Atlas Copco Air Dryer Troubleshooting Pdf: Quick Solutions
Are you struggling to figure out what’s wrong with your Atlas Copco air dryer? Maybe it’s not performing as it should, and you’re left wondering where to start.
Don’t worry—you’re not alone, and you’ve come to the right place. Finding a reliable resource like an Atlas Copco Air Dryer Troubleshooting PDF can feel like uncovering a hidden treasure, but knowing how to make the most of it is where the real magic happens.
In this post, we’ll guide you on how to effectively troubleshoot your Atlas Copco air dryer using the information in these PDFs. Whether you’re dealing with pressure drops, moisture issues, or strange noises, you’ll learn how to pinpoint the problem and take actionable steps to fix it. Keep reading, because the solution you’ve been looking for is just a few scrolls away.
Common Issues With Atlas Copco Air Dryers
Atlas Copco air dryers are essential for maintaining clean, dry compressed air in various industries. But like any equipment, they can encounter issues that disrupt performance. If you’re dealing with problems, you’re not alone—many users face common challenges that can be resolved with the right approach.
Pressure Drop Problems
Pressure drops can wreak havoc on your system’s efficiency. This typically happens when filters are clogged or pipes are too narrow. Regularly check and clean filters to keep airflow consistent.
Improper installation can also cause drops. Make sure connections are secure and there are no leaks. Have you noticed a significant dip in performance? It might be time to replace worn-out parts.
Insufficient Dew Point Performance
A poor dew point means your air isn’t as dry as it should be. This is often due to faulty sensors or a malfunctioning refrigeration system. Test the sensors periodically to ensure they’re accurate.
Another culprit? Overloading the dryer with more air than its capacity. Always match your dryer to your air demand to avoid this issue. If you’re unsure, consult your manual or an expert for guidance.
Overheating Issues
Overheating can lead to system shutdowns and costly repairs. Blocked cooling fans or dirty heat exchangers are frequent causes. Clean these components regularly to improve heat dissipation.
Improper ventilation is another factor. Ensure the dryer is in a well-ventilated area to prevent heat buildup. Is your dryer overheating despite proper maintenance? You may need to inspect the refrigerant levels.
Excessive Noise During Operation
Loud noises can be annoying and a sign of trouble. Vibrations or loose parts often cause this. Tighten any loose bolts and check for worn-out components.
Sometimes, it’s the compressor itself that’s struggling. Lubricate moving parts and inspect for wear. If the noise persists, consider scheduling a professional inspection to avoid further damage.
Are these issues sounding familiar? Tackle them early to save time and money on repairs. Proper maintenance is your best defense against recurring problems.
Basic Maintenance Tips
Maintaining your Atlas Copco air dryer helps prevent issues and ensures efficiency. Regular care extends its lifespan and keeps it performing optimally. Simple maintenance steps can save time and reduce repair costs.
Cleaning Filters Regularly
Filters trap dirt, dust, and moisture over time. Dirty filters reduce airflow and lower the dryer’s performance. Clean or replace filters based on usage or manufacturer guidelines. Use a soft brush or compressed air to remove debris. Always reinstall filters securely to avoid air leaks.
Inspecting For Leaks
Air leaks can reduce pressure and efficiency. Check hoses, valves, and connections for cracks or worn seals. Listen for hissing sounds that may indicate leakage. Replace damaged parts immediately to maintain optimal operation.
Checking Electrical Connections
Loose or damaged wires can cause malfunctions. Inspect all electrical connections for signs of wear or fraying. Tighten loose screws and connectors to ensure a stable electrical supply. Always turn off power before inspecting to prevent accidents.
Monitoring Operating Temperatures
Excess heat can damage internal components. Use a thermometer to check operating temperatures regularly. Compare readings with the manufacturer’s recommended range. Investigate overheating issues to avoid costly repairs or downtime.
Troubleshooting Steps For Airflow Issues
Airflow issues in your Atlas Copco air dryer can disrupt operations. Proper troubleshooting ensures smooth functionality and prevents costly downtime. Below are key steps for resolving airflow problems. Each step addresses common causes and provides actionable solutions.
Blocked Or Dirty Filters
Clogged filters restrict airflow, causing pressure drops and reduced efficiency. Regularly inspect the filters for dust, oil, or debris buildup. Replace dirty filters to restore proper airflow. Check the user manual for the recommended filter replacement schedule.
Improper Piping Installation
Poorly installed piping can create blockages or airflow restrictions. Ensure pipes are properly sized and aligned to avoid bends or kinks. Check for leaks or obstructions in the piping system. Use piping materials compatible with your air dryer for optimal performance.
Compressor Malfunctions
A malfunctioning compressor can disrupt airflow through the dryer. Inspect the compressor for unusual sounds, overheating, or leaks. Verify that the compressor’s pressure output matches the dryer’s requirements. Schedule regular maintenance to prevent unexpected breakdowns.
Credit: www.atlascopco.com
Solutions For Dew Point Failures
Atlas Copco air dryers are essential for maintaining optimal compressed air quality. Dew point failures can disrupt performance and lead to inefficiencies. Addressing these issues involves targeted troubleshooting steps. Below are practical solutions to fix dew point problems and ensure your air dryer operates reliably.
Refrigerant Level Check
Low refrigerant levels can impact your dryer’s cooling efficiency. Inspect the refrigerant level in the system regularly. A drop in refrigerant can cause improper dew point regulation. Use a pressure gauge to verify the refrigerant pressure. Ensure there are no leaks in the system. Refill the refrigerant if needed, following the manufacturer’s guidelines.
Sensor Calibration
Malfunctioning sensors can lead to inaccurate dew point readings. Check the dew point sensor for proper calibration. Over time, sensors may drift and provide incorrect measurements. Use a calibration kit to adjust the sensor settings. Replace the sensor if calibration doesn’t resolve the issue. Always ensure the sensor is clean and free of debris.
Heat Exchanger Maintenance
A clogged heat exchanger can reduce the dryer’s cooling performance. Inspect the heat exchanger for dirt, dust, or blockages. Clean it thoroughly to restore optimal airflow. Use compressed air or a soft brush to remove contaminants. Regular maintenance prevents buildup and extends the life of the exchanger. Check for physical damage that might affect its efficiency.
Dealing With Error Codes
Error codes on Atlas Copco air dryers can disrupt operations. Understanding these codes can save time and reduce downtime. This section helps identify, reset, and address error codes effectively.
Identifying Common Error Codes
Error codes provide specific information about the issue. Check the user manual or troubleshooting PDF to match the code with its meaning. Common codes may indicate issues like temperature imbalances or power supply interruptions. Take note of the displayed error for accurate diagnosis.
Resetting The System
When To Call Technical Support
Preventive Care Measures
Preventive care is the backbone of a well-functioning Atlas Copco air dryer. Regular maintenance can save you from unexpected breakdowns, expensive repairs, and production delays. By focusing on a few key areas, you can ensure your equipment stays in top shape for the long haul.
Scheduling Routine Inspections
Set a regular schedule to inspect your air dryer and stick to it. Even a quick check every month can help you catch small issues before they snowball into major problems. Look for visible signs like unusual noises, leaks, or inconsistent airflow.
Keep a record of each inspection. This helps you track recurring issues and identify patterns over time. If you notice parts wearing out frequently, it might be time to address the root cause.
Upgrading Outdated Components
Old components can drag down the efficiency of your air dryer. If your machine is over five years old, consider upgrading critical parts like filters, valves, and desiccants. Newer components are often more energy-efficient and designed to last longer.
Check the user manual or Atlas Copco’s website for compatible replacements. You don’t want to risk damaging your system with the wrong parts. A small investment in upgrades today can save you big on energy and repair costs tomorrow.
Training Staff For Proper Handling
Your air dryer is only as reliable as the people operating it. Are your staff trained to handle it correctly? Simple mistakes, like improper shutdowns or ignoring warning lights, can lead to costly damage.
Organize hands-on training sessions for your team. Teach them how to operate the air dryer, perform basic maintenance, and recognize early signs of trouble. When everyone knows what they’re doing, your equipment stays safer.
Preventive care isn’t just about the machine—it’s about the people and processes around it. When was the last time you evaluated your maintenance habits? A little effort now can make all the difference in keeping your Atlas Copco air dryer running smoothly.
Using The Pdf Troubleshooting Guide
Having a reliable troubleshooting guide can save you time and frustration when dealing with issues related to your Atlas Copco air dryer. The PDF troubleshooting guide is a practical tool to help you pinpoint problems and apply solutions effectively. Whether you’re a seasoned technician or just starting out, this guide simplifies the process with clear instructions.
Locating The Relevant Section
Start by identifying the exact problem with your air dryer. Is it a performance issue, an error code, or unusual noises? Once you have a general idea, open the PDF and skim the table of contents or index for keywords related to your issue. For example, if your dryer isn’t reaching the expected pressure, look for sections labeled “Pressure Issues” or “Low Efficiency.”
If you’re unsure which section applies, take a moment to read through the introduction of the guide. It often includes tips on how to narrow down common problems. This step ensures you’re not wasting time flipping through irrelevant pages.
Following Step-by-step Instructions
The PDF troubleshooting guide lays out solutions in simple, actionable steps. Follow each instruction carefully, and don’t skip steps—even if something seems obvious. For example, if the guide suggests checking the power supply before inspecting internal components, do it. Overlooking initial steps can lead to misdiagnosis.
Most guides include diagrams or photos for clarity. Use these visual aids to confirm you’re working on the correct part. If you’re unsure, pause and cross-check the description with the image. This minimizes errors and ensures you’re addressing the issue accurately.
Documenting Repairs For Future Reference
While troubleshooting, keep a record of the steps you’ve taken and any changes you’ve made. Write down details such as parts replaced, adjustments made, or error codes resolved. This documentation can help if the issue reoccurs or if you need to share information with a colleague or technician.
Consider saving a copy of the troubleshooting guide on your phone or computer for easy access. You could even highlight sections that were particularly helpful. This way, if a similar problem arises, you’ll have a quick reference ready.
Have you ever fixed something only to forget how you did it? Keeping notes ensures you won’t face the same frustration in the future. Plus, it gives you a sense of accomplishment every time you solve a problem efficiently.
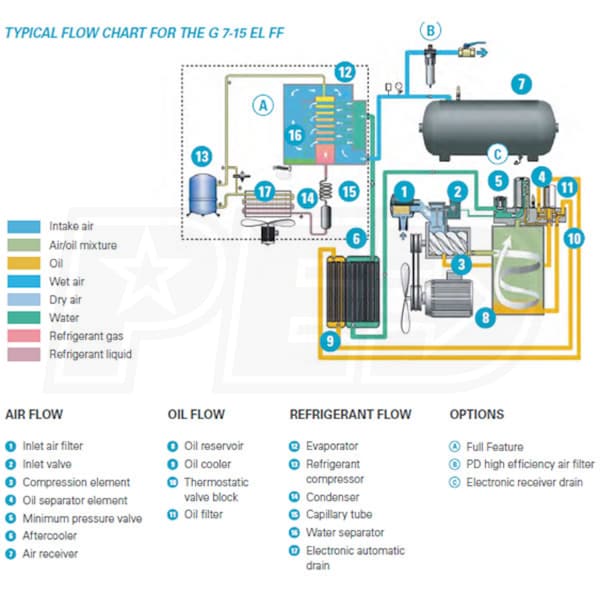
Credit: www.aircompressorsdirect.com
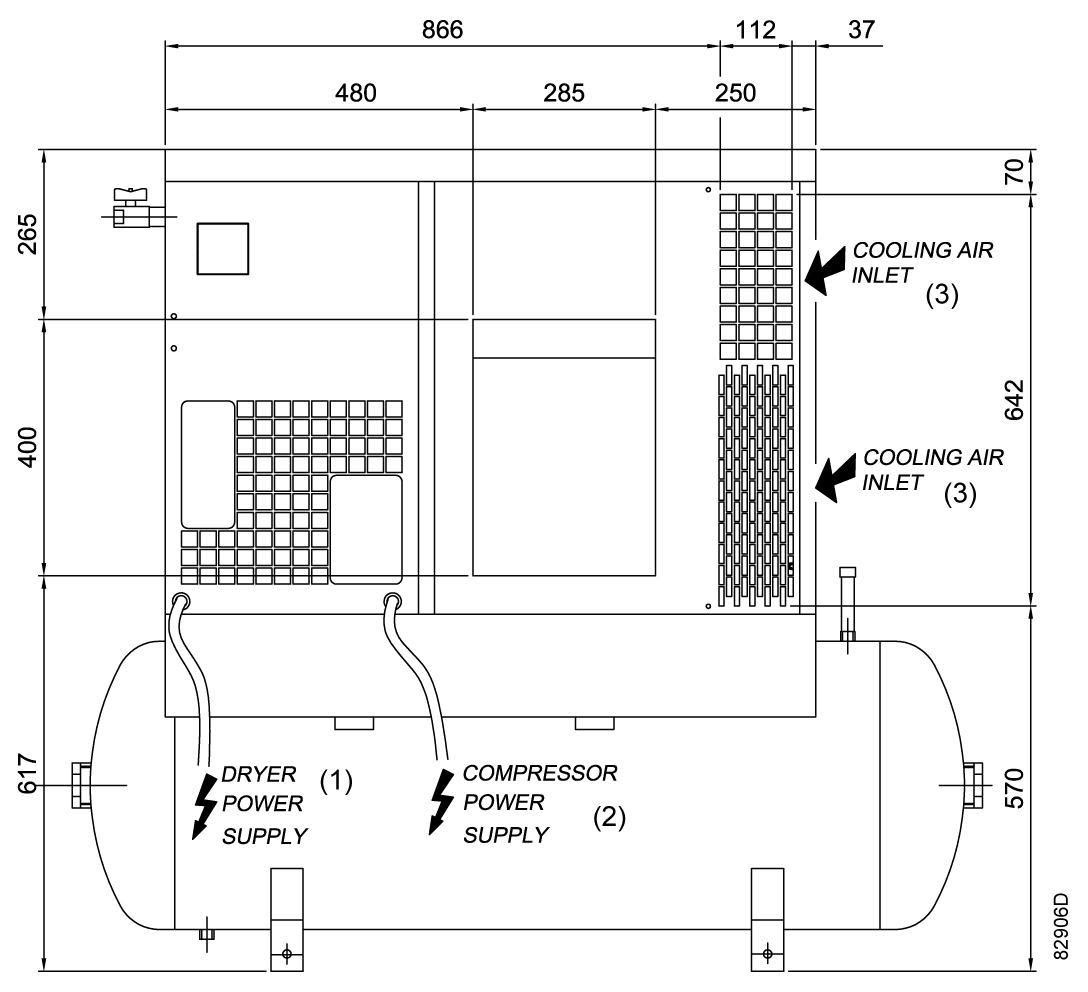
Credit: tommycarwash.zendesk.com
Frequently Asked Questions
What Are Common Issues With Atlas Copco Air Dryers?
Atlas Copco air dryers often face problems like clogged filters, refrigerant leaks, or faulty sensors causing operational errors.
How Do I Identify Air Dryer Malfunctions?
Check for unusual noises, temperature changes, or reduced airflow. Review error codes for specific issues in the system.
Can I Fix Atlas Copco Air Dryers Myself?
Basic maintenance like cleaning filters is easy. Complex repairs, like sensor replacement, may need professional help.
Where Can I Find The Troubleshooting Pdf For Atlas Copco Air Dryers?
Visit Atlas Copco’s official website or contact customer support for a downloadable troubleshooting manual.
Why Is My Air Dryer Not Cooling Properly?
Cooling issues often result from refrigerant leaks, dirty condensers, or compressor malfunction. Inspect the system for visible problems.
Conclusion
Resolving issues with Atlas Copco air dryers is simpler with the right guide. A troubleshooting PDF can save time and reduce stress during repairs. Always ensure proper maintenance to avoid frequent breakdowns. Follow the steps outlined in the manual for effective results.
Regular checks can extend the lifespan of your equipment. Address problems early to prevent costly repairs later. Reliable resources like these PDFs make the process manageable. Keep your air dryer running efficiently with consistent care and attention.