Baler Knotter Troubleshooting: Fix Common Issues Fast
Baler Knotter Troubleshooting: Simplify Your Hay Season Nothing is more frustrating than a baler knotter acting up when you’re in the middle of a busy hay season. You’re out in the field, racing against time, and suddenly, the knotter starts missing ties or jamming.
Sound familiar? You’re not alone. These issues can bring your work to a standstill, costing you time, money, and patience. But here’s the good news—you can fix most knotter problems with a little guidance. Whether you’re dealing with broken twine, uneven knots, or a knotter that just won’t cooperate, this guide is here to help.
We’ll walk you through common issues and practical solutions so you can get back to baling without unnecessary headaches. Stay with us, because understanding the root of the problem can save you countless hours and keep your baler running smoothly. Ready to take control of your baler knotter troubles? Let’s dive in.
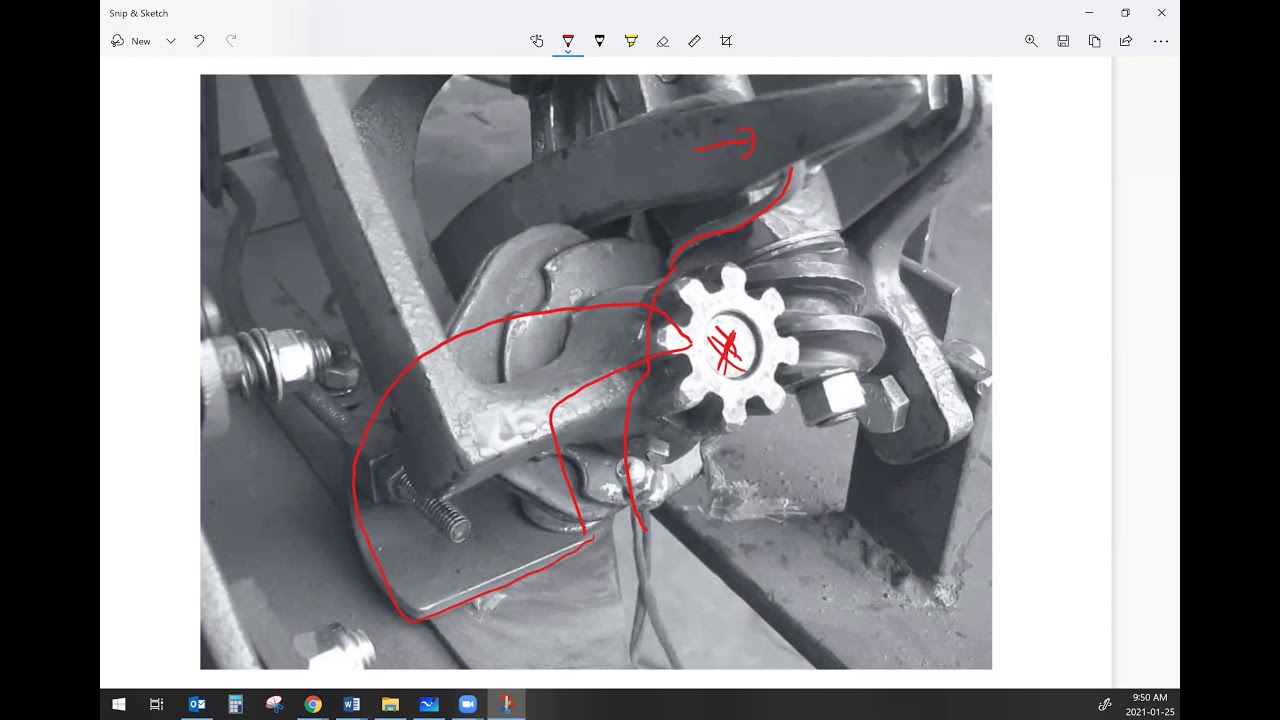
Credit: m.youtube.com
Common Knotter Problems
When your baler’s knotter isn’t working as it should, it can bring your hay baling process to a grinding halt. Common knotter problems can lead to wasted time, frustration, and even damaged crops. Understanding the root of these issues can save you headaches and keep your baler running smoothly.
Knots Not Tying Properly
One of the most frequent issues is when the knotter fails to tie a proper knot. This can happen if the twine tension is off—too loose or too tight. Check the twine tension settings and adjust them according to the baler’s manual.
Another culprit might be worn-out knotter parts. Inspect components like the billhook and twine disk for wear or damage. Replacing these parts can often solve the problem.
Dirty or debris-filled knotters can also cause trouble. Take a moment to clean the knotter mechanism thoroughly. A simple wipe-down can make a big difference.
Twine Breaking Frequently
If the twine keeps breaking, start by checking the twine quality. Low-grade twine often snaps under tension. Always opt for twine that matches your baler’s specifications.
Inspect the twine path for sharp edges or burrs. These can cut through the twine during operation. Smooth out any rough spots with a file to prevent further breaks.
Also, ensure the twine tension is not overly high. Excess tension can put unnecessary strain on the twine, causing it to break under pressure.
Missed Knots During Operation
Missed knots can slow down your baling process and lead to loose bales. One possible reason is improperly threaded twine. Double-check the threading and ensure it follows the correct path.
Worn-out or misaligned knotter parts can also result in missed knots. Regular maintenance and timely replacement of parts like the twine holder and billhook are crucial.
Lastly, consider the speed of your baler. If you’re operating too fast, the knotter may not have enough time to tie a knot. Slow down slightly and monitor the results.
Troubleshooting knotter problems doesn’t have to be overwhelming. What’s your go-to fix when the knotter acts up? Share your tips in the comments below—we’d love to hear from you!
Diagnosing Knotter Issues
The knotter is a critical component of a baler, ensuring secure knots for efficient baling. Malfunctions can lead to missed knots, tangled twine, and time-consuming delays. Diagnosing the root cause of knotter issues is essential for maintaining smooth operations and preventing downtime.
This guide focuses on three key areas: twine quality, knotter timing, and worn or damaged parts. Each area plays a vital role in knotter performance. Careful inspection can help identify the problem and restore functionality.
Inspecting Twine Quality
Twine quality directly impacts knotter efficiency. Poor-quality twine may break or fail to knot properly. Check the twine thickness and ensure it matches the baler’s specifications. Uneven twine can cause inconsistent knots and mechanical errors. Look for frays or weak spots in the twine, as these can lead to knotting failures.
Store twine in a dry, cool environment to prevent deterioration. Moist or damaged twine may lose strength and increase knotter issues. High-quality twine ensures reliable knots and smoother baling operations.
Checking Knotter Timing
Proper timing is critical for knotter performance. Misaligned timing can cause missed knots or twine jamming. Inspect the knotter’s timing mechanism and ensure it aligns with the baler’s cycle. Use the operator’s manual to check the timing specifications for your model.
Rotate the baler manually and observe the knotter’s movement. Verify that the knotter completes its cycle in sync with the plunger. Adjust the timing if necessary to prevent knotting errors. Precision in timing ensures consistent operation and reduces downtime.
Examining Worn Or Damaged Parts
Worn or damaged components can hinder knotter functionality. Inspect the knotter assembly for bent or broken parts. Pay close attention to the billhook, twine disk, and knives. These parts must be in good condition to ensure proper knot formation.
Look for signs of rust, cracks, or excessive wear. Replace damaged parts promptly to avoid further complications. Regular maintenance and part replacement extend the lifespan of the knotter and improve performance.
Fixing Twine-related Problems
Twine-related issues are common when dealing with baler knotters. They can cause missed ties, weak knots, or tangled twine. Identifying and resolving these problems ensures smooth baling and consistent performance. Below are steps to address common twine-related problems effectively.
Selecting The Right Twine
Using the correct twine type is critical for knotter efficiency. Check your baler manual to determine the recommended twine size and material. Mismatched twine can lead to knots slipping or breaking. For heavier bales, choose stronger twine that matches the load requirements. Ensure the twine is free from frays or defects before use.
Adjusting Twine Tension
Improper twine tension can cause knots to fail or twine to snap. Inspect the tension settings on your baler regularly. Loosen or tighten the tensioner to ensure smooth twine feeding. Avoid over-tightening as it may damage the twine or knotter components. Consistent tension prevents tangles and ensures reliable knot formation.
Replacing Twine Discs
Worn-out twine discs can disrupt knot formation and lead to missed ties. Check the discs for grooves, cracks, or significant wear. Replace damaged discs with compatible replacements specified in the manual. Properly aligned and clean discs ensure smooth twine gripping during knotting. Routine inspections can prevent sudden failures in the field.
Addressing Mechanical Failures
Mechanical failures in a baler knotter can bring your hay baling process to a screeching halt. Whether you’re battling misaligned parts, worn-out gears, or sticky mechanisms, these issues can feel overwhelming. But with the right steps, you can tackle them head-on and get back to baling efficiently.
Realigning Knotter Components
Misaligned knotter components are a common culprit behind knotting issues. Check if the bill hook, twine disc, and knife arm are in sync. Even a slight misalignment can cause the twine to slip or fail to knot properly.
Adjust the components so they move together smoothly. Use your baler’s manual to identify the correct alignment positions. If you’re unsure, test by slowly cycling the knotter mechanism by hand and watching for irregular movements.
Repairing Or Replacing Gears
Worn or damaged gears can disrupt the knotter’s timing. Inspect all gears for cracks, missing teeth, or excessive wear. Even small imperfections can throw off the entire operation.
If you notice damage, replace the faulty gear immediately. Make sure to use gears that are compatible with your baler model. Regularly checking and replacing worn gears can prevent bigger mechanical failures down the road.
Cleaning And Lubricating Knotter Mechanisms
Dirt, debris, and old grease can clog your knotter mechanism over time. A clogged mechanism causes unnecessary friction and can lead to skipped knots or binding issues. Have you ever noticed how even a small twig can jam up the works?
Clean out any debris with a brush or compressed air. Once clean, apply fresh lubricant to all moving parts. Use a lubricant recommended by your baler manufacturer to ensure long-lasting performance.
Regular cleaning and lubrication not only solve current problems but also prevent new ones. Make it a habit after every baling session to keep your knotter running smoothly.
Mechanical failures may seem intimidating, but they’re often easier to fix than you might think. By addressing alignment, repairing gears, and maintaining a clean mechanism, you’ll save time and frustration in the field. What’s stopping you from giving your baler knotter the attention it deserves?
Preventative Maintenance Tips
Baler knotters are essential for creating clean, secure bales. Keeping them in top shape prevents breakdowns and ensures smooth operation. Preventative maintenance is the key to extending the life of your baler knotter. By following simple maintenance steps, you can avoid costly repairs and downtime. Below are practical tips to keep your baler knotter working efficiently.
Regular Cleaning And Inspection
Dust, debris, and crop residue build up on baler knotters during operation. Regular cleaning keeps the mechanism clear and functional. Use a soft brush or cloth to remove dirt after each use. Inspect the knotter for worn or damaged parts during cleaning. Check the twine disc, bill hooks, and knives for wear or damage. Early detection prevents further issues.
Proper Storage After Use
Store your baler in a clean, dry area after use. Avoid leaving it exposed to rain or moisture. Corrosion and rust can damage knotter components over time. Cover the baler to protect it from dust and pests. Before storing, ensure the knotter is clean and free of residue. Proper storage keeps the knotter ready for the next season.
Scheduling Routine Service Checks
Regular service checks by a professional enhance knotter performance. Schedule maintenance at least once every season. Technicians can identify hidden issues before they escalate. Ensure all moving parts are lubricated during service checks. Routine inspections reduce unexpected breakdowns and prolong the knotter’s lifespan.
Credit: www.scribd.com
When To Seek Professional Help
Dealing with baler knotter problems can be frustrating and time-consuming. While some issues can be fixed with basic tools and a little patience, others may require professional expertise. Knowing when to call in a professional can save you time, money, and unnecessary stress.
Identifying Complex Issues
Not every baler knotter issue is as simple as a loose twine or a misaligned needle. If you’ve tried basic troubleshooting steps like cleaning debris, checking tension, or replacing worn parts, yet the problem persists, it might indicate a deeper issue.
Issues like consistent knot failures, broken components, or electrical malfunctions usually require expert knowledge. Ask yourself—are you confident diagnosing and fixing these problems without causing further damage?
Another red flag is recurring issues. If your knotter breaks down repeatedly after your repairs, it’s a sign that there may be underlying problems you’re not spotting.
Finding Qualified Repair Technicians
Not all repair technicians are created equal. Look for someone who specializes in balers or agricultural machinery. Many local dealers have in-house experts who are factory-trained for specific brands.
Check reviews or ask other farmers for recommendations. A good technician won’t just fix the issue; they’ll explain the cause and give you tips to prevent it in the future.
Also, confirm their availability. During peak harvest season, delays in repairs can cost you time and money, so having a technician who can respond quickly is vital.
Weighing Repair Vs Replacement Costs
Sometimes, repairs can become a financial black hole. If your baler knotter has been repaired multiple times and still doesn’t work efficiently, it’s worth calculating the long-term costs.
Compare the price of ongoing repairs with the cost of replacing the knotter or even upgrading your baler. A newer model may offer better performance and fewer headaches down the line.
Ask the technician for their honest opinion. They often have a clear idea of whether a repair will be a temporary fix or a lasting solution.
When deciding, think about downtime too. A faulty knotter can slow your operations, leading to missed deadlines and reduced productivity. Is it worth sticking with an unreliable component?
Remember, seeking professional help doesn’t mean you’ve failed. It’s about making smart decisions to keep your baler running smoothly and your harvest on schedule.
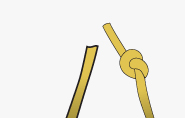
Credit: www.bridon-usa.com
Conclusion
Fixing baler knotter issues takes patience and attention to detail. Regular maintenance prevents most problems and keeps your machine running smoothly. Always check for worn parts and replace them when needed. Clean your knotter regularly to avoid debris buildup. Follow the manufacturer’s guide for adjustments and repairs.
Troubleshooting step by step saves time and effort. A well-maintained baler ensures better performance and reliable results. Keep these tips handy for future reference. Proper care today means fewer problems tomorrow. Stay proactive, and your baler will serve you well for years.