Bendix Air Dryer Troubleshooting: Expert Tips for Quick Fixes
Bendix air dryers are essential for truck and bus air systems. They ensure moisture-free air, preventing damage.
But what happens when things go wrong? Understanding how to troubleshoot a Bendix air dryer can save you time and money. A functioning air dryer maintains the efficiency of your vehicle’s air system, preventing costly repairs. This guide will help you identify common issues and their solutions.
From leaks to pressure problems, we’ll cover the basics. Knowing these troubleshooting steps ensures your vehicle runs smoothly and safely. Let’s dive into the world of Bendix air dryers and keep your air system in top shape.
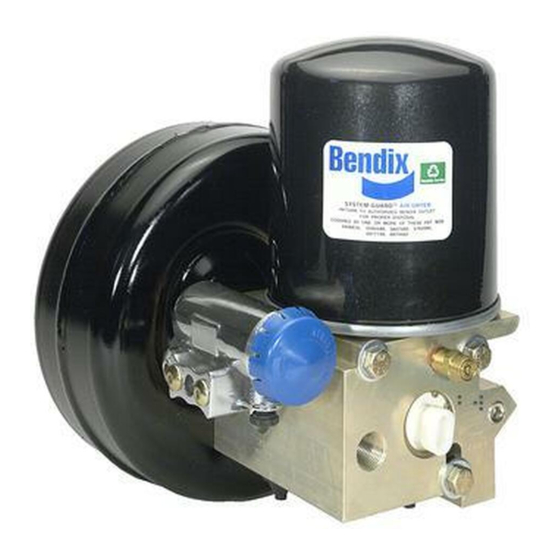
Credit: www.manualslib.com
Common Issues
Understanding common issues with Bendix air dryers can help maintain optimal performance. Addressing these problems promptly ensures safety and efficiency.
Leaking Air
Leaking air is a frequent issue with Bendix air dryers. It can cause a drop in system pressure. Inspect connections and fittings for any loose parts. Tighten or replace them if needed. Damaged O-rings or seals might also cause leaks. Regularly check and replace these components. Leaks can lead to bigger problems if ignored.
Excessive Noise
Excessive noise from the Bendix air dryer can indicate an internal issue. A malfunctioning purge valve is a common cause. Check the purge valve for debris or damage. Clean or replace it if necessary. A noisy compressor might also be the culprit. Regular maintenance can prevent such issues. Keep an ear out for unusual sounds.
Tools Needed
To effectively troubleshoot a Bendix air dryer, having the right tools is essential. Using the correct tools ensures a smooth and successful repair process. This section details the tools needed, from basic hand tools to specialized equipment.
Basic Hand Tools
Every mechanic’s toolbox should have basic hand tools. These include wrenches, screwdrivers, and pliers. These tools help you remove and replace parts. A socket set is also important for loosening and tightening bolts. Ensure you have a variety of sizes for different components.
Specialized Equipment
For Bendix air dryer troubleshooting, specialized equipment is often needed. A multimeter is crucial for checking electrical connections. It helps you identify shorts or faulty wires. An air pressure gauge is also important. This tool measures the air pressure in the system to ensure it is within the correct range.
Another useful tool is a diagnostic scanner. This device reads error codes from the air dryer’s control unit. It helps pinpoint specific issues quickly. Lastly, having a good quality flashlight can help you see in tight or dark spaces.
By having these tools on hand, you can efficiently diagnose and repair your Bendix air dryer. This makes the entire troubleshooting process much smoother.
Safety Precautions
Ensure safety by wearing protective gear while troubleshooting the Bendix air dryer. Disconnect all power sources before beginning. Use proper tools to avoid accidents.
Working on a Bendix air dryer requires strict safety precautions. These precautions ensure your safety and the proper functioning of the equipment. Adhering to them can prevent accidents and equipment damage.
Personal Protective Equipment
Always wear appropriate personal protective equipment (PPE). This includes safety glasses to protect your eyes from debris. Gloves are essential to protect your hands from sharp edges. Wear sturdy footwear to protect your feet from heavy objects. Use a face mask to prevent inhalation of dust and particles.
Proper Ventilation
Ensure the workspace has proper ventilation. Good airflow prevents the buildup of harmful fumes. It also keeps the area comfortable to work in. Open windows and use fans if necessary. A well-ventilated area is crucial for safety and health.
“`
Initial Inspection
During the initial inspection of your Bendix air dryer, a few basic checks can help identify common issues. This process involves examining the air dryer for any visible signs of trouble. It also includes testing specific components to ensure they function correctly.
Visual Check
Start by examining the exterior of the air dryer. Look for any signs of damage or wear. Check for cracks, dents, or loose connections. Ensure all hoses and fittings are secure. Any visible damage could indicate a problem that needs attention.
Component Testing
After the visual check, move on to testing the components. Begin with the purge valve. Ensure it operates smoothly and does not leak. Next, test the heater and thermostat. They should activate correctly and maintain the proper temperature.
Also, check the desiccant cartridge. It should be dry and free of oil. A wet or oily cartridge may indicate a compressor issue. Verify that the pressure relief valve opens at the correct pressure. This prevents over-pressurization and potential damage.
Diagnosing Leaks
Diagnosing leaks in a Bendix air dryer can be a challenging task. Leaks can cause performance issues and lead to system failures. Understanding how to diagnose these leaks is crucial. This section will guide you through identifying leak sources and temporary fixes.
Identifying Leak Sources
Start by listening for hissing sounds. These sounds often indicate a leak. Use soapy water to spray on the suspected areas. Bubbles will form where there is a leak. Check connections, fittings, and hoses. Inspect the purge valve for any signs of wear or damage. Examine the air dryer’s desiccant cartridge. Look for moisture or oil, which may signal a leak.
Temporary Fixes
Sometimes, you need a quick fix before permanent repairs. Use Teflon tape on leaking threads. This can help seal small leaks. Tighten loose fittings with a wrench. Ensure not to over-tighten. For hose leaks, use a hose clamp as a temporary measure. Seal cracks in hoses with rubber adhesive tape. Remember, these fixes are only temporary. Permanent repairs are necessary to ensure system reliability.
Credit: mhhauto.com
Addressing Noise
Noise from your Bendix air dryer can be annoying and a sign of trouble. Fixing this noise is essential for optimal performance. This section will help you understand and fix noise issues.
Isolating Noise Causes
Start by identifying the source of the noise. Is it a grinding sound or a hissing noise? Different sounds indicate different problems.
Use these steps to isolate the cause:
- Listen carefully to identify the type of noise.
- Inspect the air dryer for visible damage.
- Check connections and fittings.
A grinding noise often means a mechanical issue. A hissing noise may indicate an air leak. Both require different solutions.
Lubrication Solutions
Proper lubrication can solve many noise issues. Check the manufacturer’s guidelines for the right type of lubricant.
Follow these steps for lubrication:
- Turn off the air dryer.
- Clean the lubrication points.
- Apply the recommended lubricant.
- Restart the air dryer.
Regular lubrication keeps your air dryer running smoothly. This reduces noise and extends the life of the unit.
Routine Maintenance
Routine maintenance of your Bendix air dryer ensures it works efficiently. Regular checks and services help avoid unexpected breakdowns. Follow these simple steps to keep your system in top shape.
Filter Replacement
Replacing the filter is crucial for smooth air dryer operation. A clogged filter can reduce performance. Check and replace the filter every 12 months. Always use Bendix-approved filters for best results. This simple task can prevent bigger issues.
System Flushing
System flushing removes contaminants from the air dryer. This process should be done every two years. Use a proper cleaning solution for the best results. Flushing helps maintain the efficiency of the system. It also extends the lifespan of your air dryer.

Credit: www.yumpu.com
When To Seek Professional Help
Seek professional help if the Bendix air dryer shows persistent issues like abnormal noises, frequent cycling, or moisture in the system. Expert intervention ensures proper diagnosis and repair, preventing further damage.
Sometimes, Bendix air dryer issues need expert intervention. Knowing when to call a professional can save time and money. It can also prevent further damage to your system. Below are some scenarios where professional help is advisable.
Complex Repairs
Air dryers have many components. Some repairs might be too complex for a DIY approach. If you face issues like electrical faults, seek a technician. They have the right tools and knowledge to fix the problem. This ensures your air dryer works efficiently.
Warranty Considerations
Using a professional can help maintain your warranty. Many warranties require repairs by certified technicians. DIY repairs might void the warranty. Always check your warranty terms. This could save you from costly repairs in the future.
“`
Frequently Asked Questions
What Are Common Bendix Air Dryer Issues?
Common issues include air leaks, frozen dryers, and clogged filters. Regular maintenance helps prevent these problems.
How Do I Fix A Bendix Air Dryer Leak?
Inspect and tighten fittings. Replace damaged parts. Use soapy water to locate leaks.
Why Is My Bendix Air Dryer Freezing?
Freezing occurs due to moisture buildup. Drain the air tanks regularly and check the dryer heater.
How Often Should I Service My Bendix Air Dryer?
Service the air dryer every 12 months or 100,000 miles, whichever comes first. Regular checks are important.
What Causes A Bendix Air Dryer To Clog?
Clogs are caused by dirt and oil. Regularly replace filters and clean components to prevent clogging.
Conclusion
Proper troubleshooting ensures your Bendix air dryer works efficiently. Regular maintenance is key. Address issues promptly to avoid bigger problems. Clean components regularly to extend lifespan. Replace parts as needed for smooth operation. Keep an eye on warning signs. A well-maintained air dryer saves time and money.
Stay proactive and informed. Your vehicle’s performance depends on it. Follow these tips for a reliable air dryer. Happy driving!