Digi-Star Scale Troubleshooting: Expert Tips & Solutions
Are you dealing with a Digi-Star scale that’s not working as it should? It can be frustrating when your equipment doesn’t perform optimally, especially when precision is crucial.
You’ve invested in this technology to save time and improve accuracy, but technical hiccups can throw a wrench in your plans. Don’t worry—you’re not alone in facing these challenges. In this guide, we’ll dive into practical troubleshooting tips tailored just for your Digi-Star scale.
By the end of this article, you’ll feel more confident in tackling these issues head-on, ensuring that your scale runs smoothly and efficiently. Stick with us, and let’s get your Digi-Star scale back on track!
Common Issues With Digi-star Scales
Dealing with Digi-Star scales can sometimes feel like untangling a mystery. These scales, known for their precision and reliability, occasionally face hiccups that can disrupt your workflow. Understanding common issues can save you time and frustration. Let’s dive into some of the most frequent problems and how you can address them effectively.
Error Messages And Their Meanings
Encountering error messages on your Digi-Star scale can be baffling. Each message serves a specific purpose, guiding you towards resolving the issue. For instance, if you see “Err 1,” it typically means there’s an overload condition. This is your cue to check the weight and ensure it’s within the scale’s capacity.
Another common error is “Err 2,” which often indicates a calibration issue. This might happen if the scale was moved or bumped. Recalibrating the scale usually fixes this problem. Have you ever ignored these messages, thinking they were inconsequential? Next time, pay attention—they’re your scale’s way of communicating.
Inaccurate Weight Readings
Are you experiencing inaccurate weight readings? This can be a real headache, especially when precision matters. One reason could be uneven surfaces. Always ensure your scale is placed on a flat, stable surface to avoid skewed readings.
Another culprit might be environmental factors like temperature fluctuations. If you notice weight discrepancies, check if your scale is exposed to direct sunlight or drafts. Adjusting the environment can often bring accuracy back on track. Have you considered how environmental changes might be impacting your scale readings?
Connectivity Problems
Connectivity issues can halt your progress in seconds, especially if you’re relying on your scale to transmit data to another device. If your Digi-Star scale isn’t connecting, start by checking the cables and connections. A loose cable can be the simplest fix.
Wireless connectivity issues might require a closer look at your network settings. Ensure your scale is within the range of your network and that the settings are correctly configured. Have you tried restarting your devices? Sometimes, a simple reset can restore connections and save you from unnecessary headaches.
Tackling these common issues doesn’t have to be overwhelming. By understanding the root causes and applying these practical solutions, you can ensure your Digi-Star scale continues to deliver reliable results. What’s your experience with these scales? Share your insights and tips in the comments below!
Step-by-step Troubleshooting Guide
Troubleshooting a Digi-Star scale can seem daunting at first, but with the right guidance, you can quickly get your scale back to peak performance. This step-by-step troubleshooting guide will walk you through common issues and solutions. Whether you’re a seasoned pro or new to scale maintenance, these actionable steps can make your task easier and more efficient.
Initial Diagnostic Checks
Start by inspecting the scale’s display and connections. Check for any error messages or unusual symbols on the screen. Ensure all cables are securely connected and free from damage.
Power interruptions can be a common issue. Verify that the power source is stable and the scale is properly plugged in. If the display is blank, try using a different power outlet.
Look for physical obstructions around the scale platform. Debris can interfere with accurate readings. A quick clean-up might be all it takes to resolve the issue.
Resetting The Scale System
If initial checks don’t solve the problem, resetting the system can be a helpful next step. Power off the scale completely. Wait for a few seconds before turning it back on.
Sometimes, a simple reset can clear minor software glitches. After restarting, observe the scale’s behavior to see if the issue persists.
Always refer to the user manual for model-specific reset instructions. This ensures you follow the correct procedure without causing additional problems.
Calibrating The Scale
Calibration is crucial for maintaining accurate measurements. Begin with an empty scale and ensure it’s on a flat, stable surface. Use certified weights for the calibration process.
Follow the calibration instructions specific to your Digi-Star model. It usually involves accessing the settings menu and following a series of prompts.
Accurate calibration can prevent future errors and improve the reliability of your scale. Regular calibration checks can save you time and hassle down the road.
Have you ever found yourself questioning the accuracy of your scale readings? Addressing these key areas can help you regain confidence in your equipment. Taking the time to troubleshoot effectively can lead to better efficiency and peace of mind.
Maintenance Best Practices
Troubleshooting Digi-Star scales requires regular inspections and calibrations to ensure accuracy. Clean connectors and cables to prevent errors. Testing with known weights helps identify discrepancies, ensuring reliable performance.
Maintaining your Digi-Star scale is essential to ensure its longevity and precision. Neglecting maintenance can lead to inaccuracies and costly downtime. By adopting best practices, you can keep your scale functioning optimally and avoid frustrating troubleshooting situations. Let’s explore how regular cleaning, firmware updates, and proper battery care can make a significant difference.Regular Cleaning And Inspection
Regular cleaning is vital for your scale’s accuracy. Dust and debris can interfere with its sensors, leading to incorrect readings. Use a soft brush or cloth to remove dirt. Avoid harsh chemicals; they may damage the equipment. Inspect your scale frequently. Check for wear and tear on cables and connectors. A quick look can save you from potential failures.Updating Firmware
Firmware updates are crucial for the smooth operation of your Digi-Star scale. Updates often fix bugs and improve performance. Check for updates regularly. Manufacturers release them to enhance functionality. Install updates promptly. You wouldn’t want your scale operating on outdated software, would you?Battery Care Tips
Battery care is another critical aspect of scale maintenance. An unreliable battery can disrupt your operations. Use quality batteries. Cheap ones may drain faster, affecting your scale’s performance. Regularly check battery contacts for corrosion. Clean them as needed to ensure proper connection. Engaging with your Digi-Star scale means more than just using it. It’s about understanding its needs and addressing them proactively. Do you have any personal tips that have worked wonders for your scale maintenance?Credit: support.scale-tec.com
Advanced Solutions For Persistent Issues
Even with regular maintenance, Digi-Star scales can face persistent issues. Advanced solutions might be necessary for complex problems. These solutions can guide you through difficult troubleshooting scenarios.
Consulting Customer Support
Customer support can be a valuable resource. They offer expert advice tailored to your situation. Contact them if basic troubleshooting fails. They can provide insights into common issues. This can save time and prevent further damage.
Replacing Faulty Components
Faulty components might cause persistent scale issues. Identifying and replacing these parts is crucial. Consult the user manual for guidance. Only use compatible components for replacements. This ensures the scale functions correctly.
Using External Diagnostic Tools
External diagnostic tools can help pinpoint problems. These tools can identify hidden issues. Investing in a good diagnostic tool is beneficial. It can provide detailed insights into the scale’s performance. This leads to more accurate troubleshooting.
Pro Tips From Industry Experts
Discover essential tips from industry experts for Digi-Star Scale troubleshooting. Quickly identify common issues and implement practical solutions. Ensure accurate measurements by understanding key maintenance practices.
In the world of agriculture and industrial operations, Digi-Star scales are a trusted tool for precision. But like any piece of equipment, they may face issues over time. To keep your scales running smoothly and efficiently, industry experts offer some valuable insights. These pro tips can help you prevent common problems, optimize performance, and ensure your team is using the equipment correctly.Preventive Measures For Longevity
Preventing issues before they arise is always a smart strategy. Regular maintenance is crucial. Make it a habit to inspect the scales for any signs of wear or damage. Check cables and connections for corrosion or fraying. Consider environmental factors. If your scales are exposed to harsh conditions, such as moisture or dust, protective measures can extend their lifespan. Simple actions like covering the scale when not in use or installing it in a sheltered location can make a significant difference. A scale that is consistently overloaded can break down faster. Ensure that the weight limits are respected to prevent unnecessary strain on the device. Following these preventive measures can save you both time and money in repairs.Optimizing Scale Performance
Performance optimization is about getting the most accurate and reliable readings from your scales. Calibration is key. Regularly calibrate your scales to ensure their accuracy, especially if they are moved frequently or used in different locations. Think about the surface where your scale sits. An uneven surface can cause inaccurate measurements. Use a level to ensure your scales are perfectly balanced. Software updates shouldn’t be ignored. Keeping the scale’s software up-to-date can improve functionality and provide fixes for known bugs. It’s a small step that can lead to better performance.Training Staff On Proper Usage
Proper usage is critical to the longevity and performance of your scales. Ensure that all users are trained on the correct operation of the equipment. A short training session can prevent costly mistakes and extend the life of the scale. Consider creating a simple manual or guide for your team. Include basic troubleshooting steps and best practices for using the scales. This can be a valuable resource for new staff or as a refresher for experienced users. Encourage open communication. If team members notice any issues or have questions about the scales, they should feel comfortable bringing them up. Prompt attention to potential problems can prevent them from becoming serious. Are there practices you have found particularly effective in your operations? Sharing insights and learning from others can lead to a well-maintained, efficient workspace.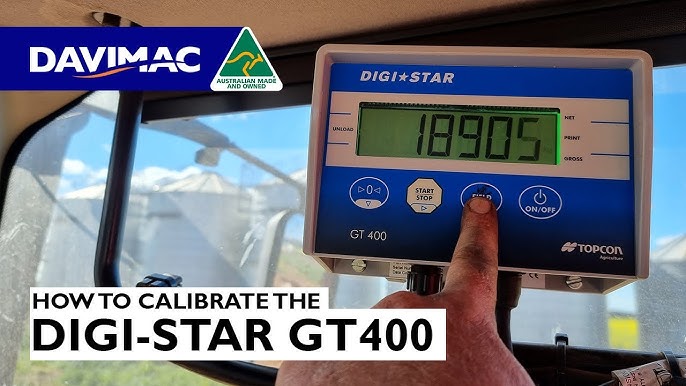
Credit: www.youtube.com

Credit: www.topconpositioning.com
Conclusion
Troubleshooting Digi-Star scales doesn’t need to be difficult. Follow the steps. Identify common issues. Check connections and settings. Ensure all components work properly. Regular maintenance helps prevent problems. Understand your scale’s functions. This boosts efficiency and accuracy. Keep this guide handy.
It will save time and frustration. With patience and practice, you’ll manage any issues. Reliable scales mean better results. Happy weighing!