Epilog Laser Troubleshooting: Expert Tips for Quick Fixes
Epilog Laser systems are powerful tools used for engraving and cutting. Like any complex equipment, they sometimes face issues.
Understanding how to troubleshoot these problems can save time and frustration. Laser systems can be tricky to diagnose. Issues may arise from software glitches, hardware malfunctions, or improper settings. Knowing the common problems and their solutions can keep your projects on track.
This guide will walk you through typical troubleshooting steps for Epilog Laser systems. We’ll cover common errors and how to fix them, ensuring you get back to your work with minimal downtime. Whether you’re a beginner or experienced user, these tips will help maintain your laser system’s performance. Ready to dive in? Let’s get started!

Credit: www.youtube.com
Common Issues
Using an Epilog Laser can be a great way to create precise cuts and engravings. However, users might face common issues that can disrupt the workflow. This section will help you identify and troubleshoot some of these common problems.
Power Problems
Power problems can arise from various sources. Ensuring your laser has stable power is essential.
- Check the power cord: Make sure it is securely connected to both the laser and the wall outlet.
- Inspect the power supply: Confirm it is working correctly. Use a multimeter to check for consistent voltage.
- Power button: Ensure it is functional and not stuck.
Sometimes, the laser might not turn on due to a blown fuse. Check the user manual for the fuse location and replace it if necessary.
Connectivity Issues
Connectivity issues can prevent your computer from communicating with the laser. This can stop your project in its tracks.
- USB cable: Make sure it is connected properly. Try a different USB port on your computer.
- Network connection: If using a network connection, ensure the laser and computer are on the same network.
- Driver software: Confirm the driver software is installed and updated. Reinstall it if needed.
Sometimes, a simple restart of both the computer and the laser can resolve connectivity issues.
Laser Not Cutting
Having issues with your Epilog Laser not cutting? This can be frustrating. Several factors could cause this problem. Let’s explore the common solutions. Cleaning the lens and aligning the mirrors often solve the problem.
Lens Cleaning
Dirty lenses can block the laser beam. This reduces its cutting power. Check the lens regularly. Use a lens cleaning solution. Gently wipe the lens with a soft cloth. Avoid scratching the lens. Clean the lens after each use. This ensures consistent performance.
Mirror Alignment
Misaligned mirrors can also affect cutting. They direct the laser beam. Any misalignment can weaken the beam. Check the mirrors’ positions. Adjust them if needed. Follow the manufacturer’s instructions. Use alignment tools if available. Proper alignment maximizes laser efficiency.
Software Errors
Software errors can significantly impact your laser engraving projects. They often disrupt workflow and cause frustration. Understanding these errors helps in troubleshooting and resolving them quickly. The most common issues relate to driver updates and compatibility checks. Let’s delve into these areas to ensure your Epilog Laser functions smoothly.
Driver Updates
Drivers are essential for your Epilog Laser to communicate with your computer. Outdated drivers can cause software errors and malfunctions. Always keep your drivers up-to-date to avoid these problems. Here’s how you can update your drivers:
- Visit the official Epilog Laser website.
- Navigate to the Support section.
- Download the latest driver for your model.
- Follow the installation instructions carefully.
Regularly updating drivers enhances performance and resolves compatibility issues. Make it a habit to check for updates periodically.
Compatibility Checks
Ensuring compatibility between your Epilog Laser and your computer system is crucial. Incompatibility can lead to frequent software errors. Here are some steps to check compatibility:
- Check the system requirements on the Epilog Laser website.
- Ensure your operating system matches the requirements.
- Verify that your software version is up-to-date.
- If needed, upgrade your computer hardware.
Compatibility checks prevent a range of errors and ensure smooth operation. Always confirm compatibility before starting a project.
Proper maintenance of your Epilog Laser’s software is key to avoiding errors. Keep your drivers updated and ensure compatibility to maintain efficiency and productivity.
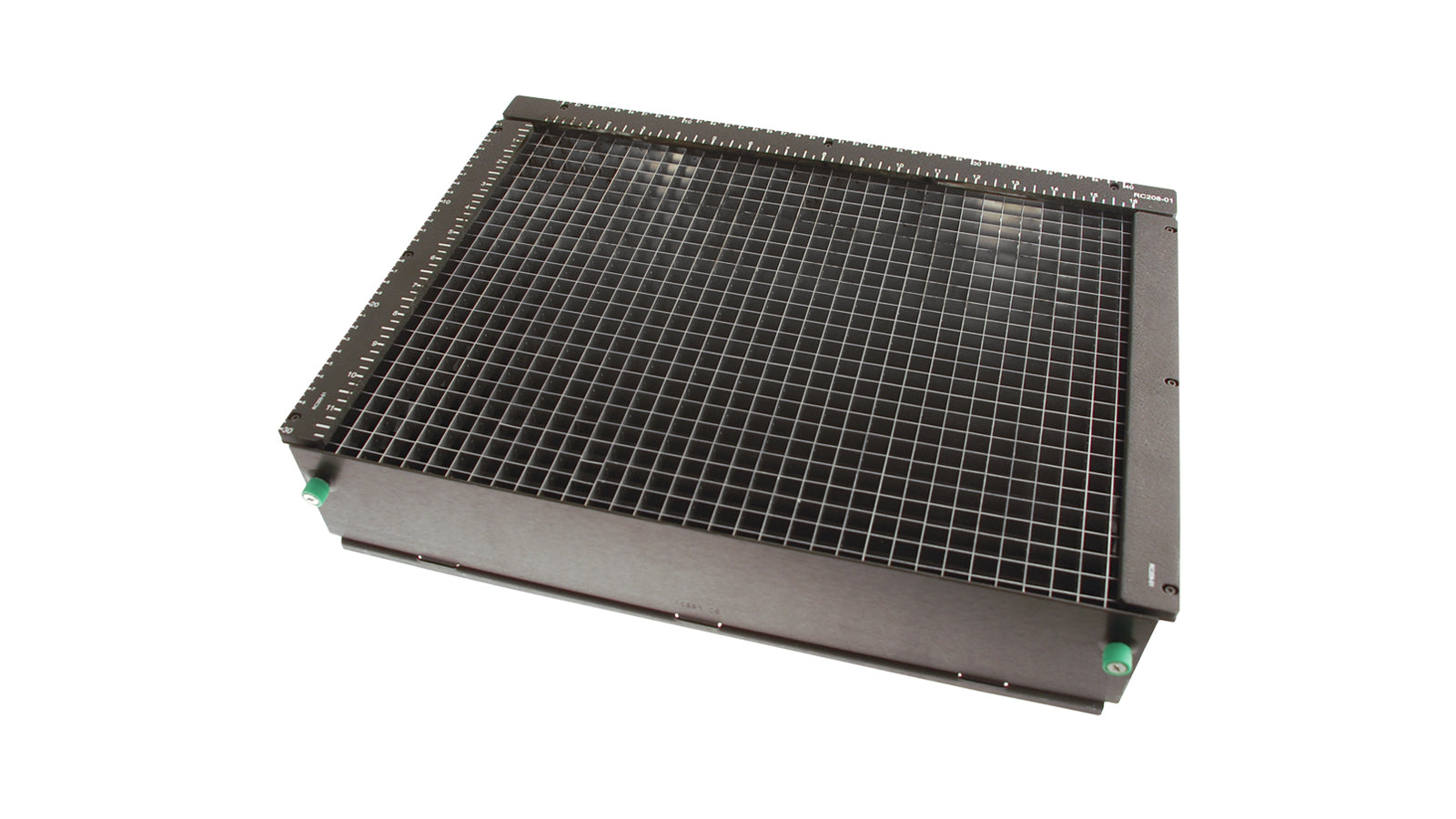
Credit: shop.epiloglaser.com
Engraving Problems
Engraving issues can disrupt the quality of your work. This section will guide you through common problems and their solutions. Read on to identify and fix these issues effectively.
Incorrect Settings
The settings on your Epilog Laser play a crucial role in engraving quality. Incorrect settings can lead to poor results. Adjusting these settings can make a significant difference.
- Speed: Check if the speed is set too high. A high speed can result in shallow engravings.
- Power: Ensure the power is adequate for your material. Low power might not engrave deeply enough.
- Resolution: Set the resolution according to the detail required. High resolution is better for detailed designs.
Material Issues
The material you use can also impact engraving quality. Different materials require different settings and handling.
Material | Common Issues | Solutions |
---|---|---|
Wood | Burn marks | Use masking tape to reduce burns |
Acrylic | Melting | Lower the power and increase speed |
Metal | Inconsistent marks | Ensure the metal is coated properly |
Always test your material before starting a project. Adjust the settings based on your tests to achieve the best results.
Overheating
Overheating can be a major issue for your Epilog Laser. It can lead to equipment damage and poor performance. Keeping your laser at optimal temperature is crucial for its longevity and efficiency. Let’s explore some solutions to prevent overheating.
Cooling System Check
One of the first steps is to inspect the cooling system. The cooling system is vital for maintaining an optimal temperature.
- Check if the cooling fan is working properly.
- Ensure there are no blockages in the cooling vents.
- Inspect the coolant level and refill if necessary.
If the cooling system is not functioning correctly, the laser can overheat quickly. Regularly checking these components can prevent major issues.
Ventilation Solutions
Proper ventilation is essential to avoid overheating. Lack of airflow can cause the laser to heat up.
Solution | Description |
---|---|
Install Exhaust Fans | Exhaust fans help remove hot air from the workspace. |
Use Air Conditioning | Air conditioning helps maintain a cool environment. |
Open Windows | Ensures fresh air circulates in the room. |
Implementing these solutions can significantly reduce the risk of overheating. Always ensure your workspace is well-ventilated to maintain the efficiency of your Epilog Laser.
Laser Tube Issues
The laser tube is the heart of your Epilog Laser. It generates the laser beam that does the cutting and engraving. Over time, the tube may face issues that can affect the performance of your machine. Here, we discuss two common problems: Tube Replacement and Tube Alignment.
Tube Replacement
An old or faulty tube can lead to weak laser output. Signs that you need a tube replacement include:
- Weak or inconsistent laser beam
- Visible damage or cracks on the tube
- Frequent power fluctuations
To replace the tube, follow these steps:
- Turn off and unplug the laser machine.
- Remove the access panel to reach the laser tube.
- Disconnect the wires attached to the old tube.
- Carefully remove the old tube and replace it with a new one.
- Reconnect the wires and reattach the access panel.
Always ensure you use a compatible tube for your specific model.
Tube Alignment
Proper alignment of the laser tube is crucial for optimal performance. Misalignment can lead to poor cutting and engraving results. To check and correct the alignment:
- Power off the machine and remove the access panel.
- Use a laser alignment tool to check the beam path.
- Adjust the tube’s position until the beam hits the target center.
- Tighten the screws to secure the tube in place.
- Replace the access panel and test the machine.
Regular alignment checks can prevent many common issues.
Maintenance Tips
Maintaining your Epilog Laser system is crucial for optimal performance. Regular maintenance can prevent common issues and extend the lifespan of your equipment. Follow these maintenance tips to keep your laser machine running smoothly.
Regular Cleaning
Regular cleaning is essential for the efficiency of your Epilog Laser. Dust and debris can build up and affect the machine’s performance. Here are some steps to follow:
- Clean the lens and mirrors weekly with the recommended cleaning solution.
- Wipe down the machine’s exterior to remove dust and dirt.
- Vacuum the interior of the machine to clear out any debris.
Scheduled Inspections
Regular inspections ensure that your machine is in good working order. Schedule these inspections to identify any potential issues early:
- Monthly inspection: Check the alignment of the laser beam.
- Quarterly inspection: Inspect the belts and gears for wear and tear.
- Yearly inspection: Have a professional service technician perform a thorough checkup.
Inspection Type | Frequency | Task |
---|---|---|
Lens and Mirror Cleaning | Weekly | Use recommended solution |
Machine Vacuuming | Weekly | Clear out debris |
Laser Beam Alignment | Monthly | Check and adjust |
Belts and Gears Inspection | Quarterly | Inspect for wear |
Professional Checkup | Yearly | Comprehensive inspection |
Technical Support
Technical support is crucial for maintaining your Epilog Laser equipment. Effective support ensures that your machine runs smoothly. It also helps in resolving any issues quickly. Understanding how to get this support is important for all users.
Contacting Epilog
If you face any issues, contacting Epilog is your first step. Their support team is knowledgeable and ready to help. You can reach them via phone or email. Each method provides timely assistance. Always have your machine’s serial number ready. This helps the team assist you faster. You can find contact details on the Epilog website. Support is available during business hours.
Warranty Information
Warranty information is vital for Epilog Laser owners. Knowing your warranty coverage can save you money. Warranties often cover parts and labor for a specific time. Always check the warranty details when you buy the machine. This ensures you understand what is covered. If your machine is under warranty, repairs might be free. Keep all warranty documents in a safe place. You will need them if you require service.
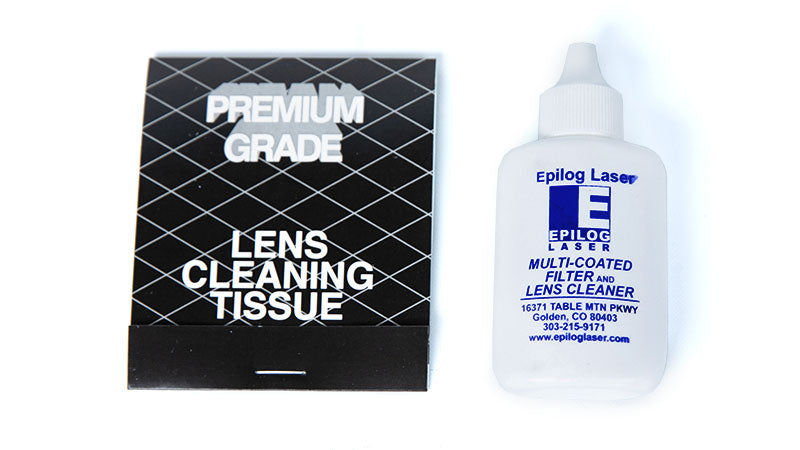
Credit: shop.epiloglaser.com
Frequently Asked Questions
Why Is My Epilog Laser Not Cutting Properly?
Check your lens and mirrors for dirt. Also, ensure your settings match the material type and thickness.
How Do I Clean My Epilog Laser?
Use a lint-free cloth and isopropyl alcohol. Gently wipe the lens and mirrors.
What Should I Do If My Laser Is Not Firing?
Check the laser tube and power supply. Ensure all connections are secure and there are no loose wires.
Why Is My Engraving Uneven?
Make sure the material is flat. Check the bed level and adjust if necessary.
How Often Should I Perform Maintenance On My Epilog Laser?
Perform basic cleaning weekly. Full maintenance, including lens and mirror checks, should be done monthly.
Conclusion
Troubleshooting your Epilog Laser can be simple with the right steps. Identify the problem first. Then follow the manual for specific solutions. Regular maintenance helps prevent issues. Clean the lens and mirrors often. Use proper materials to avoid damage. If problems persist, contact customer support.
They can offer expert advice. Remember, a well-maintained laser ensures optimal performance. Happy engraving!