Fanuc Troubleshooting Codes: Mastering Quick Solutions
Understanding Fanuc troubleshooting codes is crucial for minimizing machine downtime. These codes help identify and resolve issues quickly.
Fanuc machines are integral to many manufacturing processes. When they malfunction, troubleshooting codes provide essential information to diagnose and fix problems. This guide will explain these codes and how to interpret them. By understanding these codes, you can keep your equipment running smoothly and efficiently.
Recognizing the meaning behind these codes reduces guesswork and saves valuable time. Whether you’re new to Fanuc machines or an experienced user, knowing how to decode these messages is vital. This introduction will set the stage for a deeper dive into Fanuc troubleshooting codes, helping you maintain optimal machine performance.
Credit: www.linkedin.com
Introduction To Fanuc Codes
Understanding Fanuc troubleshooting codes is crucial for any professional working with Fanuc CNC machines. These codes help diagnose and fix issues quickly, ensuring minimal downtime. This guide provides an overview of these codes, their importance, and common issues.
Importance Of Understanding Codes
Fanuc codes are essential for maintaining smooth operations. They identify specific problems within the CNC system. Knowing these codes allows technicians to troubleshoot effectively. It saves time and reduces machine downtime.
Understanding these codes can also improve overall machine performance. Regular maintenance based on these codes can prevent future issues. It ensures the longevity of the equipment.
Common Issues
Several common issues can arise with Fanuc CNC machines. Here are some typical problems and their corresponding codes:
- Alarm 100: Emergency Stop – Indicates a manual emergency stop has been activated.
- Alarm 101: Overtravel – The machine has exceeded its travel limits.
- Alarm 300: Spindle Malfunction – There is an issue with the spindle operation.
- Alarm 500: Servo Error – A problem with the servo motor or its control system.
Addressing these issues promptly can prevent more serious damage. It also ensures the machine operates efficiently and safely.
Common Fanuc Codes
Code | Description |
---|---|
100 | Emergency Stop |
101 | Overtravel |
300 | Spindle Malfunction |
500 | Servo Error |
These codes are the most frequently encountered. Familiarizing yourself with them is beneficial.
Decoding Alarm Codes
Fanuc machines are known for their reliability and efficiency. Yet, they can occasionally present challenges. One common issue is alarm codes. Understanding these codes is crucial to maintaining smooth operations. In this section, we will decode these alarm codes to help you get back on track.
Types Of Alarm Codes
Fanuc alarm codes fall into several categories. Each category indicates a different type of issue:
- System Alarms: These relate to the core system functions.
- Servo Alarms: These pertain to the servo drive and motor.
- Spindle Alarms: These deal with the spindle motor and drive.
- Overheat Alarms: These indicate overheating issues.
- External Alarms: These come from external devices connected to the machine.
Steps To Identify Alarm Codes
Identifying Fanuc alarm codes involves a few straightforward steps:
- Check the Display: The alarm code will appear on the machine’s display.
- Consult the Manual: Refer to the machine’s manual for detailed information on the code.
- Use Online Resources: Many online resources can provide insights into specific codes.
- Document the Code: Keep a record of the alarm code for future reference.
- Contact Support: If needed, contact Fanuc support for further assistance.
By following these steps, you can quickly identify and address alarm codes, minimizing downtime and maintaining the efficiency of your Fanuc machine.
Resolving Servo Alarm Codes
Servo alarms can halt your CNC operations, causing downtime and reducing productivity. Understanding and resolving these alarms is crucial for maintaining smooth operations. This guide will help you decode and fix common Fanuc servo alarm codes efficiently.
Common Servo Alarms
Fanuc servo alarms often indicate issues with the motor, drive, or communication. Here are some typical codes you might encounter:
Alarm Code | Description |
---|---|
401 | Servo Alarm: VRDY off |
414 | Servo Alarm: X-axis detect error |
424 | Servo Alarm: Y-axis detect error |
434 | Servo Alarm: Z-axis detect error |
Quick Fixes For Servo Alarms
Before you call for professional help, try these quick fixes:
- Check connections: Ensure all cables are securely connected.
- Restart the machine: A simple reboot can sometimes resolve the issue.
- Inspect the servo drive: Look for any visible damage or loose parts.
- Reset the alarm: Follow the reset procedure in the Fanuc manual.
- Check parameter settings: Verify that all settings are correct.
These steps can often resolve common servo alarms, minimizing downtime and keeping your operations running smoothly.
Addressing Spindle Alarm Codes
Spindle alarms on Fanuc machines can disrupt your workflow. Understanding these codes helps you fix issues quickly. In this section, we’ll cover common spindle alarms. We’ll also provide effective solutions to these problems.
Frequent Spindle Alarms
Spindle alarms often occur due to various reasons. Overheating is a common cause. This happens when the spindle runs too fast or for too long. Power supply issues can also trigger alarms. A voltage drop or surge can affect spindle performance. Mechanical problems like worn-out bearings can lead to alarms. Regular maintenance is crucial to prevent these issues.
Effective Solutions For Spindle Issues
To solve spindle overheating, first, check your cooling system. Ensure it functions properly. Clean any debris blocking airflow. Adjust spindle speed to recommended levels. For power supply issues, inspect your electrical connections. Ensure there are no loose wires. Use a voltage regulator to stabilize power supply. If mechanical problems arise, inspect the spindle bearings. Replace any worn-out parts immediately. Regular lubrication of moving parts helps maintain spindle health.
Handling Overheat Alarms
Overheat alarms on Fanuc machines can disrupt operations and cause downtime. Understanding their causes and taking preventive measures can keep your equipment running smoothly. This section will guide you through the causes of overheat alarms and provide tips on how to prevent them.
Causes Of Overheat Alarms
Overheat alarms can be caused by several factors. Here are the most common reasons:
- Blocked air filters: Dust and debris can block air filters, reducing airflow.
- Faulty cooling fans: Cooling fans may stop working or run slower than needed.
- Dirty heat sinks: Heat sinks covered in dust cannot dissipate heat efficiently.
- High ambient temperature: Machines in hot environments are prone to overheating.
- Electrical issues: Problems with wiring or components can cause overheating.
Preventive Measures
To avoid overheat alarms, follow these preventive measures:
- Regular Maintenance: Clean air filters, heat sinks, and check fans regularly.
- Check Ambient Temperature: Ensure the machine operates in a cool environment.
- Inspect Electrical Components: Check wiring and connections for any issues.
- Use Cooling Systems: Employ additional cooling systems if necessary.
- Monitor Machine Load: Ensure the machine is not overloaded during operations.
Implementing these steps can help you prevent overheat alarms and maintain smooth operations.
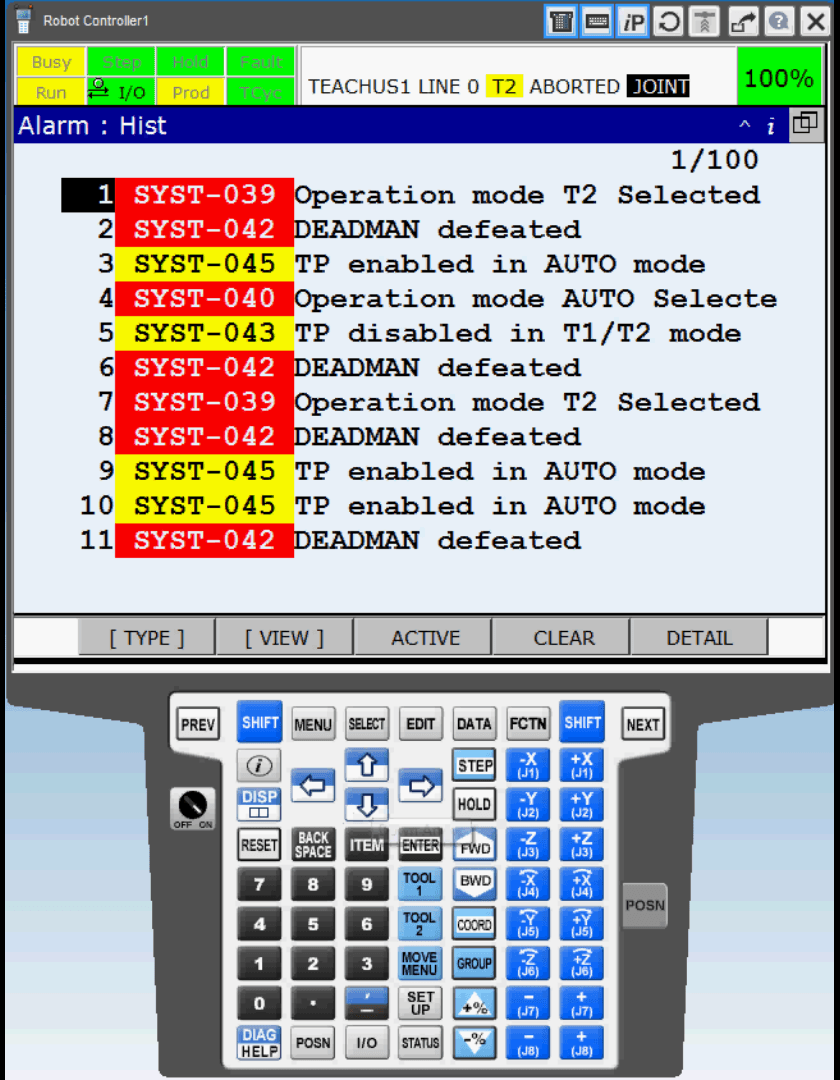
Credit: motioncontrolsrobotics.com
Troubleshooting Communication Errors
Communication errors in Fanuc systems can disrupt operations and cause delays. Troubleshooting these errors involves identifying the issue, fixing connection problems, and ensuring reliable communication. This section will help you understand and resolve communication errors efficiently.
Identifying Communication Errors
Identifying communication errors starts with recognizing the signs. Common indicators include:
- Error messages on the control panel
- Lost signals during operation
- Intermittent connectivity issues
Check the error codes displayed. These codes provide clues about the nature of the problem. Document the error codes for reference.
Fixing Connection Issues
Fixing connection issues often involves simple steps:
- Inspect cables for damage or loose connections.
- Ensure all cables are securely plugged in.
- Check for network configuration issues.
- Verify that all devices are on the same network.
If the problem persists, consider resetting the network settings to default. This can resolve many connectivity issues.
Step | Action |
---|---|
1 | Inspect and secure cables |
2 | Check network configuration |
3 | Reset network settings |
By following these steps, you can resolve most communication errors in Fanuc systems. Proper identification and fixing of connection issues are crucial for smooth operations.
Software And Firmware Issues
Software and firmware issues can disrupt the smooth operation of Fanuc systems. These problems often manifest through error codes and can be challenging to diagnose. Understanding these issues is crucial for maintaining optimal performance.
Updating Software
Outdated software can cause numerous problems in Fanuc systems. Regular updates help ensure compatibility and fix known bugs. Always check for software updates on the Fanuc website. Download and install the latest versions to keep your system running smoothly.
Dealing With Firmware Glitches
Firmware glitches can cause unexpected behavior in Fanuc systems. These issues might result in random error codes. Restarting the machine can sometimes resolve temporary glitches. If problems persist, consider reinstalling the firmware. Ensure you have the correct firmware version for your specific Fanuc model.
Preventive Maintenance Tips
Preventive maintenance can help you avoid unexpected downtimes and costly repairs. By taking care of your Fanuc system, you ensure smoother operations and extend its lifespan. Follow these preventive maintenance tips to keep your Fanuc system in top shape.
Routine Checks
Perform daily visual inspections to spot any unusual signs. Check for loose connections and worn-out parts. Listen for any strange noises. Ensure all indicators and displays are functioning correctly. Regularly clean the system to remove dust and debris. These simple checks can help you catch issues early.
Long-term Solutions
Schedule regular professional maintenance. This ensures a thorough inspection of all system components. Replace worn-out parts before they fail. Update software to the latest version. Keeping your system updated reduces the risk of software-related issues. Train your staff on proper use and care of the system. Well-trained staff can prevent many common issues.
When To Call For Professional Help
Encountering Fanuc troubleshooting codes can be confusing. It’s crucial to call for professional help when the error persists after basic troubleshooting attempts. Experts can efficiently diagnose and fix complex issues.
Troubleshooting Fanuc codes can be complex. Sometimes, you might need expert help. Knowing when to call a professional can save time. It also prevents potential damage to your machinery.Signs You Need Expert Assistance
Some signs suggest you need an expert. Frequent error codes are one sign. If you keep seeing the same error, it might need a professional touch. Another sign is unexpected shutdowns. These can indicate deeper issues. Inconsistent performance is another red flag. If your machine works one day and not the next, it’s time to call in help. Unusual noises or vibrations are also warning signs. These could mean mechanical problems. Finally, if you’ve tried basic fixes and the issue persists, don’t wait. Call an expert to prevent further damage.Choosing The Right Service Provider
Choosing the right service provider is important. Look for certified technicians. Certification ensures they know Fanuc systems. Experience is also key. Technicians with years of experience can often diagnose issues quicker. Check reviews and ask for references. Good reviews indicate reliable service. References can provide peace of mind. Also, ask about their availability. Quick response times are crucial. Downtime can cost money. Another tip is to ask about their warranty. A good warranty shows confidence in their work. It also protects you if issues arise later. “`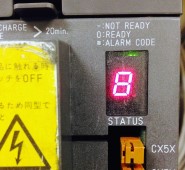
Credit: www.cncspares.com
Frequently Asked Questions
What Is Fanuc Error Code 9000?
Fanuc error code 9000 indicates a system alarm. It often means memory overload.
How To Fix Fanuc Error Code 300?
Check the servo motor connection. Ensure proper wiring and settings.
Why Does Fanuc Display Error Code 401?
Error code 401 typically means servo alarm. Check motor and amplifier.
What Causes Fanuc Error Code 410?
Error code 410 suggests an overtravel alarm. Verify limit switches.
How To Resolve Fanuc Error Code 501?
Error code 501 means a spindle alarm. Check spindle drive and parameters.
Conclusion
Understanding Fanuc troubleshooting codes can save you time and frustration. Use this guide to diagnose issues quickly. Stay proactive in maintaining your Fanuc systems. Regular checks and knowledge of codes help prevent downtime. Keep this reference handy for future troubleshooting.
Efficient operation depends on knowing these codes. Happy troubleshooting!