Ge Water Softener Troubleshooting: Quick Fixes and Tips
Experiencing issues with your GE water softener? You’re not alone.
Many homeowners face common problems with these appliances. Understanding how to troubleshoot your GE water softener can save you time and money. A water softener is crucial for maintaining soft water, which protects your plumbing and appliances. But like any household device, it can sometimes run into problems.
From salt bridges to error codes, knowing how to identify and fix these issues is essential. This guide will walk you through common troubleshooting steps, helping you restore your water softener’s efficiency. Whether you’re dealing with a minor glitch or a more significant problem, these tips will help you get your system back on track. Let’s dive in and solve those water softener issues together.
Common Issues
Experiencing problems with your GE water softener? You’re not alone. Many homeowners face common issues that can affect the performance of their water softeners. Understanding these problems can help you troubleshoot and maintain your system more effectively.
Low Water Pressure
One frequent issue is low water pressure. If your water softener is causing low water pressure, it can be frustrating. Here are some potential causes and solutions:
- Clogged Filter: Check if the filter is clogged. A clogged filter can reduce water flow. Clean or replace the filter to restore proper pressure.
- Blocked Resin Bed: The resin bed can sometimes become blocked. Perform a manual regeneration cycle to clean the resin bed.
- Bypass Valve: Ensure the bypass valve is fully open. A partially closed valve can restrict water flow.
Hard Water Spots
Another common problem is hard water spots. These can appear on dishes, glassware, and fixtures. If you notice hard water spots, your water softener may not be working correctly. Consider these potential issues:
- Salt Level: Check the salt level in the brine tank. Low salt levels can affect the softening process. Refill the tank with the appropriate type of salt.
- Resin Bed: Inspect the resin bed for any damage. A damaged resin bed can reduce the effectiveness of the water softener. Replace the resin if necessary.
- Brine Tank: Ensure the brine tank is functioning properly. Clean the tank to remove any buildup that could interfere with the brine solution.
Addressing these common issues can help maintain the efficiency of your GE water softener. Regular maintenance and timely troubleshooting can prolong the life of your system and ensure you have soft water for your home.

Credit: www.youtube.com
Diagnosing Problems
Experiencing issues with your GE water softener can be frustrating. Diagnosing the problems correctly is crucial. This section will help you pinpoint the issues and find solutions quickly. Let’s dive into checking salt levels and inspecting resin beads.
Checking Salt Levels
The salt level in your water softener is essential for proper operation. To check the salt level, follow these steps:
- Open the brine tank lid.
- Visually inspect the salt level inside the tank.
- If the salt is below the halfway mark, add more salt.
Make sure to use the correct type of salt. The three main types are rock salt, solar salt, and evaporated salt. Using the right salt ensures your water softener works efficiently.
Inspecting Resin Beads
Resin beads play a crucial role in the water-softening process. Inspecting them can help diagnose problems. Here are the steps:
- Turn off the water supply to the softener.
- Disconnect the unit from the electrical source.
- Remove the resin tank carefully.
- Check the condition of the resin beads inside the tank.
If the resin beads appear worn out or damaged, consider replacing them. Properly maintained resin beads ensure effective water softening.
Basic Maintenance
Regular maintenance of your GE water softener ensures its long life. Simple tasks keep your unit running smoothly. Let’s dive into basic maintenance steps.
Cleaning The Brine Tank
The brine tank stores salt for the water softening process. Salt can build up and form a crust. This can affect performance. Clean the brine tank every few months.
First, disconnect the unit from the power supply. Remove any remaining salt from the tank. Use warm water and mild detergent to scrub the interior. Rinse thoroughly to remove all soap residue. Refill the tank with new salt and reconnect the power.
Replacing Filters
Filters play a crucial role in water softening. They trap dirt and particles. Over time, filters get clogged. This reduces the efficiency of your unit.
Check the filters every month. Replace them if they appear dirty or worn out. Always follow the manufacturer’s instructions for replacing filters. Proper filter maintenance ensures clean and soft water.
Error Codes
Understanding error codes on your GE water softener can save you time and frustration. These codes help identify issues that need attention. Knowing what each code means is the first step to fixing the problem.
Interpreting Codes
GE water softeners display error codes to signal specific issues. Common codes include “Err01” for a motor problem and “Err03” for a valve issue. Refer to your user manual for a complete list. Each code corresponds to a specific malfunction. This helps you diagnose the problem faster.
Resetting The System
Sometimes, a simple reset can solve the issue. To reset your GE water softener, unplug it from the power source. Wait for a few minutes. Then, plug it back in. This can clear minor errors and restore normal operation. If the error persists, further troubleshooting may be needed.
Regeneration Cycle
The regeneration cycle is vital for the efficient operation of a GE water softener. This process helps to refresh the resin beads inside the softener, removing the minerals that cause water hardness. Understanding the regeneration cycle can help you troubleshoot and maintain your system better.
Manual Regeneration
Manual regeneration allows you to start the regeneration cycle at your convenience. This can be useful if you notice the water hardness level increasing before the scheduled cycle. To perform a manual regeneration, follow these steps:
- Find the control panel on your GE water softener.
- Press and hold the “Regenerate” button for about 5 seconds.
- Release the button when the regeneration cycle starts.
- Wait for the cycle to complete. It usually takes about 2 hours.
If the cycle does not start, check the power supply and ensure the system is properly connected.
Automatic Regeneration
Automatic regeneration is programmed to occur at specific intervals, typically based on water usage or time. This ensures consistent soft water supply. To ensure your system is set for automatic regeneration:
- Access the control panel.
- Navigate to the settings menu.
- Set the regeneration time and frequency according to your water usage.
Most GE water softeners have a default setting of every 7 days. If you experience hard water before the scheduled regeneration, adjust the frequency accordingly.
Understanding these methods can help maintain the efficiency of your GE water softener and ensure a consistent supply of soft water. Regular maintenance and proper settings are key to avoiding any issues with the regeneration cycle.
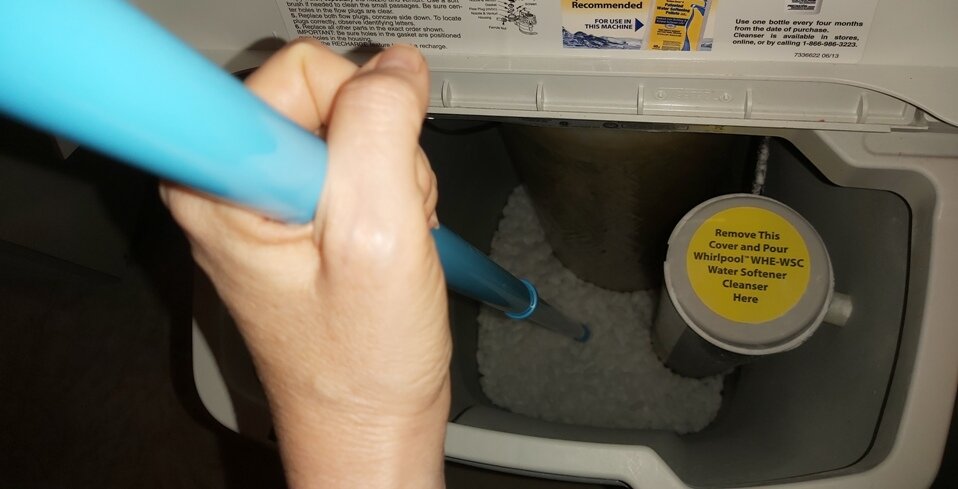
Credit: www.watersmartsystems.com
Water Leaks
Water leaks are a common issue with GE water softeners. Leaks can cause significant water waste and damage. It’s important to address them promptly to maintain system efficiency. This section will guide you on identifying and fixing leaks.
Identifying Leaks
First, check for visible signs of water around the unit. Look for puddles or damp areas. Inspect all connections and fittings for moisture. Use a flashlight if needed to see clearly.
If no visible signs are present, listen for a hissing or dripping sound. This may indicate a hidden leak. Check the water meter. A constant movement, even when no water is used, can signal a leak.
Fixing Common Leaks
Once you identify the source, you can start fixing it. Here are common leaks and how to fix them:
- Loose connections: Tighten any loose fittings with a wrench.
- Worn O-rings: Replace O-rings in connectors if they appear damaged.
- Cracked hoses: Replace any cracked or damaged hoses.
- Valve leaks: Check and replace faulty valves if needed.
For severe leaks or if you’re unsure, consider contacting a professional. Proper maintenance can prevent leaks and extend the life of your GE water softener.
Professional Help
Water softeners are essential for maintaining the quality of your water. Sometimes, they face issues that require professional help. Understanding when to call a technician and how to choose the right service can save you time and money. This section will guide you through these crucial steps.
When To Call A Technician
Knowing when to call a technician is key. Here are some signs to look out for:
- Unusual noises: If your water softener makes strange sounds.
- Low water pressure: A drop in water pressure could indicate a problem.
- Hard water signs: If you notice scale buildup on fixtures.
- Error codes: The unit displays error codes that you cannot resolve.
These issues often need expert attention. Don’t delay in seeking help. Prompt action can prevent further damage.
Choosing The Right Service
Picking the right service ensures your water softener is in good hands. Consider these factors:
- Experience: Choose a service with a proven track record.
- Certifications: Ensure technicians are certified and trained.
- Reviews: Check customer reviews and ratings online.
- Warranty: Services that offer warranties provide peace of mind.
These steps help you select a reliable service provider. Don’t compromise on quality. Your water softener’s efficiency depends on it.
Preventive Measures
Preventive measures are vital for the smooth operation of your GE water softener. Regular maintenance can save you from costly repairs. It also extends the lifespan of your unit. Let’s delve into some key preventive steps.
Regular Inspections
Check your water softener every month. Look for salt buildup in the brine tank. If present, clean it out. Inspect the unit for leaks. Ensure all connections are tight. Test the water softness. Adjust settings if needed. Regular inspections help catch small issues early.
Proper Usage Tips
Use the right type of salt. Check the user manual for recommendations. Don’t overfill the brine tank. Leave some space at the top. Keep the unit in a dry place. Moisture can cause damage. Avoid using hot water during regeneration. This can hurt the softener. Follow these tips for optimal performance.
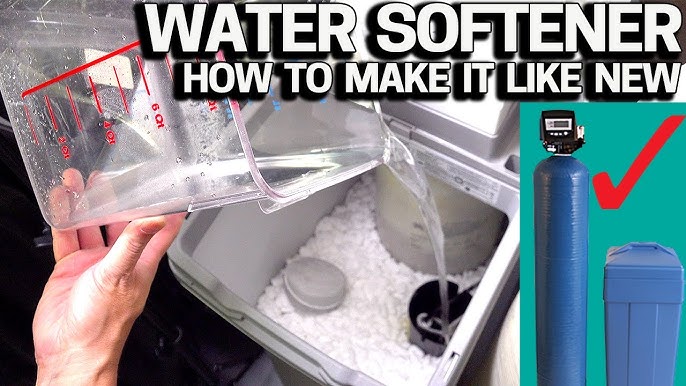
Credit: www.youtube.com
Frequently Asked Questions
Why Is My Ge Water Softener Not Regenerating?
A clogged injector or valve can stop regeneration. Clean them regularly. Check the settings too.
How Do I Reset My Ge Water Softener?
Press and hold the “RECHARGE” button for 3 seconds. The system will reset and start a recharge cycle.
What Does Error Code E1 Mean On My Ge Water Softener?
Error code E1 indicates a problem with the timer or circuit board. Inspect connections or call for service.
Why Is My Ge Water Softener Leaking?
Leaks may be due to loose connections or a worn-out seal. Tighten connections or replace seals if needed.
How Often Should I Add Salt To My Ge Water Softener?
Check the salt level monthly. Add salt when the level is below half. Use high-purity salt for best results.
Conclusion
Troubleshooting your GE water softener can seem daunting, but it’s manageable. Start with simple checks. Clean the brine tank regularly. Ensure the salt levels are adequate. Listen for unusual noises. Follow the manual closely. These steps can solve most issues.
For persistent problems, seek expert help. Regular maintenance ensures your system runs smoothly. Keep your water softener in top shape. Enjoy soft water every day.