Hamm Roller Troubleshooting: Expert Tips for Common Issues
Hamm rollers are essential in construction projects. They ensure smooth and even surfaces.
But what happens when they malfunction? Troubleshooting these machines can be challenging. Understanding common issues with Hamm rollers can save you time and money. Faulty rollers can disrupt your project schedule. Knowing how to identify and fix problems quickly is crucial.
This guide will help you diagnose and resolve common Hamm roller issues. From engine troubles to hydraulic failures, we cover it all. Equip yourself with the knowledge to keep your roller running smoothly. Keep reading to learn how to tackle these problems efficiently and get back to work faster.
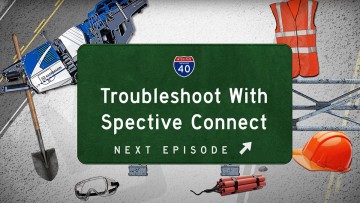
Credit: www.wirtgen-group.com
Engine Problems
The engine is the heart of your Hamm roller. Engine problems can halt your work. Understanding these issues can save time and money. Let’s dive into common engine problems and their solutions.
Starting Issues
Starting problems can be frustrating. Often, the battery is the culprit. Check the battery connections first. They should be clean and tight. A weak battery might need a charge or replacement. Another possible issue is the fuel. Ensure there is enough clean fuel in the tank. Dirty fuel can clog the system. Also, inspect the fuel filter. Replace it if necessary.
Overheating Solutions
Overheating can damage the engine. First, check the coolant level. Low coolant can cause overheating. Fill the coolant to the required level. Next, inspect the radiator. A blocked radiator can restrict airflow. Clean the radiator to ensure proper cooling. Also, check the fan belt. A loose or broken belt can lead to overheating. Replace it if needed. Lastly, monitor the engine oil. Low or old oil can cause the engine to overheat. Change the oil regularly to keep the engine cool.
Hydraulic System Failures
Hydraulic system failures in Hamm rollers can cause significant downtime. These failures affect the machine’s efficiency and performance. Understanding the common issues can help you troubleshoot effectively.
Slow Response
Slow response in the hydraulic system often indicates a problem. Check the hydraulic fluid level first. Low fluid can cause sluggish operations. Fill the reservoir to the recommended level.
Next, inspect the hydraulic filters. Dirty or clogged filters restrict fluid flow. Replace them if necessary. Also, examine the hydraulic pump. A faulty pump can reduce system pressure. Test the pump’s output and replace it if it’s underperforming.
Leakage Fixes
Hydraulic leaks are another common issue. Start by examining all hoses and connections. Look for visible signs of wear or damage. Tighten any loose connections. If a hose is damaged, replace it immediately.
Inspect the hydraulic seals. Worn or damaged seals can cause leaks. Replace the seals if you find any faults. Also, check the hydraulic cylinders. They should be free of dents or cracks. Repair or replace damaged cylinders to prevent leaks.
Vibration System Malfunctions
Vibration system malfunctions can affect the efficiency of your Hamm roller. These issues can lead to uneven compaction and increased maintenance costs. Understanding the causes and solutions can save you time and money.
Inconsistent Vibrations
Inconsistent vibrations are a common problem in Hamm rollers. This usually indicates an issue with the hydraulic system or the eccentric weights. Check for any hydraulic fluid leaks. Ensure that the hydraulic fluid level is adequate. Inspect the eccentric weights for wear or damage. Replace any faulty components immediately.
Calibration Tips
Calibration is crucial for maintaining consistent vibrations. Begin by ensuring the roller is on a flat surface. Start the machine and activate the vibration system. Use a calibration tool to measure the vibration frequency. Adjust the settings according to the manufacturer’s guidelines. Regular calibration ensures optimal performance and longevity.
Credit: www.wirtgen-group.com
Electrical System Troubles
Hamm rollers are essential in construction. But, they can sometimes face electrical system troubles. These issues can halt your work. Understanding the common problems helps in quick fixes. Two main areas to check are battery problems and wiring checks.
Battery Problems
The battery is the heart of the electrical system. If your roller won’t start, the battery might be the cause. Check the battery terminals for corrosion. Clean them with a wire brush. Ensure the battery connections are tight. A loose connection can prevent the roller from starting. Use a multimeter to check the battery voltage. A fully charged battery should read around 12.6 volts. If the voltage is low, recharge or replace the battery.
Wiring Checks
Wiring issues can also cause electrical problems. Inspect all wires for visible damage. Look for cuts, frays, or burns. Damaged wires need replacing. Check all connections for tightness. Loose wires can cause intermittent issues. Use a multimeter to check for continuity. This ensures the wires are good. Faulty wires can stop the roller from working. Replace any faulty wiring found during the check.
Drum Issues
Drum issues can significantly affect the performance of your Hamm roller. Identifying and fixing these problems early is essential for maintaining even compaction and ensuring smooth surfaces. Let’s dive into some common drum issues and their solutions.
Uneven Compaction
Uneven compaction can lead to poor road quality and increased maintenance costs. Here are some steps to identify and resolve this issue:
- Check the drum alignment. Ensure the drum is level with the ground.
- Inspect the drum for wear. Replace worn parts to maintain even compaction.
- Examine the vibration settings. Adjust them according to the material being compacted.
Regular maintenance and calibration can help prevent uneven compaction. Keep an eye on the drum’s condition to ensure optimal performance.
Surface Damage Repair
Surface damage on the drum can affect the quality of the compaction. Here are some common types of surface damage and their repair methods:
Type of Damage | Repair Method |
---|---|
Dents | Use a hammer to gently tap out the dents. |
Scratches | Sand the surface and apply a protective coating. |
Cracks | Weld the cracks and grind the surface smooth. |
Addressing surface damage promptly can extend the life of your Hamm roller. Regular inspections can help identify these issues before they become severe.
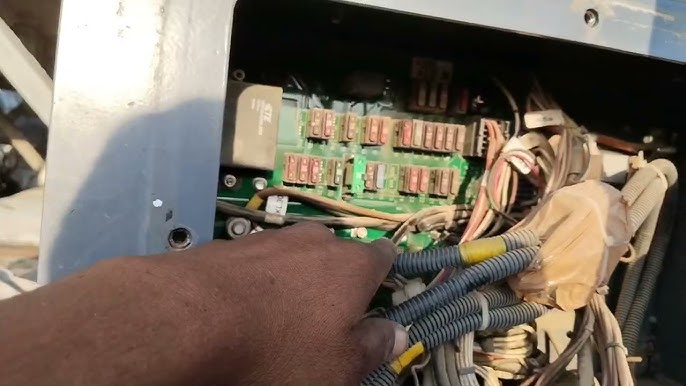
Credit: www.youtube.com
Maintenance Tips
Maintaining a Hamm roller is crucial for its longevity and performance. Regular maintenance keeps your equipment in top shape and prevents unexpected breakdowns. Below are some essential tips to ensure your Hamm roller remains efficient and reliable.
Regular Inspection Routines
Performing regular inspections can help identify potential issues before they become serious problems. Create a checklist to ensure nothing is overlooked during your routine inspections. Here are some key points to include:
- Check fluid levels (engine oil, hydraulic fluid, coolant)
- Inspect filters (air, fuel, hydraulic)
- Examine hoses and belts for signs of wear
- Look for leaks around the engine and hydraulic systems
- Ensure tire pressure is at the recommended level
Regular inspections can save you time and money in the long run. Address any issues found during these checks immediately to avoid costly repairs.
Preventive Measures
Taking preventive measures can extend the lifespan of your Hamm roller. Here are some practical steps to follow:
- Lubricate moving parts regularly to reduce wear and tear.
- Schedule routine oil changes to keep the engine running smoothly.
- Replace filters periodically to ensure clean fluids and air.
- Keep the roller clean to prevent dirt buildup and corrosion.
- Use quality parts and fluids to maintain optimal performance.
Implementing these preventive measures ensures your roller operates efficiently. It also minimizes the risk of unexpected breakdowns.
Task | Frequency |
---|---|
Fluid Level Check | Daily |
Filter Inspection | Weekly |
Hose and Belt Check | Monthly |
Oil Change | Every 100 hours |
Full System Inspection | Quarterly |
By following these maintenance tips, you can keep your Hamm roller in peak condition. Regular inspections and preventive measures are key to avoiding downtime and ensuring smooth operations.
Frequently Asked Questions
Why Is My Hamm Roller Not Starting?
Check the battery. Ensure it is charged and connected properly. Inspect the ignition switch and starter motor.
How To Fix Uneven Compaction With Hamm Roller?
Verify tire pressure. Ensure consistent speed. Check the drum and make sure it is clean and free from debris.
What Causes Excessive Vibration In Hamm Roller?
Loose components or misaligned drum. Inspect and tighten all parts. Check for worn or damaged bearings.
Why Is My Hamm Roller Leaking Oil?
Look for damaged seals or gaskets. Inspect the hydraulic system for leaks. Replace damaged parts immediately.
How To Maintain Hamm Roller For Long Life?
Regularly check fluid levels. Clean filters. Inspect and tighten all bolts. Schedule routine service with a professional.
Conclusion
Fixing Hamm Roller issues doesn’t have to be hard. With the right steps, you can save time and money. Regular checks help prevent major problems. Always follow the manual for guidance. If problems persist, call a professional. Your roller will work smoothly again.
Stay proactive and keep your equipment in top shape. Happy rolling!