Henny Penny Troubleshooting: Expert Tips to Fix Common Issues
Is your Henny Penny fryer giving you trouble? Don’t worry, you’re not alone.
Many users face common issues with their fryers. Understanding these problems can help you fix them quickly. Henny Penny fryers are known for their reliability and efficiency. But, like any other kitchen equipment, they can sometimes malfunction. This blog post will guide you through common troubleshooting steps.
You’ll learn how to identify and resolve issues to keep your fryer running smoothly. Whether it’s a heating problem or an error code, we’ve got you covered. Stay tuned to discover practical solutions and get your Henny Penny fryer back in top shape.
Introduction To Henny Penny Equipment
Welcome to our comprehensive guide on Henny Penny troubleshooting. Henny Penny equipment is renowned for its reliability and efficiency in commercial kitchens. Understanding the basics of this equipment can help ensure smooth operations and minimize downtime.
Overview Of Henny Penny Products
Henny Penny offers a wide range of products. These include fryers, rotisseries, and holding cabinets. Their fryers are known for even cooking and high efficiency. Rotisseries cook meat to perfection, retaining juices and flavor. Holding cabinets keep food at the ideal serving temperature.
Importance Of Regular Maintenance
Regular maintenance is crucial for Henny Penny equipment. It helps extend the lifespan of the machines. It also reduces the risk of unexpected breakdowns. Cleaning and inspecting equipment regularly can prevent many common issues. Ensure you follow the manufacturer’s maintenance schedule.
By doing so, you maintain the equipment’s peak performance. Regular checks can identify potential problems early. This proactive approach saves time and money in the long run.
Common Issues With Henny Penny Fryers
Henny Penny fryers are known for their reliability and efficiency. But like all equipment, they can face issues. Understanding common problems can help you maintain your fryer. Here are some frequent issues you might encounter with Henny Penny fryers.
Temperature Control Problems
Temperature control is crucial for consistent frying. A malfunction here can result in overcooked or undercooked food.
- Inconsistent Temperature: The fryer might not hold a steady temperature.
- Faulty Thermostat: A broken thermostat can give false readings.
- Heating Element Issues: The heating element may not heat properly.
These issues can be due to faulty wiring or worn-out parts. Regular checks can prevent most temperature control problems. Always ensure the thermostat is calibrated correctly.
Oil Filter Malfunctions
Oil filtering is essential for maintaining oil quality. Poor filtering can affect food taste and fryer performance.
- Clogged Filters: Filters can get clogged with food particles and debris.
- Pump Problems: The pump might not circulate oil properly.
- Leaks: Oil leaks can occur due to damaged seals or hoses.
A malfunctioning oil filter system can lead to dirty oil and poor cooking results. Regular cleaning and maintenance can help avoid these issues. Always check for blockages and ensure the pump works correctly.
Issue | Possible Cause | Solution |
---|---|---|
Inconsistent Temperature | Faulty thermostat | Replace or recalibrate thermostat |
Clogged Filters | Food particles | Clean or replace filters |
Leaks | Damaged seals | Replace seals |
Proper maintenance can extend the life of your fryer. Regular checks and cleaning are vital. Stay aware of these common issues to ensure your Henny Penny fryer works efficiently.
Resolving Issues With Henny Penny Ovens
Henny Penny ovens are known for their reliability. Yet, even the best equipment can face issues. This guide will help you troubleshoot common problems and keep your oven running smoothly. From uneven cooking to door seal problems, we cover it all to ensure your cooking process remains uninterrupted.
Uneven Cooking
Uneven cooking can ruin a dish. It is a common issue with many ovens, including Henny Penny. Here are some steps to resolve it:
- Check the oven racks. Ensure they are placed correctly.
- Verify the oven’s temperature with a thermometer.
- Inspect the heating elements for any signs of damage.
Use the following table to identify potential causes and solutions:
Cause | Solution |
---|---|
Incorrect Rack Placement | Adjust the rack position. |
Temperature Inaccuracy | Calibrate the oven temperature. |
Damaged Heating Elements | Replace the heating elements. |
Door Seal Problems
A faulty door seal can cause heat loss. This affects cooking efficiency. Follow these steps to check and fix door seal issues:
- Inspect the door seal for any cracks or tears.
- If damaged, order a replacement seal from the manufacturer.
- Clean the door seal regularly to maintain its elasticity.
Regular maintenance prevents future problems. A good door seal ensures even heat distribution, keeping your oven efficient.
Troubleshooting Henny Penny Warmers
Henny Penny warmers are essential in maintaining food temperature. When problems arise, quick troubleshooting is necessary to keep food quality high. Below, we address common issues and their solutions.
Inconsistent Heating
One frequent problem with Henny Penny warmers is inconsistent heating. This can lead to food not staying at the right temperature. Here are a few steps to troubleshoot this issue:
- Check the power supply. Ensure the warmer is plugged in properly.
- Inspect the thermostat settings. Adjust them as needed.
- Examine the heating elements. Replace if they appear damaged or worn out.
If the problem persists, the internal wiring may need inspection. In such cases, seeking professional help is advisable.
Display Errors
Display errors can disrupt the operation of Henny Penny warmers. These errors can be confusing and may indicate underlying issues. Follow these steps to troubleshoot display problems:
- Reset the warmer. Unplug for a few minutes, then plug it back in.
- Check for loose connections. Ensure all cables are securely attached.
- Review the user manual. Follow any specific instructions for error codes.
Persistent display errors might signal a need for software updates or professional maintenance.
By addressing these common issues, you can ensure your Henny Penny warmers function effectively. Keep your equipment in top shape to maintain food quality and customer satisfaction.
Dealing With Henny Penny Pressure Fryers
Henny Penny pressure fryers are vital in many commercial kitchens. But they can face issues. Quick troubleshooting can save you time and money. Below, we discuss common problems and solutions.
Pressure Seal Leaks
Pressure seal leaks are common in Henny Penny fryers. They can affect cooking and safety. Regular inspection helps prevent this issue.
- Check the seal for cracks or wear.
- Clean the seal and surrounding areas.
- Replace damaged seals immediately.
Always use genuine parts for replacements. This ensures a proper fit and function.
Pump Blockages
Pump blockages can reduce the efficiency of your fryer. Frequent cleaning is essential. Follow these steps to clear blockages:
- Turn off the fryer and let it cool.
- Remove the pump and inspect it.
- Clear any debris from the pump and hoses.
- Reassemble and test the fryer.
If blockages persist, the pump may need replacement. Consult the user manual for guidance.
Maintenance Tips For Longevity
Maintaining your Henny Penny equipment is essential for its longevity. Regular upkeep ensures your machines run smoothly and efficiently. Following a few simple maintenance tips can help you avoid costly repairs and downtime. Here are some key maintenance practices to keep your Henny Penny equipment in top shape.
Daily Cleaning Routines
Daily cleaning is critical for your Henny Penny equipment. Wipe down all surfaces with a damp cloth to remove grease and food particles. Clean the fryer baskets and other removable parts with warm, soapy water. Rinse thoroughly to avoid any soap residue. Ensure the oil filter system is clean to maintain optimal performance.
Check the oil level and top it up if necessary. Remove any debris from the oil to prevent contamination. Keeping your equipment clean daily helps prevent buildup and ensures safe operation.
Periodic Inspections
Conduct periodic inspections to identify potential issues early. Check for any signs of wear and tear on the equipment. Inspect the power cords and connections for any damage. Ensure all components are securely fastened and in good working order.
Examine the oil quality regularly. Replace it if it appears dark or has an off smell. Monitor the temperature settings to ensure they are accurate. Regular inspections help you catch problems before they become serious.
By following these maintenance tips, you can extend the life of your Henny Penny equipment. Consistent cleaning and inspections keep your machines running efficiently. Stay proactive and keep your equipment in peak condition.
When To Call A Professional
When dealing with Henny Penny equipment, some issues may require professional assistance. Knowing when to call a professional can save time and prevent further damage. This section covers identifying serious issues and choosing a qualified technician.
Identifying Serious Issues
Some problems with your Henny Penny equipment need immediate attention from a professional. Here are some serious issues to watch for:
- Electrical problems: Sparks, burning smells, or tripped breakers.
- Gas leaks: The smell of gas or hissing sounds near gas lines.
- Unusual noises: Loud banging, grinding, or other strange sounds.
- Temperature issues: Inconsistent heating or inability to reach the desired temperature.
- Persistent error codes: Repeated error messages that won’t clear.
If you notice any of these issues, shut down your equipment and call a professional immediately. Ignoring these signs can lead to costly repairs or dangerous situations.
Choosing A Qualified Technician
Finding the right technician ensures your Henny Penny equipment gets the best care. Consider these factors when choosing a technician:
- Experience: Look for technicians with experience in Henny Penny equipment.
- Certifications: Ensure they have the necessary certifications and training.
- Reviews: Check online reviews and ask for references.
- Availability: Find a technician who can respond quickly to emergencies.
- Warranty: Confirm they offer a warranty on their work.
By choosing a qualified technician, you ensure your equipment remains in top condition, reducing downtime and improving performance.
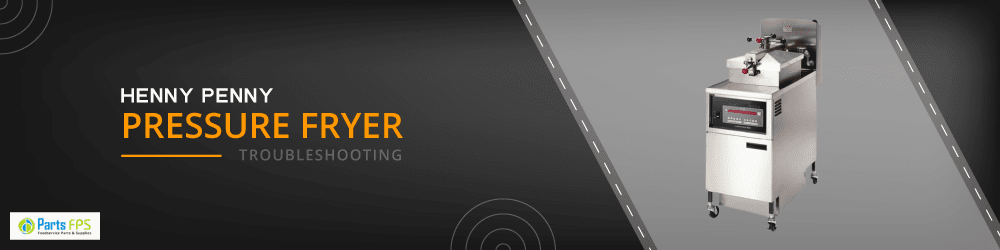
Credit: www.partsfps.com
Preventative Measures For Henny Penny Equipment
Proper maintenance ensures the longevity of Henny Penny equipment. Preventative measures reduce downtime and costly repairs. Regular check-ups and following usage guidelines are essential.
Proper Usage Guidelines
Using Henny Penny equipment correctly is crucial for its durability. Follow these simple guidelines:
- Read the user manual thoroughly before operation.
- Ensure the equipment is on a stable and level surface.
- Do not overload the machine; adhere to capacity limits.
- Use only recommended materials and ingredients.
- Turn off and unplug the equipment after use.
These steps ensure safe and efficient operation. They also prevent unexpected breakdowns.
Scheduled Maintenance Plans
Regular maintenance is vital for keeping Henny Penny equipment in top condition. Create a schedule to check and service the equipment. Here are some key maintenance tasks:
Task | Frequency |
---|---|
Clean filters | Weekly |
Inspect electrical connections | Monthly |
Lubricate moving parts | Quarterly |
Replace worn-out parts | As needed |
By following a maintenance plan, you can avoid unexpected issues. It helps in ensuring the equipment runs smoothly. This way, your operations remain uninterrupted and efficient.
Conclusion And Final Thoughts
In this section, we will review the key points of Henny Penny troubleshooting. We will also discuss the importance of proactive care for your equipment. Regular maintenance can help in preventing many common issues.
Summary Of Key Points
Here is a summary of the key points discussed in this blog:
- Check Power Supply: Ensure the equipment is properly plugged in and the circuit breakers are not tripped.
- Temperature Control: Verify that the temperature settings are correct and functioning. Misconfiguration can affect cooking results.
- Cleanliness: Regular cleaning prevents build-up, which can cause malfunctions. Pay attention to the fryer’s oil and filters.
- Error Codes: Consult the manual for understanding error codes. Address the issues as per the instructions.
- Regular Maintenance: Schedule routine maintenance to keep the equipment running smoothly. Replace worn parts promptly.
Encouraging Proactive Care
Proactive care of Henny Penny equipment can save time and money. Here are some tips to encourage proactive care:
- Regular Inspections: Conduct regular inspections to spot potential issues early.
- Staff Training: Train your staff on proper usage and maintenance routines. Well-trained staff can identify problems before they escalate.
- Documentation: Keep detailed records of maintenance activities. This helps in tracking the performance and scheduling future maintenance.
- Follow Manufacturer’s Guidelines: Always adhere to the manufacturer’s guidelines for maintenance and troubleshooting.
By following these tips, you can extend the life of your Henny Penny equipment. Proper care ensures consistent performance and reduces downtime.
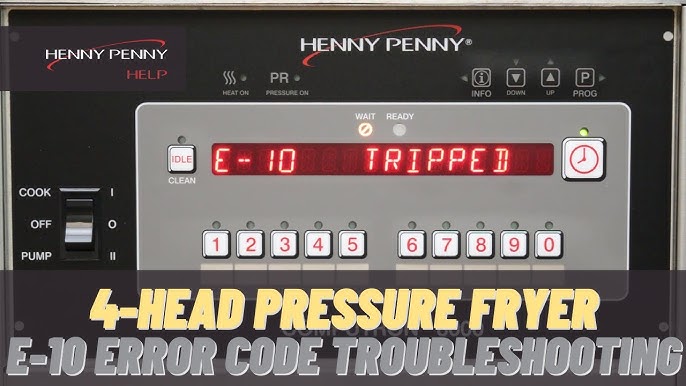
Credit: www.youtube.com
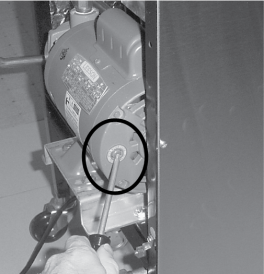
Credit: operation.hennypennyhelp.com
Frequently Asked Questions
Why Is My Henny Penny Fryer Not Heating Up?
Check the power supply and the thermostat settings. Also, inspect the heating elements for any damage.
How Do I Reset A Henny Penny Fryer?
Turn off the fryer and unplug it. Wait for a few minutes, then plug it back in and turn it on.
What Causes My Henny Penny Fryer To Overheat?
Overheating can be due to a faulty thermostat or clogged ventilation. Ensure proper airflow and check the thermostat.
Why Is My Henny Penny Fryer Leaking Oil?
Inspect the oil tank for cracks or loose connections. Ensure all seals and gaskets are intact and properly fitted.
How Do I Clean A Henny Penny Fryer Filter?
Remove the filter and soak it in hot, soapy water. Scrub gently and rinse thoroughly before reinstalling.
Conclusion
Troubleshooting Henny Penny equipment can be simple with the right steps. Always check for common issues first. Clean and maintain regularly to prevent problems. Refer to the manual for guidance. Seek professional help if problems persist. Proper care ensures efficient operation.
Happy cooking!