Hydro Gear Troubleshooting: Expert Tips to Diagnose and Fix Issues
Hydro Gear systems are vital for efficient lawn and garden care. They power many of the top lawnmowers and other machines.
Yet, like any mechanical system, they can have issues. Understanding Hydro Gear troubleshooting can save you time and money. Knowing the basics helps you spot and fix problems quickly. Common issues include leaks, strange noises, and performance drops. By identifying these early, you can avoid bigger repairs.
This guide will walk you through simple steps to diagnose and resolve typical Hydro Gear problems. Whether you’re a homeowner or a professional, these tips can keep your equipment running smoothly. Dive in to learn how to maintain your Hydro Gear system efficiently.
Common Hydro Gear Problems
Hydro Gear systems are essential in various machinery, offering smooth and efficient operations. Despite their efficiency, users often encounter issues. Understanding these common Hydro Gear problems can save time and money.
Noisy Operation
Noisy operation in Hydro Gear systems is a frequent issue. This noise often results from worn-out bearings or misaligned gears. Regular maintenance can prevent these problems.
Here are some steps to address noisy operation:
- Check for loose or damaged parts.
- Inspect bearings and replace if necessary.
- Ensure gears are properly aligned.
- Lubricate moving parts regularly.
If noise persists, consider seeking professional assistance. Persistent noise can indicate more severe internal damage.
Fluid Leaks
Fluid leaks are another common Hydro Gear problem. Leaks can lead to reduced efficiency and potential system failure. Identifying the source of the leak is crucial.
Common causes of fluid leaks include:
- Worn or damaged seals.
- Loose fittings or connections.
- Cracks in the housing.
To fix fluid leaks, follow these steps:
- Inspect all seals and replace if necessary.
- Tighten all fittings and connections.
- Check the housing for cracks and repair or replace as needed.
Regular inspection and maintenance can help prevent fluid leaks. Always use the recommended fluid type for your Hydro Gear system.
Initial Inspection Steps
Hydro Gear systems are vital components in many machines. Regular maintenance helps keep them working efficiently. The first step in troubleshooting is a thorough initial inspection. This process involves several key steps to identify potential issues quickly.
Visual Inspection
Begin with a visual inspection. Look for obvious signs of wear or damage. Check for leaks around seals and hoses. Pay attention to any loose or missing parts. Look closely at the drive belt for cracks or fraying.
Use a flashlight to inspect hard-to-see areas. Look for any buildup of dirt or debris. Clean these areas if necessary. This can help reveal hidden issues.
Fluid Level Check
Next, perform a fluid level check. Low fluid levels can cause performance issues. Check the fluid reservoir for the proper level. Refer to the machine’s manual for the correct specifications.
Use a clean dipstick to measure the fluid. Ensure it is within the recommended range. If the fluid is low, top it up with the appropriate type. Check for any signs of contamination or discoloration.
If you notice any issues, it may be time for a fluid change. Regular fluid maintenance is crucial for the longevity of your Hydro Gear system.
Identifying Noisy Operation Causes
Experiencing noisy operation in your Hydro Gear system can be frustrating. Understanding the root causes can help you address the issue effectively. Below, we will explore some common causes of noisy operation.
Worn Bearings
Worn bearings often lead to unusual noises in Hydro Gear systems. Bearings are crucial for smooth operation. When bearings wear out, they cause friction. This friction creates noise. Check for signs of wear and tear.
Common signs include:
- Grinding sounds
- Excessive vibration
- Overheating components
Regular inspection can help you catch worn bearings early. Replacing them as needed ensures quieter operation and extends system life.
Air In System
Air trapped in the hydraulic system can also cause noise. This air disrupts the fluid flow. It leads to cavitation. Cavitation produces a loud, banging noise. It can damage components if left unchecked.
To remove air:
- Check for loose connections.
- Tighten any loose fittings.
- Bleed the system to release trapped air.
Preventing air from entering the system is key. Regular maintenance helps keep the system air-free and quiet.
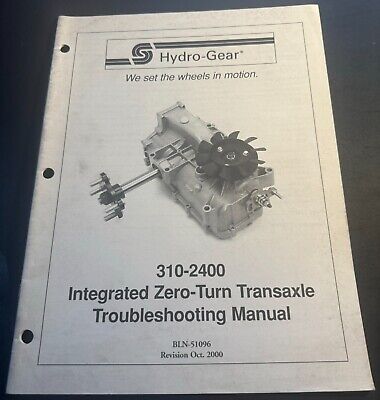
Credit: www.ebay.com
Addressing Fluid Leaks
Fluid leaks can cause serious issues in your Hydro Gear system. These leaks reduce efficiency and may lead to system failure. Addressing fluid leaks promptly ensures your equipment runs smoothly. Here, we’ll cover common causes of fluid leaks and how to fix them.
Seal Replacement
Worn-out seals often cause fluid leaks. Over time, seals can crack or wear down. Replacing these seals is essential for stopping leaks. First, identify the leaking seal. Then, remove the old seal carefully. Install a new, compatible seal in its place. Make sure the new seal fits tightly. This should stop the leak and restore proper function.
Loose Fittings
Loose fittings are another common cause of fluid leaks. Check all fittings for tightness. Use a wrench to tighten any loose connections. Ensure not to overtighten, which can cause damage. Sometimes, fittings may need replacement. If so, choose the correct size and type. Properly tightened fittings can prevent future leaks.
Performance Issues
Hydro Gear systems are known for their reliability. But performance issues can occur. Recognizing these issues early can prevent major problems. Here are some common performance issues you might face. This guide will help you understand and troubleshoot them.
Sluggish Movement
Sluggish movement is a common issue. Your machine may not move as quickly as it should. This could be due to low hydraulic fluid. Check the fluid level first. Refill if necessary. Another cause might be air trapped in the system. Bleed the system to remove any air bubbles.
Dirty or clogged filters can also slow down movement. Inspect and clean the filters. Replace them if needed. Worn-out parts can also cause sluggishness. Inspect gears, pumps, and motors for wear. Replace any worn parts to restore performance.
Power Loss
Power loss can affect productivity. Check the hydraulic fluid level. Low fluid levels can cause power loss. Refill the fluid if it is low. Also, inspect for any leaks. Leaks can reduce fluid levels quickly. Fix any leaks you find.
Another cause of power loss is worn-out belts. Check the belts for wear and tear. Replace any damaged belts. Clogged filters can also lead to power loss. Clean or replace filters regularly. Lastly, ensure the engine is running properly. Poor engine performance can affect the Hydro Gear system.
Hydro Gear Maintenance Tips
Maintaining your Hydro Gear system is essential for optimal performance and longevity. Regular upkeep can prevent costly repairs and downtime. Here are some practical Hydro Gear maintenance tips to keep your system running smoothly.
Regular Fluid Changes
Hydro Gear systems rely heavily on hydraulic fluid. Changing the fluid regularly is crucial. Old fluid can cause wear and tear on components. Check the fluid levels frequently. Use the recommended type of hydraulic fluid. Follow the manufacturer’s guidelines for fluid changes. It ensures the system runs efficiently.
Component Lubrication
Lubrication of moving parts is vital for smooth operation. Ensure all components are well-lubricated. This reduces friction and prevents damage. Use high-quality lubricants for best results. Regularly inspect parts for signs of wear. Replace or lubricate as needed. Proper lubrication extends the life of your Hydro Gear system.
Tools For Troubleshooting
For effective Hydro Gear troubleshooting, having the right tools is essential. Proper tools ensure accurate diagnosis and efficient repairs. This section highlights the key tools needed for troubleshooting Hydro Gear issues. From diagnostic equipment to basic repair tools, each plays a crucial role in maintaining your equipment.
Diagnostic Equipment
Diagnostic equipment helps identify issues precisely. A multimeter is essential for checking electrical connections. It measures voltage, current, and resistance. Pressure gauges are vital too. They check hydraulic pressure within the system. An OBD-II scanner is useful for reading error codes. It connects to the vehicle’s diagnostic port. These tools help pinpoint problems quickly and accurately.
Basic Repair Tools
Basic repair tools are necessary for hands-on fixes. A set of wrenches is a must-have. They come in various sizes for different bolts. Screwdrivers are essential as well. Both flat-head and Phillips are needed. Pliers are useful for gripping and twisting. A rubber mallet helps in applying force without damaging parts. Socket sets are versatile for many repair tasks.
Having these tools ready makes troubleshooting easier. They ensure you can fix issues promptly. This minimizes downtime and keeps your equipment running smoothly.

Credit: www.youtube.com
When To Seek Professional Help
For Hydro Gear troubleshooting, seek professional help if unusual noises, leaks, or performance issues occur. This ensures proper diagnosis and repair.
Experiencing issues with your Hydro Gear system can be frustrating. Some problems are easy to fix on your own. Yet, there are times when you need a professional. Knowing when to seek help can save time and prevent further damage.Complex Repairs
Some repairs are beyond basic tools and skills. If the problem involves internal parts, it is best to contact a professional. They have the right tools and expertise. Attempting complex repairs without proper knowledge can worsen the issue. Professionals ensure the repair is done correctly and safely.Persistent Issues
Sometimes, the same problem keeps coming back. You fix it, but it returns. Persistent issues can be a sign of a deeper problem. A professional can diagnose the root cause. They provide a lasting solution. This prevents recurring issues and extends the life of your equipment. “`
Credit: www.youtube.com
Frequently Asked Questions
What Causes Hydro Gear Transmission Problems?
Hydro Gear transmission problems often stem from low oil levels, dirty filters, or air in the system.
How Do You Check Hydro Gear Fluid Levels?
Check fluid levels by removing the reservoir cap. Ensure the oil reaches the “Full” mark.
Why Is My Hydro Gear Noisy?
Noise in Hydro Gear systems is usually due to air in the fluid, worn parts, or low oil.
How Can I Fix Hydro Gear Leaks?
Fix leaks by tightening connections, replacing seals, or checking for cracks in the hydraulic lines.
What Maintenance Does Hydro Gear Require?
Regular maintenance includes checking oil levels, changing filters, and inspecting for leaks or worn parts.
Conclusion
Troubleshooting Hydro Gear issues can be simple with the right steps. Identify the problem early to save time and money. Regular maintenance helps prevent common issues. Always use proper tools and follow guidelines. Consult the manual for specific instructions. Seek professional help if needed.
Keep your equipment in top shape for better performance. Stay informed and proactive to avoid major problems. Happy troubleshooting!