Hydrostatic Transmission Troubleshooting: Expert Tips and Solutions
Hydrostatic transmission systems are common in many machines. They rely on fluid to transmit power.
Understanding how to troubleshoot these systems can save time and money. Hydrostatic transmissions are vital in lawn mowers, tractors, and other heavy equipment. They offer smooth and precise control. But like all machinery, they can develop issues. Knowing how to troubleshoot these problems is crucial for maintaining performance.
This guide will help you identify and fix common hydrostatic transmission problems. By learning these tips, you can ensure your equipment runs efficiently. Let’s dive into the basics of hydrostatic transmission troubleshooting to keep your machines in top shape.
Introduction To Hydrostatic Transmission
Hydrostatic transmission systems are vital in various machinery. They offer seamless power transfer. Understanding these systems can help in troubleshooting issues. This section covers the basic principles and common applications of hydrostatic transmission.
Basic Principles
Hydrostatic transmission systems use fluid pressure to transfer power. This method is highly efficient and flexible. Here are the key components:
- Pumps: These create fluid flow.
- Motors: They convert fluid flow back into mechanical power.
- Reservoir: This stores the hydraulic fluid.
- Valves: They control the fluid flow and pressure.
The main principle involves converting mechanical energy into fluid energy. Then, it converts back to mechanical energy. This results in smooth and controlled power transfer. These systems are closed-loop, meaning the fluid circulates within a confined system.
Common Applications
Hydrostatic transmissions are found in many industries. They are especially popular in heavy machinery. Here are some common applications:
- Agricultural equipment: Tractors and combines use hydrostatic systems for variable speed control.
- Construction machinery: Excavators and loaders benefit from the precision and power of hydrostatic systems.
- Industrial machines: Conveyor belts and presses use these systems for consistent performance.
- Marine vessels: Boats and ships use hydrostatic transmissions for steering and propulsion.
These applications highlight the versatility and efficiency of hydrostatic transmissions. They offer smooth, variable speed control. This makes them ideal for tasks requiring precise movements.
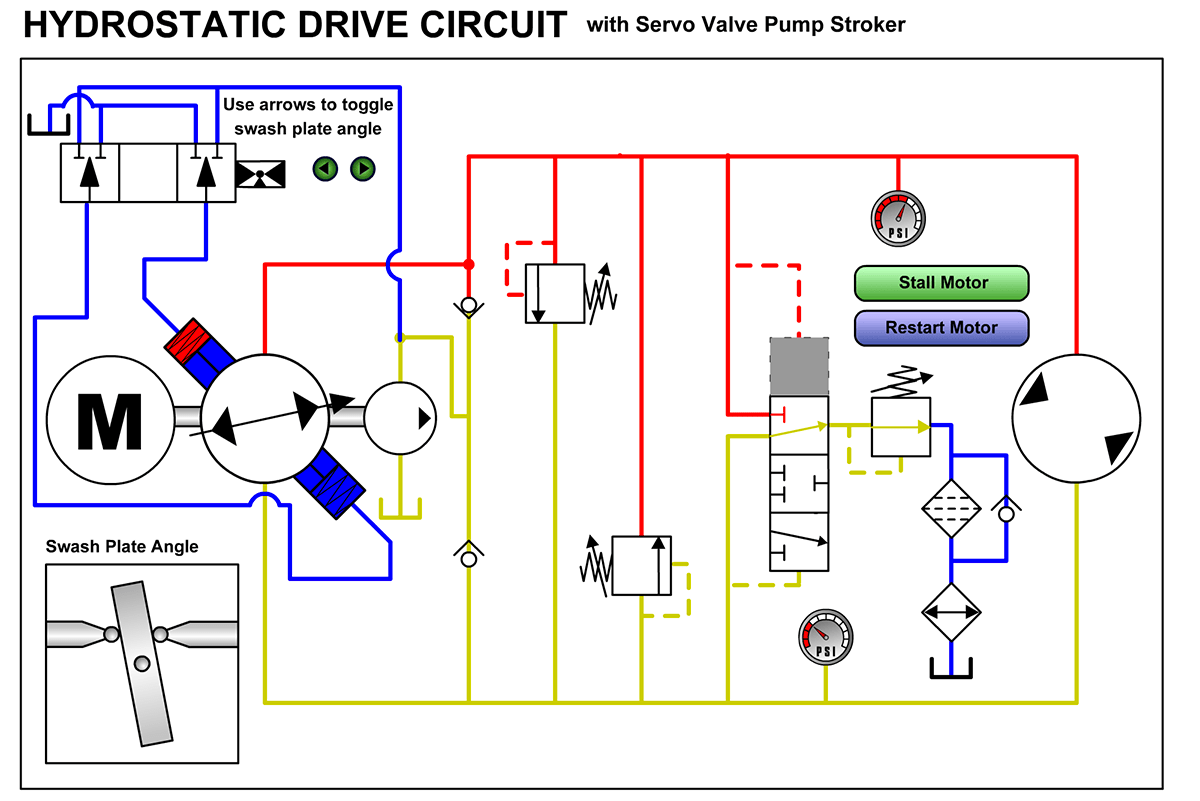
Credit: www.cdiginc.com
Identifying Symptoms Of Problems
Hydrostatic transmissions offer smooth and efficient power transfer. But, like any machinery, they can develop issues over time. Identifying symptoms early can prevent costly repairs. Knowing what to look for helps maintain performance and longevity. This section will cover the most common signs of problems.
Unusual Noises
One of the first signs of trouble is unusual noises. Hydrostatic transmissions should operate quietly. If you hear grinding, whining, or clunking, something is wrong. These noises often indicate internal wear or damage. It could be low fluid levels or contamination. Always listen for changes in sound during operation. Regular maintenance can prevent these issues.
Performance Issues
Performance issues are another red flag. If your machine is sluggish, the transmission might be failing. Noticeable drops in speed or power can signal problems. Inconsistent movement is another symptom. Sometimes, the machine may jerk or lurch unexpectedly. These issues often result from worn components or fluid issues. Check for leaks and ensure fluid levels are adequate.
Common Causes Of Failures
Low hydraulic fluid levels can cause hydrostatic transmission failures. Contaminated fluid and worn-out components also contribute to common issues. Proper maintenance helps prevent these problems.
Hydrostatic transmission systems are reliable and efficient. But they can face issues. Knowing the common causes of failures helps in timely troubleshooting.Fluid Contamination
Fluid contamination is a leading cause of transmission failures. Dirt and debris can enter the system. This often happens during maintenance or fluid changes. Contaminated fluid can damage internal components. Always use clean, high-quality hydraulic fluid. Regularly check and replace filters. Preventing contamination can save time and money.Component Wear
Components wear down over time. Seals, bearings, and gears are especially prone to wear. Regular inspections can detect early signs of wear. Worn components can cause leaks and reduced efficiency. Replacing worn parts promptly prevents bigger issues. Keep a maintenance schedule to track component lifespan. This ensures your system runs smoothly and efficiently. “`Credit: www.linkedin.com
Fluid And Filter Maintenance
Maintaining the fluid and filters in your hydrostatic transmission system is crucial. Proper care ensures optimal performance and longevity. Let’s delve into the importance of fluid and filter maintenance.
Choosing The Right Fluid
Using the correct fluid is vital for your hydrostatic transmission. Different systems need specific fluids. Always check the manufacturer’s guidelines.
A good hydrostatic fluid:
- Provides proper viscosity
- Has anti-wear properties
- Prevents corrosion
- Offers thermal stability
Tip: Avoid mixing different fluids. It can affect system performance.
Regular Filter Replacement
Filters keep the fluid clean by trapping dirt and debris. Over time, they get clogged. Regular replacement is necessary.
Benefits of regular filter replacement:
- Improves system efficiency
- Prevents contamination
- Extends component life
Replace filters according to the maintenance schedule. Check the manual for specific intervals.
Here’s a simple guide for filter replacement:
- Turn off the engine
- Locate the filter
- Remove the old filter
- Install the new filter
- Check for leaks
Regular maintenance of fluid and filters keeps your hydrostatic transmission running smoothly.
Inspecting And Testing Components
Inspecting and testing components is essential for effective hydrostatic transmission troubleshooting. These steps ensure the system operates smoothly. Proper inspections can identify potential issues early. Testing helps confirm the condition of each component. This section will guide you through visual inspections and pressure testing.
Visual Inspections
Begin with a thorough visual inspection. Look for obvious signs of wear or damage. Check hoses for leaks or cracks. Examine connections to ensure they are secure. Inspect the transmission fluid for contamination or discoloration. Clear fluid indicates a healthy system. Cloudy or dark fluid suggests issues. Also, check filters for debris. Clean or replace them if necessary.
Pressure Testing
Pressure testing is crucial for diagnosing hydrostatic transmission problems. Use a pressure gauge to measure system pressure. Connect the gauge to the test port on the transmission. Start the machine and record the pressure readings. Compare them to the manufacturer’s specifications. Low pressure may indicate a pump issue. High pressure can point to blockages or restrictions. Regular pressure testing helps maintain optimal performance.
Fixing Common Issues
Experiencing issues with your hydrostatic transmission can be frustrating. Fixing these problems can save time and money. This section will help you identify and solve common issues with ease.
Adjusting Control Settings
Incorrect control settings can cause transmission problems. Adjusting these settings can enhance performance. Follow these steps:
- Locate the control lever. This is usually near the driver’s seat.
- Check for any loose connections. Tighten any that are loose.
- Adjust the lever to the manufacturer’s recommended position.
- Test the machine. Make sure it operates smoothly.
Remember: Always refer to your machine’s manual for specific instructions. Proper adjustment can prevent further issues.
Replacing Worn Parts
Worn parts can lead to transmission failure. Replacing these parts is essential for maintaining efficiency. Here’s a simple guide:
- Identify the worn parts: Inspect the machine for any signs of wear and tear.
- Obtain the correct replacements: Make sure to get parts that match your machine’s specifications.
- Replace the parts: Follow the steps in your manual for replacing each part.
- Test the machine: Ensure that the new parts are functioning properly.
Using high-quality parts can extend the life of your machine. Regular maintenance can prevent the need for frequent replacements.
Common Issues | Possible Solutions |
---|---|
Sluggish Performance | Check and adjust control settings |
Unusual Noises | Inspect and replace worn parts |
Overheating | Ensure proper ventilation and check fluid levels |
By addressing these common issues, you can keep your hydrostatic transmission running smoothly. Regular checks and timely repairs can save you from costly downtime.
Preventive Measures
Hydrostatic transmission systems require regular care to function efficiently. By taking preventive measures, you can minimize breakdowns and extend the life of your equipment. Below are some key areas to focus on.
Scheduled Maintenance
Regular scheduled maintenance is crucial for hydrostatic transmission systems. Create a maintenance plan that includes:
- Changing the hydraulic fluid at the recommended intervals.
- Checking and replacing filters regularly.
- Inspecting hoses and seals for leaks or wear.
- Testing the system pressure to ensure it remains within the specified range.
By following a consistent maintenance schedule, you can catch small issues before they become major problems.
Proper Usage Techniques
Using the equipment correctly can prevent many issues. Here are some proper usage techniques to keep in mind:
- Avoid overloading the system beyond its capacity.
- Operate controls smoothly to prevent sudden pressure spikes.
- Ensure the equipment is always on a stable surface.
- Allow the system to warm up before use, especially in cold conditions.
Proper usage extends the life of your hydrostatic transmission system and reduces the need for repairs.

Credit: www.machinerylubrication.com
When To Seek Professional Help
Hydrostatic transmissions are complex systems. Sometimes, issues arise that need expert attention. Knowing when to seek professional help can save time and money. This section will guide you through the signs of severe damage and how to find a qualified technician.
Signs Of Severe Damage
Recognizing the signs of severe damage is crucial. It can prevent further harm to your hydrostatic transmission. Look out for these symptoms:
- Unusual noises: Loud grinding or whining sounds indicate internal damage.
- Fluid leaks: Puddles under the transmission show possible seal or gasket failure.
- Overheating: If the transmission is too hot to touch, it may have a serious issue.
- Loss of power: If the machine struggles to move, the transmission might be failing.
Finding A Qualified Technician
Once you identify severe damage, finding a qualified technician is the next step. Here are some tips to help you:
- Ask for recommendations: Friends, family, and online reviews can point you to reliable professionals.
- Check certifications: Ensure the technician has proper certification for hydrostatic transmission repair.
- Experience matters: Choose someone with years of experience in hydrostatic systems.
- Inquire about warranties: A good technician should offer a warranty on their work.
By following these steps, you can find a trustworthy expert to fix your hydrostatic transmission, ensuring your equipment runs smoothly again.
Frequently Asked Questions
What Are Common Symptoms Of Hydrostatic Transmission Problems?
Symptoms include loss of power, slow response, unusual noises, and overheating.
How Do You Check Hydrostatic Transmission Fluid Levels?
Locate the reservoir. Check the fluid level against the marked indicator.
Why Is My Hydrostatic Transmission Making Noise?
Noise may indicate low fluid levels, air in the system, or worn components.
How Often Should Hydrostatic Transmission Fluid Be Changed?
Check the manufacturer’s manual. Typically, change the fluid every 200-500 hours of use.
What Causes Hydrostatic Transmission To Lose Power?
Possible causes include low fluid levels, clogged filters, or worn-out components.
Conclusion
Troubleshooting hydrostatic transmission can seem difficult, but it is manageable. Regular maintenance prevents many issues. Listen to your machine. Check for leaks and unusual noises. Consult your manual often. Replace worn parts promptly. Keep the system clean. Small problems can become big if ignored.
Always prioritize safety. Follow these steps and keep your machine running smoothly. Happy troubleshooting!