Intertherm Furnace Troubleshooting: Expert Tips & Solutions
To troubleshoot an Intertherm furnace, start by checking the thermostat settings and ensuring the power supply is on. Inspect and clean the air filters regularly.
Intertherm furnaces are reliable, but occasional issues can arise. Effective troubleshooting can save time and money. Begin by examining the thermostat to confirm it is set correctly and has power. Verify that the circuit breaker is not tripped and the furnace switch is on.
Regularly cleaning or replacing air filters is essential to maintain efficiency. Check for any error codes displayed on the furnace and consult the manual for guidance. If problems persist, it might be necessary to call a professional technician for a thorough inspection and repair. Proper maintenance ensures your furnace runs smoothly and efficiently.
Common Furnace Issues
Intertherm furnaces are reliable, but sometimes, they face problems. Knowing the common issues helps in quick fixes. Below, we discuss some frequent problems and how to troubleshoot them.
No Heat
If your furnace isn’t producing heat, check the thermostat. Ensure it’s set to “heat” mode and the temperature is correct. Next, examine the circuit breaker. If it’s tripped, reset it. Sometimes, the pilot light might be out. Relight it according to the manufacturer’s instructions.
- Check thermostat settings
- Reset circuit breaker
- Relight pilot light
Also, inspect the filter. A dirty filter restricts airflow, causing no heat. Replace it if needed.
Component | Solution |
---|---|
Thermostat | Set to “heat” and correct temperature |
Circuit Breaker | Reset if tripped |
Pilot Light | Relight if out |
Filter | Replace if dirty |
Inconsistent Temperature
Inconsistent temperature might be due to a faulty thermostat. Check if the thermostat is level and clean. Dust can affect its performance. Next, inspect the furnace blower. If the blower is dirty, it can’t distribute heat evenly.
- Check if thermostat is level
- Clean the thermostat
- Inspect and clean furnace blower
Also, look at your home’s insulation. Poor insulation can cause uneven heating. Seal any gaps or leaks to maintain a steady temperature. Use weatherstripping or caulk for sealing.
Intertherm Furnace Troubleshooting Steps
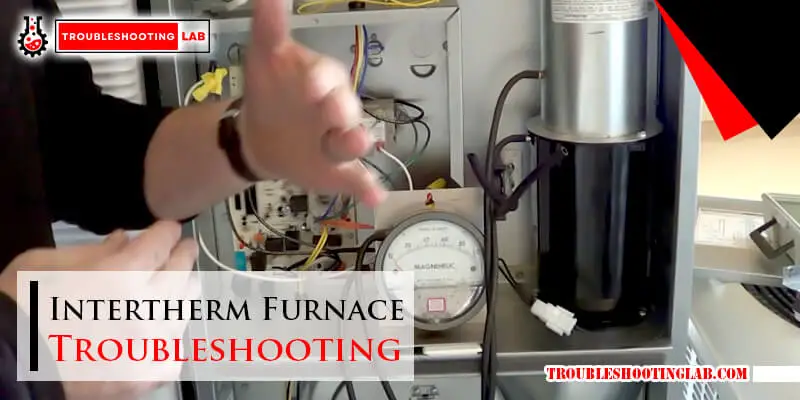
Is your Intertherm furnace acting up? Follow these basic troubleshooting steps. These steps can help you identify and fix common issues.
Check Thermostat Settings
The thermostat controls the furnace. Ensure the settings are correct. Set the thermostat to “Heat” mode. Ensure the temperature is set higher than the room temperature.
Verify the fan setting is on “Auto.” This ensures the fan runs only when heating. If set to “On,” the fan runs constantly, even when not heating.
- Ensure the thermostat has working batteries.
- Check for any error messages on the display.
- Make sure the thermostat is clean and free of dust.
Inspect Power Supply
A furnace needs power to operate. Check the power supply to the furnace. Ensure the furnace is plugged in securely. Check the circuit breaker. Ensure it is not tripped.
If the breaker is tripped, reset it. If it trips again, call a professional. Inspect the furnace switch. Ensure it is in the “On” position.
Look for any blown fuses. Replace them if necessary. Check the power cord for any damage. If damaged, replace the cord.
Component | Action |
---|---|
Thermostat | Verify settings and batteries |
Circuit Breaker | Ensure not tripped |
Furnace Switch | Ensure “On” position |
Power Cord | Check for damage |
Following these steps can resolve many furnace issues. Always ensure safety first. If unsure, contact a professional for help.
Ignition Problems
Ignition problems can halt your Intertherm furnace’s operation. This section helps you troubleshoot these issues. Ignition problems often arise from two main sources: pilot light issues and electronic ignition faults. Understanding and addressing these can restore warmth to your home.
Pilot Light Issues
The pilot light is crucial for older furnace models. If the pilot light goes out, the furnace will not ignite.
- Check for Gas Supply: Ensure the gas supply is on. Turn the valve to the open position.
- Inspect the Pilot Light: Look for a steady blue flame. If it’s flickering or yellow, there may be a problem.
- Clean the Pilot Orifice: Dust and debris can block the orifice. Use a needle to clear it.
- Replace the Thermocouple: A faulty thermocouple can cause the pilot light to go out. Replace it if necessary.
Electronic Ignition Faults
Modern furnaces use electronic ignition systems. These systems can sometimes fail, leading to ignition problems.
- Check the Power Supply: Ensure the furnace is plugged in. Check the circuit breaker and reset if needed.
- Inspect the Ignitor: The ignitor should glow when the furnace starts. If it doesn’t, it may need replacing.
- Test the Flame Sensor: A dirty flame sensor can prevent ignition. Clean it with a fine sandpaper.
- Examine the Control Board: Look for any error codes. Refer to the manual for troubleshooting steps.
Proper maintenance can prevent many ignition problems. Regularly inspect and clean components. This ensures your furnace runs smoothly all winter long.
Blower Motor Malfunctions
Experiencing issues with your Intertherm furnace? Blower motor malfunctions can cause significant problems. These issues can disrupt the efficiency of your heating system. Understanding common blower motor malfunctions can help you troubleshoot effectively.
Strange Noises
Strange noises from your blower motor can indicate various issues. These noises might include:
- Squealing: This often means a worn-out belt.
- Rattling: Loose or broken components could be the cause.
- Grinding: Worn-out bearings might be to blame.
Regular maintenance can prevent such issues. Address them promptly to avoid further damage.
Blower Not Running
If your blower is not running, several factors could be at play. Check these possible causes:
- Power Supply: Ensure the furnace is receiving power.
- Thermostat Settings: Verify the thermostat is set correctly.
- Blown Fuse: Replace any blown fuses in the system.
- Motor Overload: An overheated motor may need a reset.
Consult your furnace’s manual for specific troubleshooting steps. If issues persist, seeking professional help may be necessary.
Filter And Airflow Concerns

Intertherm furnaces need clean air filters and unblocked vents for proper airflow. Filters and vents directly affect furnace performance. Let’s dive into common issues.
Dirty Filters
Dirty filters block airflow and strain the furnace. This leads to higher energy bills and reduced efficiency. Changing filters regularly is essential.
Here are signs of dirty filters:
- Reduced airflow from vents
- Increased dust in the home
- Higher utility bills
- Frequent furnace cycling
Replace filters every 1-3 months. Check them monthly to ensure they are clean. Use high-quality filters for better performance.
Blocked Vents
Blocked vents can cause uneven heating and furnace overheating. Keep all vents open and unblocked to ensure proper airflow.
Here are signs of blocked vents:
- Cold spots in rooms
- Furnace shutting down frequently
- Unusual noises from the furnace
Check vents for obstructions like furniture, drapes, or debris. Clean vents regularly to maintain airflow.
Proper airflow ensures your Intertherm furnace runs efficiently. Regular maintenance of filters and vents is key.
Thermostat Malfunctions
Intertherm furnace issues can often be traced back to thermostat malfunctions. The thermostat controls the furnace’s operation. If it malfunctions, your furnace may not work correctly. Understanding the common thermostat issues can help you troubleshoot and fix the problem quickly.
Calibration Issues
Calibration issues can cause the thermostat to misread the room temperature. This can lead to the furnace not turning on or off at the right time. You can check the calibration with a simple thermometer. Place the thermometer next to the thermostat and compare readings. If they differ significantly, calibration is needed.
To recalibrate your thermostat:
- Turn off the furnace power.
- Remove the thermostat cover.
- Locate the calibration screw.
- Use a small screwdriver to adjust the screw.
- Test the thermostat again.
If recalibration does not fix the issue, the thermostat may need replacement.
Wiring Problems
Wiring problems can also affect the thermostat’s function. Loose or damaged wires can disrupt the connection, causing the furnace to malfunction. Inspect the wiring for any signs of wear or damage.
Steps to check the wiring:
- Turn off the furnace power.
- Remove the thermostat cover.
- Inspect the wires for any breaks or corrosion.
- Tighten any loose connections.
- Replace any damaged wires.
If you are not comfortable handling electrical components, contact a professional technician. Proper wiring ensures the thermostat sends accurate signals to the furnace.
Gas Supply Issues
Experiencing gas supply issues can be frustrating. It often leads to your Intertherm furnace not working correctly. These issues are usually due to either gas valve problems or gas line leaks. Understanding these problems can help you troubleshoot your furnace effectively.
Gas Valve Problems
The gas valve controls the flow of gas to your furnace. If it malfunctions, your furnace won’t get the gas it needs. Here are some common signs of gas valve problems:
- Furnace not igniting
- Intermittent heating
- Strange noises from the furnace
To check the gas valve, follow these steps:
- Turn off the furnace.
- Locate the gas valve near the furnace.
- Inspect for visible damage or wear.
- Ensure the valve is in the “on” position.
If you find any issues, consider calling a professional. Do not attempt to repair the gas valve yourself.
Gas Line Leaks
Gas line leaks are serious and need immediate attention. Signs of a gas leak include:
- Smell of gas (rotten eggs)
- Hissing sound near the gas line
- Dead or dying plants near the gas line
If you suspect a gas leak:
- Turn off the gas supply immediately.
- Evacuate the area.
- Call your gas company or emergency services.
Never attempt to fix a gas leak on your own. Safety should always be your top priority.
Problem | Signs | Action |
---|---|---|
Gas Valve Problems | Furnace not igniting, intermittent heating, strange noises | Inspect the valve, call a professional |
Gas Line Leaks | Smell of gas, hissing sound, dead plants | Turn off gas, evacuate, call emergency services |
Professional Maintenance Tips

Maintaining your Intertherm furnace is crucial for its longevity. Regular maintenance helps prevent unexpected breakdowns and ensures optimal performance. Below are some professional maintenance tips to keep your Intertherm furnace running smoothly.
Regular Inspections
Regular inspections are essential for identifying potential issues early. Check the furnace filters monthly. Replace them if they are dirty. Clean filters improve airflow and efficiency. Inspect the blower motor and belts. Look for signs of wear or damage.
Examine the electrical connections. Tighten any loose wires. Ensure the thermostat is working correctly. A well-functioning thermostat maintains the desired temperature. Check for any unusual noises. Strange sounds can indicate mechanical problems.
Annual Servicing
Schedule annual servicing by a professional technician. They will perform a thorough inspection. This includes cleaning and adjusting components. The technician will check the heat exchanger for cracks. A cracked heat exchanger can be dangerous.
They will also test the furnace’s safety controls. These controls ensure safe operation. The technician will measure the furnace’s efficiency. This helps in identifying any performance issues. Regular servicing extends the life of your furnace.
Below is a table summarizing the key tasks for annual servicing:
Task | Description |
---|---|
Heat Exchanger Inspection | Check for cracks and damages |
Safety Controls Test | Ensure all safety mechanisms are functional |
Efficiency Measurement | Assess the furnace’s performance levels |
Following these tips will help maintain your Intertherm furnace. Regular inspections and annual servicing are key. Keep your furnace in top condition for years to come.
Frequently Asked Questions
How Do I Reset My Intertherm Furnace?
To reset your Intertherm furnace, locate the reset button on the motor. Press and hold it until the furnace restarts.
Why Is My Intertherm Furnace Not Heating?
Check the thermostat settings, ensure the gas supply is on, and inspect for any tripped circuit breakers.
What Does A Blinking Red Light Mean?
A blinking red light indicates an error code. Refer to your furnace’s manual for specific troubleshooting steps.
How Often Should I Change The Furnace Filter?
Change the furnace filter every 1-3 months to maintain optimal performance and improve indoor air quality.
Why Is My Furnace Making A Loud Noise?
Loud noises can result from loose components, dirty burners, or a failing motor. Inspect these parts and tighten or clean as needed.
Conclusion
Regular maintenance and timely troubleshooting can extend your Intertherm furnace’s life. Follow the tips provided to ensure optimal performance. If issues persist, consult a professional technician. Keeping your furnace in good shape ensures a warm and comfortable home during cold months.
Stay proactive and enjoy a trouble-free heating experience.
model-E7EU-010H1, my furnace is throwing a code #1 blower motor failure . I’ve checked running amps registers 3.6A. The furnace will run for a period, then trip and lock out. a manual restart is required. I’ve checked airflow, filter all are clear and clean . This is an extremely clean and well installed unit. I don’t have a continuous amp monitor to see if i have a graduation in amps to cause a trip. Do you have any ideas to check . I don’t want to condemn a good motor. Some help, please. Thank You!
Hi there! It sounds like you’ve done a thorough job troubleshooting so far—great work on checking the airflow, filter, and running amps. Here are a few additional things you might consider:
If you’ve gone through all these steps and the issue persists, it might be worth consulting a technician before replacing the motor. Sometimes, diagnostic tools like an oscilloscope can identify hidden issues with the motor or control board.