Lantech Q300 Troubleshooting: Expert Tips for Quick Fixes
Facing issues with your Lantech Q300? Don’t worry, we’ve got you covered.
Troubleshooting can save time and money. The Lantech Q300 is a reliable stretch wrapping machine, yet like any equipment, it can face occasional issues. Knowing how to troubleshoot common problems can keep your operations running smoothly. This guide will help you identify and resolve frequent glitches.
From mechanical hitches to electrical faults, we will cover various troubleshooting steps. Understanding these basics ensures minimal downtime and maximizes efficiency. Let’s dive into the essentials of Lantech Q300 troubleshooting, so you can get back to wrapping with ease.
Credit: www.scribd.com
Introduction To Lantech Q300
Facing issues with your Lantech Q300? This guide covers common troubleshooting steps to keep your machine running smoothly. Save time and reduce downtime with easy-to-follow solutions.
The Lantech Q300 is a popular stretch wrap machine. It is known for its reliability and efficiency. Many industries use it for wrapping pallets securely. This machine helps save time and reduce labor costs.Key Features
The Lantech Q300 has many useful features. It includes an easy-to-use control panel. This allows operators to set wrap parameters quickly. The machine also has a robust construction. This ensures it can handle heavy loads and long hours of work. Another key feature is the automatic film delivery system. This system ensures consistent film tension. It helps in achieving a tight wrap every time. The Q300 also has a safety system. This system stops the machine if it detects any issues.Common Issues
Despite its reliability, the Lantech Q300 may face some issues. One common problem is film breakage. This can happen if the film tension is too high. Another issue is the turntable not spinning. This might be due to a faulty motor or sensor. Operators may also encounter problems with the control panel. Sometimes, it may not respond or display error messages. Regular maintenance can help prevent these issues. It is important to check the machine regularly. This ensures it operates smoothly and efficiently. “`Safety Precautions
When troubleshooting the Lantech Q300, it is vital to follow safety precautions. This ensures the well-being of both the operator and the machine. Following these guidelines can prevent accidents and costly repairs. Below are detailed safety precautions categorized into personal safety and machine safety.
Personal Safety
Personal safety is the top priority while working with the Lantech Q300. Follow these steps to ensure your safety:
- Wear appropriate personal protective equipment (PPE) including gloves and safety glasses.
- Ensure the machine is turned off and unplugged before starting any troubleshooting.
- Avoid wearing loose clothing or jewelry that can get caught in the machinery.
- Keep hands and other body parts away from moving parts of the machine.
- Make sure your work area is well-lit and free from obstructions.
Machine Safety
Machine safety is also crucial to maintain the integrity of the Lantech Q300. Follow these guidelines to protect the machine:
- Inspect the machine for any visible damage before starting the troubleshooting process.
- Use only the tools and parts specified in the Lantech Q300 manual.
- Ensure all safety guards and covers are in place before operating the machine.
- Do not bypass or disable any safety switches or devices.
- Regularly check and maintain the machine according to the manufacturer’s recommendations.
Adhering to these safety precautions can help you troubleshoot the Lantech Q300 effectively and safely.
Initial Diagnostics
The Lantech Q300 stretch wrapper is a vital machine in many warehouses. When it stops working, you need to troubleshoot quickly. The first step is to run initial diagnostics. This helps identify the issue and speeds up repairs.
Visual Inspection
Start with a visual inspection. This is the easiest way to find obvious problems. Look for loose wires, broken parts, and leaks. Check if the stretch film is loaded correctly. Make sure all safety guards are in place.
- Inspect the power connections.
- Ensure the emergency stop is not activated.
- Check for any physical damage to the machine.
A quick look can save time. It may reveal simple issues that are easy to fix.
Error Codes
The Lantech Q300 shows error codes on its control panel. These codes help diagnose problems. Each code points to a specific issue.
Error Code | Meaning | Possible Solution |
---|---|---|
E01 | Film Break | Reload the film and reset the machine. |
E02 | Turntable Fault | Check the turntable motor and sensors. |
E03 | Low Battery | Charge or replace the battery. |
Refer to the manual for a complete list of error codes. Understanding these codes can help you fix the machine faster.
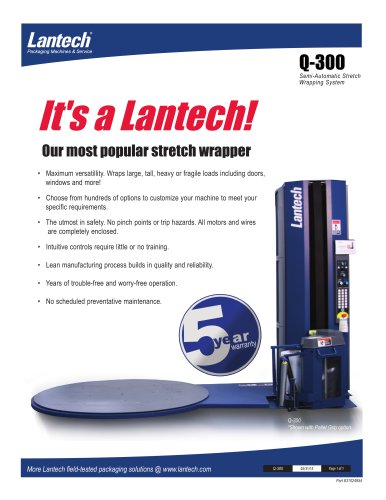
Credit: pdf.directindustry.com
Electrical Issues
Electrical issues can disrupt the performance of your Lantech Q300. These issues are common but fixable with some basic troubleshooting. Understanding and fixing electrical problems can extend the life of your machine.
Power Supply Problems
Power supply issues often cause the Lantech Q300 to malfunction. First, check if the machine is receiving adequate power. Ensure the power cord is properly connected. Look for any visible damage on the cord.
If the power cord is fine, inspect the power outlet. Use a multimeter to check the voltage. The outlet should provide the correct voltage as specified in the machine’s manual. If the voltage is incorrect, contact a professional electrician.
Sometimes, the internal power supply unit may be faulty. In this case, replacing the unit might solve the problem. Always follow the manufacturer’s guidelines for safe replacement.
Wiring Checks
Wiring issues can also affect the Lantech Q300. Loose or damaged wires can cause intermittent problems. Inspect all the wires in the machine carefully. Look for any signs of wear or damage.
Tighten any loose connections. Ensure all wires are securely attached. If you find any damaged wires, replace them immediately. Use wires that match the specifications in the manual.
After checking the wires, test the machine. This can help identify if the issue persists. If problems continue, consider consulting a professional technician.
Mechanical Problems
Mechanical issues can interrupt the smooth operation of your Lantech Q300. Identifying and resolving these problems quickly is essential. Understanding how to troubleshoot common mechanical issues will keep your machine running efficiently. Below, we will discuss two key areas: Belt Tension and Roller Alignment.
Belt Tension
Proper belt tension is crucial for the Lantech Q300’s performance. An improperly tensioned belt can cause slippage, reduced efficiency, and even damage. To ensure your belts are correctly tensioned, follow these steps:
- Turn off and unplug the machine.
- Locate the belt tension adjustment screws.
- Use a wrench to adjust the tension screws. Tighten or loosen them as needed.
- Check the belt tension manually. It should be tight but not overly so.
- Reassemble and test the machine.
If you notice excessive wear or damage to the belt, it might need replacing. Keeping belts in good condition ensures the machine operates smoothly.
Roller Alignment
Roller alignment is another critical factor. Misaligned rollers can lead to uneven wrapping and potential damage to your products. Follow these steps to check and adjust roller alignment:
- First, turn off and unplug the machine.
- Next, locate the roller adjustment points.
- Use a level to check the roller alignment.
- Adjust the rollers using the provided screws or bolts.
- Ensure the rollers are parallel to each other and level.
Testing the machine after adjustment is important. Ensure the wrapping is even and consistent. Regularly check roller alignment to maintain optimal performance.
Proper maintenance of belt tension and roller alignment significantly improves the Lantech Q300’s efficiency and longevity. Regular checks and adjustments are key to preventing mechanical problems.
Control Panel Errors
Troubleshooting control panel errors on the Lantech Q300 can be daunting. These errors often halt operations and cause delays. Recognizing common issues and understanding how to resolve them can save you time.
Resetting The System
Resetting the system is often the first step in troubleshooting. A simple reset can solve many minor glitches. Follow these steps to reset your Lantech Q300:
- Turn off the power switch located on the control panel.
- Wait for 30 seconds to ensure a complete shutdown.
- Turn the power switch back on.
If the error persists, consult the user manual for further instructions. Sometimes, a deeper reset procedure might be needed.
Software Updates
Keeping the software updated is crucial. Software updates fix bugs and improve performance. Here’s how to check and update your software:
- Go to the main menu on the control panel.
- Select ‘Settings’ and then ‘Software Update’.
- If an update is available, follow the on-screen instructions to install it.
Regular updates prevent many common errors. Check for updates at least once a month.
Film Delivery System
The film delivery system is crucial for the Lantech Q300 stretch wrapper. It ensures the film is correctly dispensed during wrapping. Proper functioning of this system helps maintain the quality and consistency of wrapped products. Understanding how to troubleshoot this part of the machine can save time and prevent issues.
Film Loading
Loading the film properly is vital for the machine to work efficiently. First, ensure the film roll is the correct size and type for the machine. Place the film roll on the carriage and secure it. Feed the film through the rollers as per the manual. Make sure the film is flat and free of wrinkles. Misaligned film can cause problems during wrapping.
Film Tension Adjustment
Film tension must be adjusted correctly for proper wrapping. Start by checking the tension settings on the machine. Adjust the tension knob or control to the recommended setting. Too much tension can tear the film. Too little tension can cause loose wrapping. Regularly monitor and adjust the tension to ensure optimal performance.
Preventive Maintenance
Preventive maintenance is essential for the Lantech Q300. It ensures the machine runs smoothly and minimizes downtime. Regular upkeep not only extends the lifespan of the equipment but also boosts its performance. Let’s delve into two key aspects of preventive maintenance: Regular Cleaning and Component Lubrication.
Regular Cleaning
Regular cleaning is crucial. Dust and debris can hinder the machine’s operation. Follow these steps to keep the Lantech Q300 clean:
- Wipe down surfaces with a soft cloth.
- Use compressed air to remove dust from tight spaces.
- Clean the film carriage and rollers.
Ensure all parts are free of contaminants. This prevents wear and tear. A clean machine runs more efficiently.
Component Lubrication
Proper lubrication ensures smooth operation. It reduces friction and prevents wear. Here’s a simple guide:
- Identify all moving parts.
- Apply manufacturer-recommended lubricant.
- Check for signs of wear.
Lubricate the following components:
- Roller bearings
- Chains and gears
- Film carriage slides
Regular lubrication extends the lifespan of components. It ensures the Lantech Q300 operates efficiently.
When To Call A Professional
Troubleshooting your Lantech Q300 can sometimes be straightforward. But there are moments when calling a professional is the best course of action. Understanding when to seek expert help can save time, money, and prevent further damage. Below, we discuss specific situations that require a professional’s expertise.
Persistent Issues
If your Lantech Q300 shows the same problem repeatedly, it’s a clear sign. Persistent issues can indicate deeper, underlying problems that need professional attention.
- The machine stops mid-cycle frequently.
- It shows error messages you can’t resolve.
- The wrap quality is consistently poor.
These issues, if left unchecked, can lead to more serious damage. A professional can diagnose and fix the root cause effectively.
Major Repairs
Some repairs are too complex to handle without technical knowledge. If you face major issues, it’s time to call a professional.
Examples include:
- Electrical problems.
- Motor malfunctions.
- Major component replacements.
Attempting these repairs without proper knowledge can be dangerous. It can also void your warranty. Professionals have the tools and expertise to handle these repairs safely.
Issue | Professional Required |
---|---|
Frequent Stoppages | Yes |
Error Messages | Yes |
Electrical Problems | Yes |
Motor Issues | Yes |
Credit: www.scribd.com
Frequently Asked Questions
What Causes My Lantech Q300 To Stop During Operation?
The Lantech Q300 may stop due to power issues or a tripped safety switch. Check these first.
How Can I Reset The Lantech Q300?
To reset, turn off the machine, wait a few seconds, then turn it on again.
Why Is My Lantech Q300 Wrapping Unevenly?
Uneven wrapping can be caused by incorrect film tension settings. Adjust the tension to fix this.
What Should I Do If The Lantech Q300 Film Breaks?
Check the film tension and load. Replace the film if it is damaged or too thin.
How Do I Maintain The Lantech Q300?
Regularly clean and lubricate moving parts. Check for wear and tear. Follow the maintenance schedule in the manual.
Conclusion
Troubleshooting the Lantech Q300 can be straightforward with the right steps. Regular maintenance helps prevent issues. Always check for common problems first. Replace worn parts promptly. Keep your machine clean and well-lubricated. Follow these tips for smooth operation. If problems persist, seek professional help.
Your machine will run efficiently with proper care. Happy wrapping!