Lift Axle Troubleshooting: Expert Tips for Smooth Operations
Lift axles are crucial for heavy-duty trucks. They help distribute weight and improve fuel efficiency.
But, what happens when they malfunction? Lift axle issues can cause serious problems for truck operators. Proper troubleshooting ensures your truck runs smoothly and safely. This guide aims to simplify lift axle troubleshooting for everyone. We will cover common problems and easy solutions.
Understanding these basics can save time and money. So, let’s dive into the world of lift axles and learn how to keep them in top condition.
Common Lift Axle Issues
Lift axles play a vital role in heavy-duty trucks and trailers. They help distribute weight and improve fuel efficiency. Yet, they can face several issues. Understanding these problems can save you time and money. Below, we explore some common lift axle issues you might encounter.
Uneven Tire Wear
Uneven tire wear is a frequent issue with lift axles. It often results from misalignment or improper inflation. This problem can lead to costly tire replacements.
Cause | Effect |
---|---|
Misalignment | Uneven tread wear |
Improper Inflation | Shortened tire lifespan |
To prevent this issue, regularly check your tire alignment and inflation. Use a tire gauge for accurate readings. Rotate tires as per the manufacturer’s recommendations.
Air Bag Failures
Air bag failures can cause significant problems. They support the weight and ensure a smooth ride. If they fail, it can lead to poor handling and increased wear on other components.
- Check for leaks regularly.
- Inspect the air lines and fittings.
- Replace worn or damaged air bags promptly.
A simple inspection can help identify potential issues. Look for cracks, leaks, or any signs of wear. Timely maintenance can prevent costly repairs.

Credit: www.youtube.com
Symptoms Of Malfunction
Understanding the symptoms of a malfunctioning lift axle is crucial. It helps in diagnosing issues early. This prevents further damage and ensures the safety of the vehicle.
Strange Noises
Do you hear unusual sounds? These noises can be a sign of trouble. A lift axle in good condition should operate quietly. Common noises include:
- Grinding: This may indicate worn-out bearings.
- Hissing: This could suggest air leaks in the system.
- Clunking: Loose or damaged parts can cause this sound.
Handling Problems
Handling issues are another sign of a malfunctioning lift axle. The vehicle may not steer or brake properly. Common handling issues include:
- Difficulty Steering: The vehicle might pull to one side.
- Poor Braking: Longer stopping distances could be required.
- Uneven Tire Wear: This can indicate misalignment or imbalance.
Address these issues promptly. Ignoring them can lead to major repairs and safety risks.
Preventative Maintenance
Preventative maintenance is key to ensuring the longevity and efficiency of lift axles. It helps in identifying potential issues before they become major problems. This practice not only saves money but also ensures the safety of the vehicle and its cargo. Below are some essential steps for maintaining lift axles effectively.
Regular Inspections
Conduct regular inspections of your lift axle. Check for any signs of wear or damage. Look at the tires, brakes, and suspension components. Make sure everything is in good condition. Replace any worn-out parts immediately.
Proper Lubrication
Ensure all moving parts are properly lubricated. Lubrication reduces friction and wear. Use the right type of lubricant for your lift axle. Follow the manufacturer’s recommendations. Regularly check the lubrication levels and top up if needed.
Diagnosing Electrical Problems
Diagnosing electrical problems in lift axles can be challenging. Electrical issues often stem from faulty wiring, damaged sensors, or other electrical components. Understanding how to troubleshoot these problems is crucial for maintaining a functional lift axle system.
Wiring Checks
Start by inspecting the wiring. Look for any signs of wear or damage. This includes frayed wires, loose connections, or corrosion. Use a multimeter to check for continuity. Ensure that all connections are secure and that there is no short circuit.
Step | Action |
---|---|
1 | Visually inspect all wires. |
2 | Check for loose connections. |
3 | Use a multimeter for continuity checks. |
4 | Repair or replace damaged wires. |
Sensor Testing
Sensors play a vital role in the operation of lift axles. Faulty sensors can lead to incorrect readings or malfunctioning systems. Use a diagnostic tool to test the sensors. Check for proper voltage and signal output.
- Identify the sensor type.
- Consult the service manual for specifications.
- Test the sensor with a multimeter.
- Replace faulty sensors.
Ensure all sensors are clean and properly aligned. Dirt or misalignment can affect sensor performance. Regular maintenance helps prevent sensor issues.
Hydraulic System Troubles
Hydraulic system troubles in lift axles can cause significant downtime. It’s crucial to identify and address issues promptly. This section will guide you through leak detection and pressure testing. These steps will help ensure your hydraulic system runs smoothly.
Leak Detection
First, inspect all hydraulic lines for visible leaks. Check connections, fittings, and hoses. Look for any drips or wet spots. Also, use a clean cloth to wipe around joints and seals. This helps reveal hidden leaks. Small cracks or loose fittings are common culprits. Fixing these can prevent bigger issues.
Pressure Testing
Pressure testing ensures your hydraulic system operates correctly. Begin by connecting a pressure gauge to the system. Start the lift axle and observe the gauge. The pressure should stay within the manufacturer’s specifications. If it’s too high or low, there may be a problem. Adjust the pressure settings if needed. Consistent pressure readings indicate a healthy system.
If you notice any irregularities, further investigation is necessary. Check for blockages or worn-out components. Replace any damaged parts immediately. This prevents further damage and costly repairs.
Adjusting Lift Axle Settings
Adjusting lift axle settings correctly ensures optimal performance and safety of your vehicle. Proper adjustments can prevent mechanical issues and enhance the load distribution. This section will guide you through two critical adjustments: Load Capacity Calibration and Height Adjustment.
Load Capacity Calibration
Calibrating the load capacity ensures the axle can handle the weight safely. Follow these steps to calibrate the load capacity:
- Locate the load capacity adjustment controls on your lift axle.
- Refer to the vehicle’s manual for specific load capacity limits.
- Adjust the settings to match the recommended load capacity.
- Test the axle with a load to ensure proper calibration.
Proper calibration helps prevent overloading and potential damage to the axle. Always check the load capacity before each trip.
Height Adjustment
Height adjustment is crucial for maintaining vehicle stability and ride quality. Here’s how to adjust the lift axle height:
- Park the vehicle on a level surface.
- Identify the height adjustment mechanism on the lift axle.
- Use the provided tools to adjust the height settings.
- Ensure the lift axle is at the correct height for your load.
Adjusting the height correctly improves fuel efficiency and reduces tire wear. Regularly check and adjust the height to match varying load conditions.
Properly adjusting your lift axle settings is essential for safe and efficient vehicle operation. By calibrating the load capacity and adjusting the height, you ensure your vehicle performs optimally under different load conditions.
Tools For Troubleshooting
Troubleshooting lift axle issues can be complex. Having the right tools is essential for accurate diagnosis and repair. This section will cover the tools for troubleshooting lift axle problems. You will learn about diagnostic equipment and essential hand tools needed for the job.
Diagnostic Equipment
Diagnostic equipment helps in identifying issues quickly. Here are some common tools:
- OBD-II Scanner: This tool reads error codes from the vehicle’s computer.
- Multimeter: Measures voltage, current, and resistance. Useful for checking electrical circuits.
- Pressure Gauge: Checks the air pressure in the lift axle system.
Using these tools, you can pinpoint problems accurately. This reduces guesswork and saves time.
Essential Hand Tools
Basic hand tools are also important. They allow for manual inspection and adjustments. Some essential hand tools include:
- Wrenches: For tightening and loosening nuts and bolts.
- Screwdrivers: Both flathead and Phillips are needed.
- Pliers: Useful for gripping and bending components.
- Socket Set: Provides a range of sizes for different bolts.
These tools are crucial for manual repairs. They help you perform detailed inspections and adjustments. Always keep them handy for efficient troubleshooting.

Credit: www.youtube.com
Professional Repair Services
Lift axle issues can cause significant disruptions. Addressing these problems swiftly is crucial. Professional repair services offer expertise and tools to fix these issues efficiently. Choosing a specialist and understanding costs can help ensure a smooth process.
Choosing A Specialist
Finding the right specialist is essential. Look for certified professionals with experience in lift axle repairs. Check their reviews and ask for recommendations. Ensure they have the necessary tools and knowledge.
It’s also important to verify their credentials. A certified technician guarantees quality service. Experience in the field also matters. An experienced professional can diagnose and fix issues faster. This can save time and money.
Cost Considerations
Repair costs can vary. Factors like the extent of damage and parts needed affect the price. Get multiple quotes to compare prices. This ensures you get a fair deal.
Always ask for a detailed estimate. This helps avoid unexpected charges. Understanding the breakdown of costs helps in budgeting. Some repairs may require replacement parts. The quality of these parts can impact the overall cost.
Remember, opting for the cheapest service isn’t always best. Quality repairs ensure longevity and safety. Investing in good service can save future repair costs.
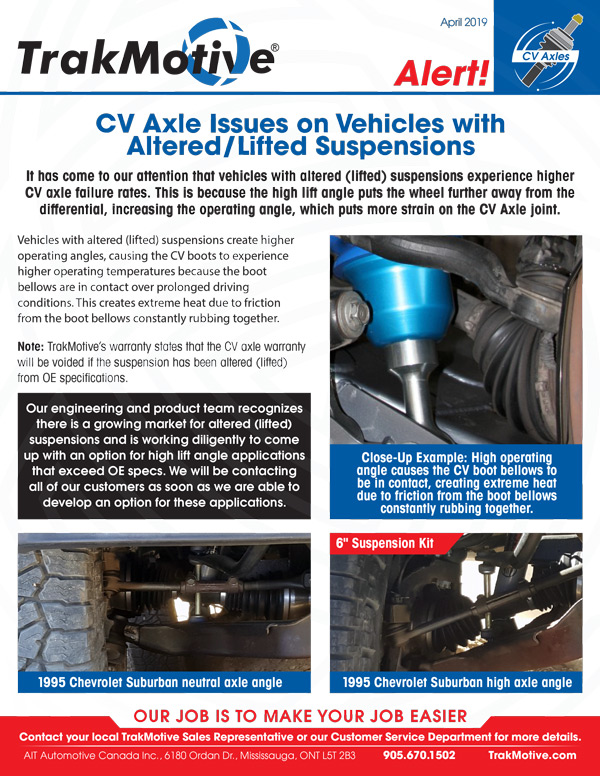
Credit: www.trakmotive.com
Frequently Asked Questions
What Causes Lift Axle Issues?
Lift axle issues can be caused by faulty wiring, air leaks, or worn-out components.
How Do I Check For Air Leaks In Lift Axles?
Listen for hissing sounds and use soapy water to spot bubbles indicating leaks.
Why Is My Lift Axle Not Lifting?
It may be due to low air pressure, faulty valves, or electrical problems.
What Maintenance Does A Lift Axle Need?
Regularly check air lines, electrical connections, and inspect for wear on mechanical parts.
Can I Drive With A Faulty Lift Axle?
It’s risky. A faulty lift axle can affect vehicle balance and safety. Get it fixed soon.
Conclusion
Understanding and addressing lift axle issues is crucial for vehicle performance. Regular maintenance prevents major problems. Listen for unusual noises. Inspect the axle components frequently. Address minor issues before they escalate. Consult a professional if needed. Safe and efficient transport depends on a well-functioning lift axle.
Keep your vehicle in top shape. Follow these troubleshooting tips. Enjoy smoother rides and longer-lasting equipment. Your vehicle will thank you.