Lochinvar Boiler Troubleshooting: Quick Fixes for Common Issues
For Lochinvar boiler troubleshooting, check the gas valve and pressure, clean the filters, and inspect the igniter. Proper maintenance and regular checks are crucial to prevent issues with your Lochinvar boiler.
If you reside in Austin, Texas, and rely on a Lochinvar boiler for heating, understanding how to troubleshoot common issues is essential. Whether it’s a gas valve problem, ignition failure, or blocked drain, knowing the necessary steps to address these issues can save you time and money.
Regular maintenance, including checking pressure, cleaning filters, and inspecting the igniter, can help prevent potential problems and keep your Lochinvar boiler running smoothly. In this guide, we’ll explore some common troubleshooting steps to help you address issues with your Lochinvar boiler effectively.
Introduction To Lochinvar Boiler Troubleshooting
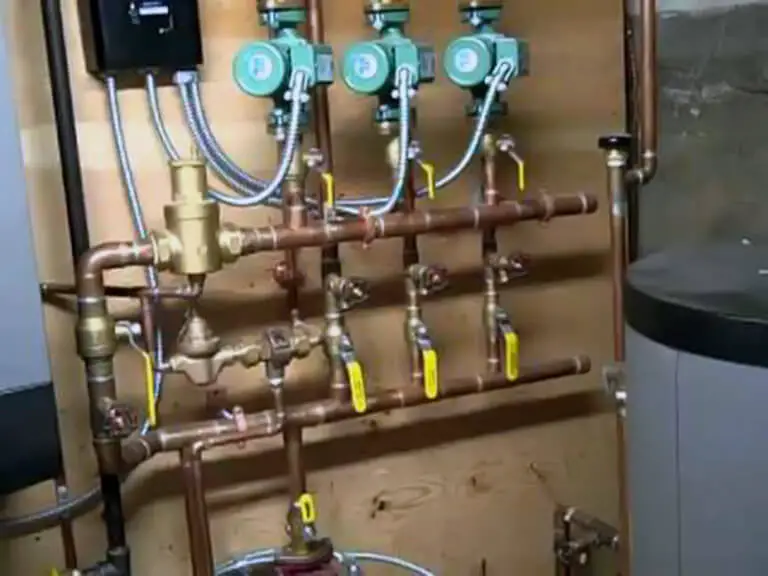
Discover the essential guide to Lochinvar boiler troubleshooting for effective problem-solving. From checking gas valves to adjusting pressure, this resource covers key steps to resolve common issues and keep your boiler running smoothly.
A Lochinvar boiler is a reliable and efficient heating system that provides warmth and comfort to your home or business. However, like any other appliance, it may experience issues that can affect its performance and safety. In this blog post, we will discuss the common symptoms of boiler issues and provide safety checks that you should perform before troubleshooting. We will also provide some tips on how to troubleshoot common Lochinvar boiler issues, including gas valve failure, ignition problems, and pressure concerns.
Common Symptoms Of Boiler Issues
If your Lochinvar boiler is experiencing issues, there are some common symptoms that you may notice. These include:
- No heat or hot water
- Strange noises, such as banging or gurgling
- Low pressure or leaks
- Inconsistent temperature
- Slow heating
If you notice any of these symptoms, it is important to perform safety checks before troubleshooting the issue.
Safety First: Pre-troubleshooting Checks
Before attempting to troubleshoot your Lochinvar boiler, it is essential to perform some safety checks. These include:
- Turn off the power supply to the boiler
- Check the pressure gauge to ensure it is in the safe range
- Check for any leaks or damage to the boiler
- Inspect the flue and ventilation system for any blockages or damage
- Make sure there is no gas smell in the area around the boiler
Once you have performed these safety checks, you can move on to troubleshooting your Lochinvar boiler.
In conclusion, if you are experiencing issues with your Lochinvar boiler, it is essential to perform safety checks before troubleshooting. By doing so, you can ensure that you and your property are safe while attempting to fix the issue. In the next section, we will discuss how to troubleshoot common Lochinvar boiler issues.
Ignition Failure Fixes
To troubleshoot ignition failure on a Lochinvar boiler, start by checking the pilot light and thermostat. Reset the boiler and verify the pressure before calling an engineer. Ensure proper installation of the system sensor in the primary loop for efficient functioning.
Pilot Light Problems And Solutions
If your Lochinvar boiler is experiencing pilot light issues, it could lead to ignition failure. Check the pilot light to ensure it is lit and burning steadily. Clean the pilot light assembly and remove any debris that may be blocking the flame. Inspect the thermocouple to see if it is functioning correctly. Replace the thermocouple if necessary.
Thermostat Troubleshooting Tips
The thermostat plays a crucial role in the ignition process of your boiler. Ensure the thermostat is set to the desired temperature and is functioning correctly. Check the wiring connections to the thermostat for any loose or damaged wires. Calibrate the thermostat if the temperature readings are inaccurate. Replace the thermostat if it is faulty.
Resetting The Boiler: A Step-by-step Guide
When facing ignition failure with your Lochinvar boiler, a simple reset may help resolve the issue. Locate the reset button on the boiler control panel. Press and hold the reset button for a few seconds to initiate the reset process. Wait for the boiler to restart and monitor if the ignition sequence initiates successfully. If the problem persists, consider seeking professional assistance.
By addressing pilot light issues, troubleshooting the thermostat, and knowing how to reset the boiler, you can effectively tackle ignition failure with your Lochinvar boiler.
Pressure Problems And Solutions
One common issue with Lochinvar boilers is pressure problems, which can lead to various performance issues. Understanding the symptoms of excessive pressure and knowing how to adjust the boiler pressure can help resolve these issues effectively.
Identifying Excessive Pressure
Excessive pressure in a boiler system can result in several telltale signs, such as unusual noises, leaks from pressure relief valves, and fluctuations in heating performance. Monitoring the pressure gauge on the boiler can help in identifying if the pressure is too high.
Adjusting Boiler Pressure
Adjusting the boiler pressure involves careful steps to ensure optimal performance. Start by switching off the boiler and allowing it to cool down. Then, locate the pressure gauge and the filling loop. Using the filling loop, adjust the pressure to the recommended level as per the manufacturer’s guidelines.
Error Codes And Meanings
When your Lochinvar boiler encounters an issue, it often communicates the problem through error codes. Understanding these error codes is crucial for effective troubleshooting. Here, we’ll delve into some common error codes and their meanings.
Deciphering The ‘blocked’ Code
If your Lochinvar boiler displays a ‘blocked’ code, it indicates that the blocked drain switch has detected excessive condensate build-up inside the unit. To address this, you should:
- Check the condensate tube from the unit to the floor drain for proper installation and obstructions.
- Inspect the condensate trap for any blockages.
Addressing The High Temperature Readout
When you encounter a high-temperature readout on your Lochinvar boiler, it could signal various issues, such as a faulty temperature sensor or other malfunctions. To troubleshoot this, consider:
- Checking the temperature sensors to ensure they are functioning correctly.
- Referencing the sensor tables to identify any irregularities.
- Consulting the troubleshooting table in the service manual for fault messages displayed on the boiler interface.
By understanding these error codes and their meanings, you can effectively diagnose and address issues with your Lochinvar boiler, ensuring optimal performance and functionality.
Sensor Issues And Calibration
When it comes to Lochinvar boiler troubleshooting, sensor issues and calibration play a crucial role in ensuring the efficient and smooth operation of the system. Addressing sensor-related issues promptly is essential for maintaining the optimal performance of your boiler.
Checking And Replacing Temperature Sensors
Temperature sensors are vital components of the boiler system, responsible for monitoring and regulating the temperature levels. If you encounter irregularities or malfunctions, it’s essential to check and replace the temperature sensors as necessary. This involves inspecting the sensor connections, assessing for any physical damage, and testing for accurate temperature readings.
Installing System Supply Sensors Properly
Proper installation of system supply sensors is critical for ensuring accurate temperature monitoring within the primary loop of the boiler system. Installing system supply sensors properly involves following the manufacturer’s guidelines, securing the sensor in the designated location, and calibrating it to ensure precise temperature measurements.
Maintenance And Cleaning Procedures
Regular maintenance and cleaning are essential to ensure the efficient and safe operation of your Lochinvar boiler. By performing routine maintenance tasks and keeping the boiler clean, you can prevent potential issues and extend the lifespan of your system. Below are the key maintenance and cleaning procedures that should be carried out to keep your Lochinvar boiler in optimal condition.
Performing A Boiler Strip And Clean
Performing a strip and clean procedure on your Lochinvar boiler is crucial to remove any accumulated debris and ensure the components are functioning properly. This process involves a thorough inspection and cleaning of various parts, including the heat exchanger, burner, and flue passages.
Cleaning And Maintenance Of The Flame Sensor
Regular cleaning and maintenance of the flame sensor are vital to ensure the proper ignition and combustion of the fuel. Over time, the flame sensor can accumulate dirt and soot, hindering its ability to detect the flame. Cleaning the flame sensor with a soft cloth or fine-grit sandpaper can help maintain its sensitivity and accuracy.
Electrical Troubleshooting
When dealing with Lochinvar boiler issues, Electrical Troubleshooting is essential to ensure smooth operation. Proper diagnosis and repair of electrical components can prevent breakdowns.
Voltage Checks For Motors And Inducers
Ensure motors and inducers are functioning correctly by conducting voltage checks. Follow these steps:
- Disconnect power supply.
- Using a multimeter, check voltage at the motor and inducer terminals.
- Compare readings to manufacturer specifications.
- If voltage is low or absent, inspect wiring and connections for damage.
Troubleshooting The Gas Valve And Electrical Connections
Proper functioning of the gas valve and electrical connections is crucial for boiler operation. Follow these steps:
- Inspect gas valve for any signs of damage or corrosion.
- Check electrical connections for tightness and signs of overheating.
- Test the gas valve solenoid for continuity using a multimeter.
- If issues are detected, replace faulty components promptly.
Regular maintenance and timely electrical troubleshooting can prevent costly repairs and downtime with your Lochinvar boiler.
Professional Help And When To Seek It
Boilers are complex pieces of equipment that require regular maintenance and occasional troubleshooting. While some issues can be resolved with simple DIY solutions, other problems require the assistance of a certified technician. In this section, we will discuss when to seek professional help and how to understand warranty and service manual advice.
When to Call a Certified Technician
It is important to know when to call a certified technician for Lochinvar boiler troubleshooting. If you encounter any of the following issues, it is recommended that you seek professional help:
- No hot water or heat
- Strange noises or odors coming from the boiler
- Water leaks
- Pilot light won’t ignite or stay lit
- Boiler won’t turn on or off
- Low pressure or temperature readings
Certified technicians have the necessary training, equipment, and experience to diagnose and repair complex issues that you may not be able to resolve on your own. Attempting to fix these problems yourself may lead to further damage or safety hazards.
Understanding Warranty and Service Manual Advice
When troubleshooting your Lochinvar boiler, it is important to consult the warranty and service manual for advice. These documents provide valuable information on how to properly maintain and repair your boiler. Here are some tips for understanding warranty and service manual advice:
- Read the manual carefully and thoroughly before attempting any repairs.
- Follow the recommended maintenance schedule to keep your boiler running smoothly.
- Only use recommended replacement parts and follow installation instructions carefully.
- Keep a record of all maintenance and repairs for future reference.
- If you are unsure about any advice in the manual, consult a certified technician.
By following the advice in the warranty and service manual, you can prevent many common issues and ensure your boiler runs efficiently for years to come.
In conclusion, knowing when to seek professional help and how to understand warranty and service manual advice is crucial for effective Lochinvar boiler troubleshooting. By following these guidelines, you can keep your boiler running smoothly and avoid costly repairs.
Frequently Asked Questions
How To Reset Maintenance On Lochinvar Boiler?
To reset maintenance on a Lochinvar boiler, follow these steps:
- Press the “Reset” button on the boiler control panel.
- Hold the button for 5 seconds until the maintenance light goes out.
- The maintenance reminder is now reset. Remember to refer to the specific boiler manual for detailed instructions.
Where Does The System Sensor Go On A Lochinvar Boiler?
The system sensor on a Lochinvar boiler should be installed in the Primary (building) loop.
How Do You Fix An Ignition Failure On A Boiler?
To fix an ignition failure on a boiler:
- Check the pilot light.
- Verify the thermostat.
- Reset the boiler.
- Inspect the pressure.
- Consider these steps before contacting an engineer for assistance.
What Does “blocked” Mean On A Lochinvar Boiler?
If your Lochinvar boiler displays the code “blocked”, it means that the blocked drain switch has detected excessive condensate buildup inside the unit. Check the condensate tube and trap for blockages or improper installation. It’s important to address this issue promptly to avoid further damage to your boiler.
Conclusion
Troubleshooting your Lochinvar boiler requires thorough checks on gas valves, pressure, and igniters. Regular maintenance and cleaning are key to preventing issues. Remember to follow manufacturer guidelines and seek professional help if needed. Keep your boiler running smoothly for optimal performance and efficiency.