Manitowoc Ice Machine Troubleshooting: Expert Tips and Tricks
If your Manitowoc Ice Machine is not making ice or producing low amounts of ice, there are a few troubleshooting steps you can take. First, check if the water service valve is open and if the water float valve and its filter screen are clean.
A dirty water float valve or filter screen can result in low ice capacity. Additionally, make sure the condenser is clean and free of obstructions, especially in air-cooled models. These simple steps can help identify and resolve common issues that may be causing your ice machine to malfunction.
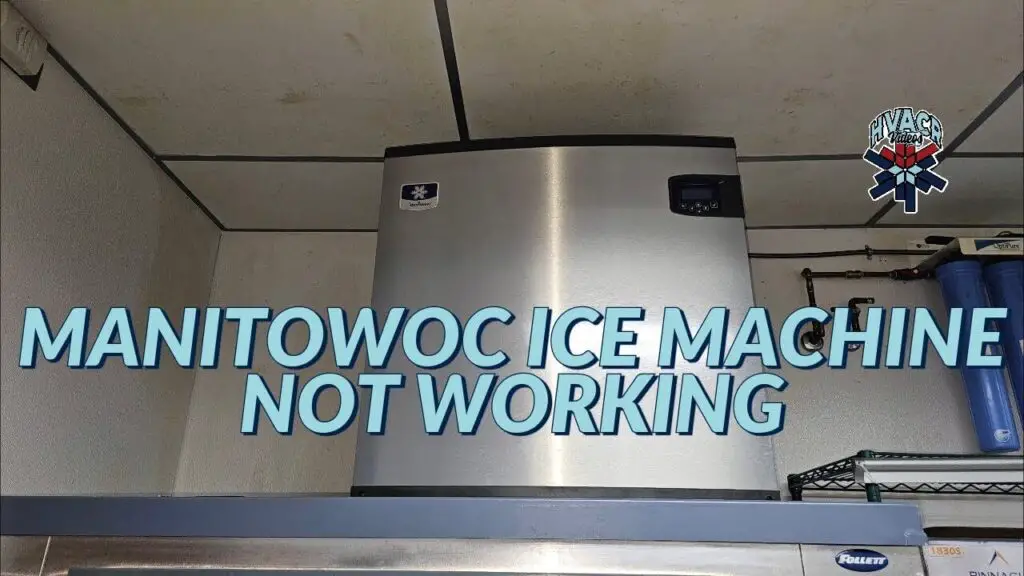
Understanding The Basics Of A Manitowoc Ice Machine
When it comes to reliable and efficient ice production, Manitowoc ice machines are a top choice for many businesses. These machines are designed to consistently produce high-quality ice, whether it’s for a restaurant, bar, hotel, or any other establishment. Understanding how a Manitowoc ice machine works and its key components is essential for troubleshooting any issues that may arise. In this section, we will explore the inner workings of a Manitowoc ice machine and help you identify common problems that may affect its performance.
how Does A Manitowoc Ice Machine WoWor
Manitowoc Ice Machine operates using a simple process that involves freezing and harvesting ice. Let’s break it down:
- The ice machine starts by filling a water trough or reservoir with water.
- A water pump then circulates the water over an evaporator plate or grid, which is kept at a freezing temperature.
- As the water flows over the evaporator, it begins to freeze, forming ice cubes or flakes, depending on the machine’s design.
- Once the ice reaches the desired thickness, the machine initiates the harvest cycle.
- During the harvest cycle, hot gas or water is used to release the ice from the evaporator plate or grid.
- The ice then falls into a storage bin or dispenser, ready to be used.
It’s important to note that different Manitowoc Ice Machine models may have slight variations in their operation, but the above steps give a general overview of how these machines work.
H3key Components Of A Manitowoc Ice Machine/h3
A Manitowoc Ice Machine consists of several key components that work together to ensure efficient ice production. These components include:
- Water pump: The water pump is responsible for circulating water over the evaporator, allowing it to freeze and form ice.
- Evaporator plate or grid: This component is where the water freezes and forms ice cubes or flakes, depending on the machine’s design.
- Compressor and condenser: The compressor compresses refrigerant gas, which then flows to the condenser. The condenser cools the refrigerant and helps release heat, maintaining the freezing temperature of the evaporator.
- Harvest assist mechanism: This mechanism aids in the release of ice from the evaporator during the harvest cycle, ensuring a smooth and efficient harvesting process.
- Control board: The control board regulates the overall operation of the ice machine, including monitoring and controlling various functions such as ice thickness, water level, and harvesting.
These are just a few of the key components that make up a Manitowoc Ice Machine. Each component plays a vital role in the ice production process, and any malfunction or issue with these parts can affect the machine’s performance.
Common Issues And Error Codes
Identifying Common Problems With Manitowoc Ice Machines
If you own a Manitowoc ice machine, you may encounter various issues that can hinder its performance. It’s important to quickly identify and troubleshoot these problems to ensure uninterrupted ice production. Below are some common problems you may encounter with your Manitowoc ice machine:
Troubleshooting Error Codes And Their Meanings
When your Manitowoc ice machine encounters a problem, it may display an error code to help you identify the issue. Understanding these error codes can save you time and money by allowing you to troubleshoot and potentially solve the problem on your own. Here are some common error codes you might come across:
– Error Code 1: This code indicates a water-related problem, such as a low water level or a water supply issue. Check the water supply valve and ensure it is properly connected and open. Also, inspect the water float valve and screen for any dirt or debris that may be blocking the flow of water.
– Error Code 2: This code signifies a high-pressure fault. It typically occurs when the condenser is dirty or obstructed. Make sure to clean the condenser and remove any debris or dust that may be hindering proper air circulation.
– Error Code 3: This code indicates a problem with the evaporator or its components. Inspect the evaporator for any ice buildup or blockages. Clean the evaporator and ensure it is functioning properly.
– Error Code 4: This code points to a harvest-related issue. It may occur if the ice machine is not properly releasing or harvesting the ice. Check for any obstructions or problems with the harvest system.
– Error Code 5: This code indicates a sensor fault. It may occur if there is a problem with the temperature sensors or their connections. Inspect the sensors and ensure they are properly connected and functioning.
By familiarizing yourself with these common issues and error codes, you can better troubleshoot and resolve any problems that arise with your Manitowoc ice machine. Remember to consult your user manual or contact a professional if you are unsure about the correct course of action.
Troubleshooting Steps For Specific Problems
No Ice Production Or Low Ice Capacity
If your Manitowoc ice machine is not producing ice or is producing low amounts of ice, there are a few troubleshooting steps you can take to identify and fix the problem.
Checking the Water Service Valve
First, check if the water service valve is open. If it is closed, the ice machine will not receive the necessary water supply for ice production. Ensure that the valve is fully open to allow water to flow into the machine.
Cleaning the Water Float Valve and Filter Screen
Next, examine the water float valve and its filter screen. A dirty float valve or clogged filter screen can lead to low ice capacity or no ice production. Remove any build-up or debris from the valve and screen, ensuring they are clean and free from obstructions.
Cleaning the Condenser
The condenser plays a crucial role in the ice production process. If it becomes dirty or obstructed, it can hinder the machine’s ability to produce ice efficiently. In air-cooled models, it is especially important to clean the condenser regularly. Make sure it is free of any dirt, dust, or other obstructions that may restrict airflow.
Harvesting Issues
If your Manitowoc ice machine is not harvesting or experiencing long harvest cycles, there are potential causes and solutions to explore.
Potential Causes and Solutions
One possible cause of long harvest cycles is cold weather conditions. In winter, the machine may take longer to harvest due to the lower ambient temperature. To address this issue, consider implementing a winter harvest setting if available.
Additionally, a malfunctioning water level sensor can also cause harvesting problems. If the sensor is not detecting the correct water level, it may delay or prevent the harvest cycle. Check the sensor and ensure it is functioning properly.
Furthermore, insufficient water flow or a malfunctioning water inlet valve can impact the harvesting process. Ensure there is proper water flow to the machine and that the inlet valve is functioning correctly.
Finally, a dirty or worn-out evaporator can hinder the harvesting process. Regular cleaning and maintenance of the evaporator can help prevent any issues related to ice harvest.
By following these troubleshooting steps for specific problems, you can identify and resolve common issues with your Manitowoc ice machine. Remember to consult the machine’s manual or contact a professional technician for further assistance if needed.
Regular Maintenance And Cleaning Tips
Keeping your Manitowoc ice machine clean and well-maintained is crucial for ensuring optimal performance and longevity. Regular maintenance not only helps to prolong the life of your machine but also ensures that it continues to produce high-quality ice consistently. In this section, we will provide you with a step-by-step guide to cleaning a Manitowoc ice machine, which will help you maintain peak performance.
Importance Of Regular Maintenance For Optimal Performance
Regular maintenance plays a vital role in keeping your Manitowoc ice machine running smoothly and efficiently. By following a routine maintenance schedule, you can prevent issues such as low ice production, slow ice harvest, and even system breakdowns. Regular maintenance helps to remove dirt, lime scale, and other contaminants that can build up over time and affect the performance of your machine.
Step-by-step Guide To Cleaning A Manitowoc Ice Machine
Cleaning your Manitowoc ice machine involves a few simple steps that should be followed regularly to maintain its performance. Here’s a step-by-step guide to cleaning your ice machine:
- Turn off the ice machine and unplug it from the power source.
- Remove all ice from the bin and discard it.
- Open the machine’s front panel to access the interior.
- Remove and clean the ice machine’s internal components, such as the evaporator, water trough, and water distribution tube. Refer to the machine’s manual for specific instructions on how to remove and clean these parts.
- Use a soft brush or cloth to gently scrub the components with a mixture of warm water and mild detergent. Avoid using harsh chemicals or abrasive materials, as they can damage the machine.
- Rinse off the cleaning solution with clean water and ensure that all the components are thoroughly clean and free from any residue.
- Sanitize the ice machine by using a solution of water and food-grade sanitizer. Follow the instructions provided by the sanitizer manufacturer for the appropriate dilution ratio.
- Pour the sanitizer solution into the water trough and let it circulate through the machine. Be sure to sanitize all surfaces thoroughly, including the interior and the ice bin.
- After sanitizing, drain and rinse the machine with clean water to remove any remaining sanitizer residue.
- Check and clean the ice machine’s condenser coils, fan, and air filters. These components are essential for proper airflow and heat dissipation. Remove any accumulated dirt or debris using a soft brush or vacuum.
- Once all the cleaning and maintenance tasks are complete, reassemble the machine and plug it back into the power source.
- Allow the machine to run for a few minutes to ensure that it is functioning correctly.
Regularly following these steps will help to keep your Manitowoc ice machine in top condition, ensuring efficient performance and clean ice production. Remember to refer to the machine’s manual for specific cleaning instructions and maintenance recommendations.
Keeping your Manitowoc ice machine well-maintained and clean is essential for optimal performance. The step-by-step guide provided above will help you effectively clean and maintain your machine, ensuring that it continues to produce high-quality ice consistently. By incorporating regular maintenance into your routine, you can enjoy years of trouble-free ice production from your Manitowoc ice machine.
References And Additional Resources
When it comes to troubleshooting your Manitowoc Ice Machine, it’s essential to have access to reliable resources and references. In this section, we will provide you with videos, manuals, and other resources that will help you troubleshoot and resolve any issues you may encounter with your ice machine.
Videos Demonstrating Manitowoc Ice Machine Troubleshooting
Watching videos can be a great way to visually understand the troubleshooting process. Below are some recommended videos that demonstrate Manitowoc Ice Machine troubleshooting:
- Video: Manitowoc Ice Machine Not Making Ice from HVACR Survival YouTube channel
- Video: Dirty Ice Machine from HVACR Survival YouTube channel
- Video: Manitowoc Ice machine Is not making Ice. Harvest issue. from REFRIGERATION KITCHEN TECH YouTube channel
Manuals And Resources For Further Troubleshooting Assistance
If you prefer written instructions and detailed guides, the following resources can provide valuable troubleshooting assistance:
- Website: Ice Maker Repair & Maintenance – Maintain Your Ice Machine by Smart Care Solutions
- Website: Manitowoc Ice Machine Troubleshooting by Parts Town
In addition to the above resources, it’s important to consult your specific Manitowoc Ice Machine model’s manual. The manual provides detailed information about operation, troubleshooting, and maintenance specific to your machine.
Remember, troubleshooting your Manitowoc Ice Machine can sometimes be complex, and it’s always recommended to seek professional assistance if you are unsure or unable to resolve the issue on your own.
Frequently Asked Questions
Why Is Manitowoc Ice Machine Not Making Ice?
The Manitowoc ice machine may not be making ice due to the following factors: 1. The Water service valve is closed. 2. Dirty water float valve or filter screen. 3. Dirty condenser, especially in air-cooled models. Make sure the water service valve is open and clean the float valve, filter screen, and condenser to resolve the issue.
How Do You Reset The Manitowoc Ice Machine?
To reset a Manitowoc ice machine, follow these steps: 1. Check if the water supply valve is open. 2. Clean the water float valve and its filter screen if dirty. 3. Clean the condenser and make sure there are no obstructions.
4. Adjust the ice thickness probe if needed. 5. Ensure the water level and temperature are within the correct range. For detailed troubleshooting, refer to the Manitowoc Ice Machine Troubleshooting Guide.
Why Is My Commercial Ice Machine Not Producing Ice?
Check if the water service valve is open. Clean the water float valve and its filter screen. Make sure the condenser is clean and free of obstructions. Ensure the water supply valve is switched on and the supply hose is connected properly. Clean the water-float valve and screen for proper ice production.
What Causes A Long Harvest On A Manitowoc Ice Machine?
A long harvest on a Manitowoc ice machine can be caused by several factors such as a dirty water float valve or filter screen, a dirty condenser, or a disconnected water supply. To correct this issue, make sure the water service valve is open, clean the float valve and filter screen, and ensure the condenser is clean and free of obstructions.
Why Is My Manitowoc Ice Machine Not Making Ice?
Make sure the water service valve is open and check if the water float valve and its filter screen are dirty.
Conclusion
To troubleshoot your Manitowoc Ice Machine, there are a few things you can check. Ensure the water service valve is open and the water float valve and screen are clean. Additionally, make sure the condenser is clean and free of obstructions.
For long harvest cycles, check the room and water temperatures, level the machine, and schedule regular deep cleaning. Remember to adjust the ice thickness probe if needed. By following these troubleshooting tips, you can keep your Manitowoc Ice Machine running smoothly and efficiently.