Miller Furnace Troubleshooting: Expert Tips for Quick Fixes
Miller furnaces are popular for their efficiency and reliability. But like any machine, they can have problems.
Understanding Miller furnace troubleshooting can save you time and money. Instead of calling a technician right away, you can often solve minor issues yourself. This blog post will guide you through common problems and their solutions. Whether your furnace won’t start, blows cold air, or makes strange noises, we’ve got you covered.
By learning these basic troubleshooting tips, you can keep your furnace running smoothly. Let’s dive into the details and help you become more confident with your Miller furnace.
Miller Furnace Troubleshooting For Common Issues
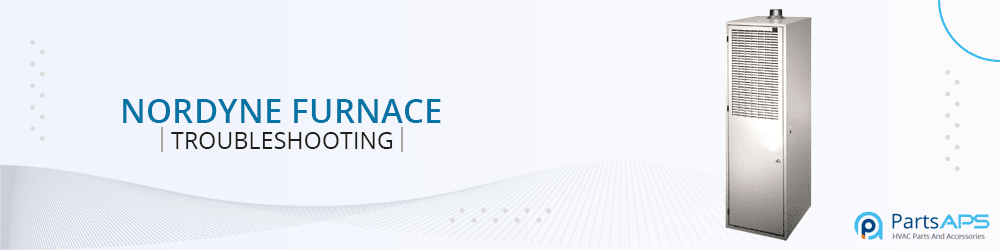
Miller furnaces are known for their reliability. But like all systems, they can encounter issues. Let’s discuss common problems and how to fix them.
No Heat
Experiencing no heat can be frustrating. Here are some possible causes:
- Thermostat Issues: Ensure the thermostat is set to “Heat”. Check the temperature setting. Replace batteries if needed.
- Power Problems: Check if the furnace is getting power. Look at the circuit breaker and ensure it is on.
- Pilot Light Out: If your furnace has a pilot light, check if it’s lit. Follow the manufacturer’s instructions to relight it.
- Clogged Filter: A dirty filter can block airflow. Replace the filter regularly.
Inconsistent Heating
Inconsistent heating can make your home uncomfortable. Here are some reasons why:
- Dirty Filters: A clogged filter can cause uneven heating. Replace filters every 1-3 months.
- Thermostat Location: If the thermostat is near a heat source, it might misread the temperature. Relocate it if needed.
- Blocked Vents: Ensure vents are open and not blocked by furniture or curtains. This allows proper airflow.
- Duct Issues: Leaky or poorly insulated ducts can cause uneven heating. Inspect and repair ducts if necessary.
Safety Precautions
Working on a Miller Furnace requires careful attention to safety. Always follow safety guidelines to avoid accidents and injury. Below are essential safety precautions to take before troubleshooting your furnace.
Turn Off Power
The first step is to turn off the power to the furnace. This prevents electric shocks and other hazards. Locate the furnace’s power switch or circuit breaker and switch it off. Confirm that the power is off before proceeding.
Wear Protective Gear
Always wear the right protective gear. This includes safety gloves, goggles, and long sleeves. Protective gear helps prevent burns, cuts, and other injuries. Ensure your clothing is not loose to avoid getting caught in moving parts.
Tools Needed
Troubleshooting your Miller furnace can seem like a daunting task. With the right tools, you can make the process much easier. This section will guide you through the essential tools needed for effective furnace troubleshooting.
Basic Tools
Start with basic tools that you likely already have. A Phillips screwdriver and flat-head screwdriver are essential for removing furnace panels. A wrench set is useful for loosening or tightening bolts. A multimeter helps to check electrical connections and ensure they are working correctly. Keep a flashlight handy for better visibility in dark spaces.
Specialized Equipment
Specialized equipment makes troubleshooting more efficient. An HVAC manometer measures gas pressure within the system. A combustion analyzer helps to check the furnace’s efficiency and safety. A thermocouple tester ensures that the thermocouple is functioning properly. These tools are essential for accurate diagnostics and repairs.
Checking Thermostat
When your Miller furnace stops working, the thermostat is often the first place to check. A faulty thermostat can cause many problems. This section will guide you through the steps of checking your thermostat. Follow these steps to ensure your furnace works properly.
Thermostat Settings
First, verify the thermostat settings. Ensure it is set to “Heat” mode. Also, set the temperature higher than the current room temperature. This step helps you know if the furnace is receiving the signal to turn on.
Setting | Action |
---|---|
Mode | Set to “Heat” |
Temperature | Set higher than room temperature |
Wiring Issues
Next, check for wiring issues. Turn off the power to the furnace before you begin. Remove the thermostat cover and inspect the wires. Ensure all wires are connected securely. Look for any damaged wires.
- Turn off power to the furnace.
- Remove the thermostat cover.
- Inspect the wires for secure connections.
- Check for damaged wires.
If you find any loose or damaged wires, fix them. Tighten loose connections. Replace any damaged wires. After fixing the wires, replace the cover and turn the power back on. Set the thermostat again and check if the furnace starts.
Inspecting Filters
Inspecting filters is a crucial step in Miller furnace troubleshooting. Clean filters ensure efficient operation. Dirty filters can lead to numerous problems. They can reduce airflow, increase energy consumption, and cause heating issues. Regular inspection helps maintain optimal performance.
Filter Condition
First, check the filter condition. Remove the filter from the furnace. Look for dust, dirt, and debris. A clean filter will appear white or light gray. A dirty filter will look dark and clogged. If the filter is dirty, it needs replacement.
Replacement Steps
Replacing the filter is simple. Follow these steps:
- Turn off the furnace. Safety first.
- Locate the filter compartment. This is usually near the blower.
- Remove the old filter. Take note of its size.
- Insert a new filter. Ensure it matches the size of the old one.
- Close the filter compartment. Make sure it’s secure.
- Turn the furnace back on. Check for proper operation.
Regular filter replacement is vital. It keeps your furnace running smoothly. Inspect filters monthly for best results.
Examining Pilot Light

When your Miller furnace is not heating, the pilot light might be the issue. The pilot light is crucial for igniting the furnace burners. Examining the pilot light is a key step in troubleshooting your furnace.
Pilot Light Status
First, check if the pilot light is on. Open the furnace cover and locate the pilot light assembly. A steady blue flame indicates a working pilot light. If you see no flame or a weak flame, there may be a problem.
Pilot Light Status | Possible Issue |
---|---|
No flame | Pilot light out |
Weak flame | Dirty pilot orifice |
Yellow flame | Insufficient gas or dirty pilot |
Relighting Procedure
If the pilot light is out, you need to relight it. Follow these steps:
- Turn off the gas valve. Wait five minutes to clear gas.
- Set the thermostat to the lowest setting.
- Turn the gas valve to the “pilot” position.
- Hold a lit match to the pilot opening.
- Press and hold the reset button until the pilot stays lit.
- Release the reset button and turn the gas valve to “on”.
- Set the thermostat to the desired temperature.
If the pilot light does not stay lit, it could be a thermocouple issue. The thermocouple ensures the pilot light stays on. If faulty, it may need replacement.
Regular maintenance can keep your furnace running smoothly. Clean the pilot light assembly and ensure the gas supply is adequate. For persistent issues, consult a professional technician.
Assessing Blower Motor
Assessing the blower motor is essential for ensuring your Miller furnace runs smoothly. This component is vital for circulating air throughout your home. Learn how to check its functionality and maintain it properly.
Motor Functionality
First, ensure the blower motor is functioning correctly. Turn off the furnace and locate the motor. Inspect it for visible damage or wear. Use a multimeter to check for electrical continuity.
- Step 1: Set the multimeter to the ohms setting.
- Step 2: Place the probes on the motor terminals.
- Step 3: Check the reading; it should not be zero.
If the motor shows no continuity, it may need replacement. Also, listen for unusual noises while the motor is running. Grinding or squealing sounds indicate issues.
Lubrication
Proper lubrication keeps the blower motor running smoothly. Check the owner’s manual to see if your motor requires lubrication. Some motors are sealed and do not need this.
- Step 1: Turn off the furnace and disconnect power.
- Step 2: Locate the oil ports on the motor.
- Step 3: Add a few drops of oil to each port.
Use the recommended oil type. Do not over-lubricate, as it can cause damage. Regular maintenance of the blower motor ensures optimal performance and longevity.
Professional Help
Furnaces can be complex. Sometimes, troubleshooting issues yourself might not be enough. Seeking professional help ensures safety and efficiency. It is crucial to know when to call a technician and how to choose the right service. Let’s dive into these aspects.
When To Call A Technician
Not all furnace issues require professional help. Some minor problems can be fixed easily. But certain signs indicate it’s time to call a technician:
- Strange Noises: If your furnace makes unusual sounds like banging or screeching.
- Frequent Cycling: The furnace turns on and off too often.
- No Heat: When the furnace is running but not producing heat.
- Yellow Pilot Light: A yellow or flickering flame instead of blue.
- High Energy Bills: Unexplained spikes in your energy costs.
If you notice any of these signs, it’s best to seek professional help. An expert can diagnose and fix the issue promptly.
Choosing The Right Service
Finding the right technician is vital. Not all services provide the same quality. Here are some tips to help you choose:
- Check Credentials: Ensure the technician is licensed and insured.
- Read Reviews: Look for reviews and testimonials from past customers.
- Experience: Choose a service with years of experience in furnace repair.
- Ask for References: Reliable services provide references on request.
- Get Quotes: Compare quotes from different services to find a fair price.
It’s important to ensure you choose a qualified and reliable technician. This will help maintain the efficiency and longevity of your furnace.
Frequently Asked Questions
Why Is My Miller Furnace Not Heating?
Your Miller furnace might not heat due to a malfunctioning thermostat or a dirty filter. Check both.
How Do I Reset My Miller Furnace?
Locate the reset button on your Miller furnace. Press and hold it for 30 seconds.
What Does A Flashing Red Light On My Furnace Mean?
A flashing red light indicates a possible error or malfunction. Consult the furnace manual or a technician.
Why Is My Miller Furnace Making Noise?
Your furnace could be noisy due to loose parts or a dirty blower motor. Inspect and clean as necessary.
How Often Should I Service My Miller Furnace?
Service your Miller furnace annually to ensure optimal performance and prevent potential issues.
Conclusion
Troubleshooting your Miller furnace can save time and money. Simple checks often solve common issues. Always ensure safety first. Remember to turn off the power before inspecting. If problems persist, consult a professional. Regular maintenance can prevent many issues. Keep your furnace running smoothly and efficiently.
Stay warm and comfortable all winter long. Proper care extends the life of your furnace. Follow these tips to avoid unnecessary headaches.