Pitco Fryer Troubleshooting Manual: Solve Common Issues Quickly
Pitco fryers are essential in many kitchens. They help cook food quickly and evenly.
But, like any equipment, they can face issues. A Pitco fryer troubleshooting manual can save you time and stress. It guides you through common problems and solutions. Whether your fryer won’t heat up or has oil leaks, this manual offers step-by-step fixes.
Knowing how to troubleshoot can keep your kitchen running smoothly. This guide will help you understand and solve typical Pitco fryer issues. Let’s dive into the most common problems and how to address them effectively. With this manual, you can ensure your Pitco fryer operates at its best.
Common Pitco Fryer Issues
Pitco fryers are reliable and efficient. Yet, like all appliances, they face issues. Understanding these common problems helps maintain your fryer. This guide covers the most frequent Pitco fryer issues.
No Power
Sometimes, a Pitco fryer may not power on. Check the power cord first. Ensure it is plugged in correctly. Next, inspect the outlet. Try plugging another device into the same outlet. If it does not work, the outlet may be faulty. Also, check the fryer’s power switch. Make sure it is in the “ON” position. If these steps do not help, the fryer may have an internal issue. Contact a professional technician for assistance.
Temperature Problems
Another common issue is temperature problems. Your fryer may not heat up properly. First, check the thermostat settings. Ensure they are correct. If the fryer overheats, the high-limit switch might be faulty. Reset the high-limit switch if necessary. Sometimes, debris blocks the thermostat sensor. Clean the sensor and check again. If temperature issues persist, call for professional help.
Oil Quality
Oil quality affects food taste and fryer performance. Poor oil quality can result from infrequent filtering. Regularly filter and change the oil. Overheating oil can degrade its quality. Monitor the fryer’s temperature settings. Ensure they are within the recommended range. Use only high-quality oil designed for frying. This helps maintain food quality and extends fryer life.
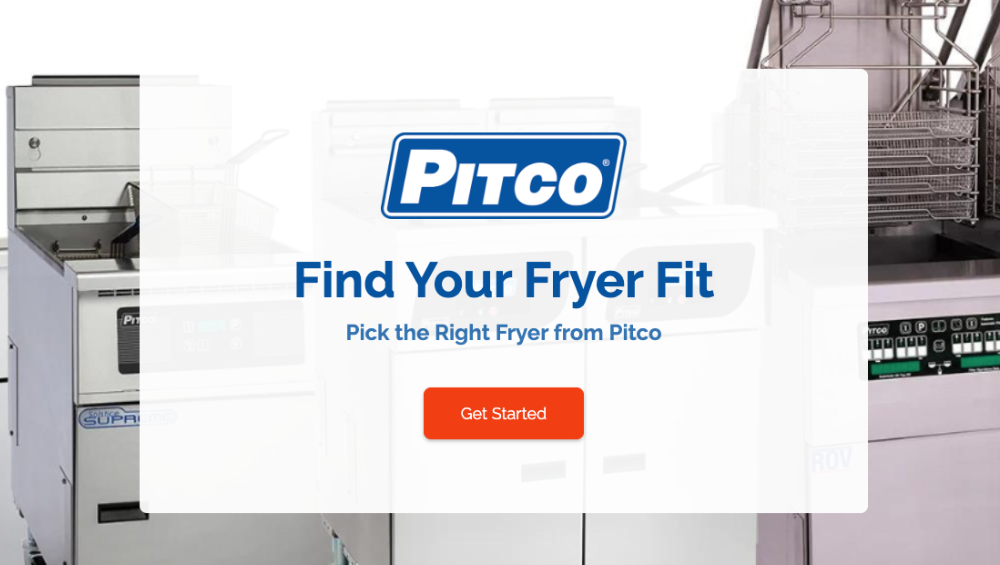
Credit: www.pitco.com
No Power Solutions
Experiencing no power issues with your Pitco fryer? This can be frustrating. But, don’t worry. You can fix many of these problems with a few simple steps. Let’s explore some solutions to get your Pitco fryer working again.
Check Power Source
First, verify that the fryer is properly plugged in. Sometimes, the plug may become loose. Ensure it’s securely inserted into the outlet. Also, check if the outlet is functioning. Plug another device into the same outlet to see if it works. If the device doesn’t work, the issue may be with the outlet.
Inspect Power Cord
Next, inspect the power cord for any visible damage. Look for cuts, frays, or exposed wires. If you see any damage, do not use the fryer. A damaged cord can be dangerous. Replace the power cord immediately to ensure safety and proper function.
Reset Circuit Breaker
If the power source and cord are fine, check the circuit breaker. Sometimes, the breaker may trip due to overload. Locate your main electrical panel. Find the breaker that controls the fryer. Flip it off, then back on. This simple reset can restore power to your fryer.
Temperature Problems Fixes
Dealing with temperature problems in your Pitco fryer can be frustrating. It can impact the quality of your fried foods and disrupt your kitchen operations. This section will guide you through common temperature issues and how to fix them. Let’s dive into thermostat calibration, faulty heating elements, and thermopile issues.
Thermostat Calibration
A miscalibrated thermostat can lead to incorrect temperature readings. This affects cooking times and food quality. Follow these steps to calibrate your thermostat:
- Turn off the fryer and let it cool.
- Locate the thermostat knob and remove it.
- Use a calibration tool to adjust the screw behind the knob.
- Turn the screw clockwise to increase temperature, counterclockwise to decrease it.
- Replace the knob and test the fryer temperature with a thermometer.
Repeat these steps until the temperature matches your desired setting.
Faulty Heating Element
If your fryer is not heating properly, the heating element might be faulty. Check for these signs of a faulty heating element:
- Uneven heating
- Slow heating times
- Visible damage or corrosion
To replace a faulty heating element:
- Turn off the fryer and disconnect it from the power source.
- Remove the fryer pot to access the heating element.
- Disconnect the wiring from the element.
- Remove the screws holding the element in place.
- Install the new heating element by reversing these steps.
Ensure all connections are secure before powering the fryer back on.
Thermopile Issues
The thermopile converts thermal energy into electrical energy. It powers the gas valve and maintains the pilot light. Common thermopile issues include:
- Weak or no pilot flame
- Intermittent heating
- Fryer not reaching set temperature
To troubleshoot thermopile issues:
- Check the pilot light. Clean it if necessary.
- Test the thermopile with a multimeter. It should read between 300-750 millivolts.
- If the reading is low, replace the thermopile.
Proper thermopile function is crucial for consistent fryer performance.
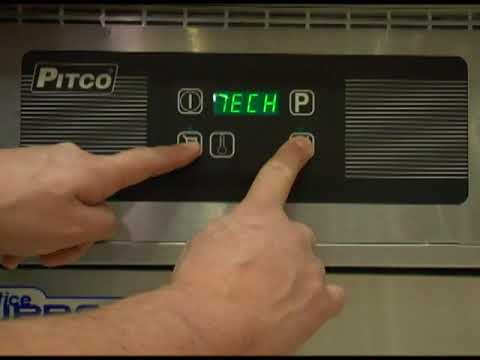
Credit: www.youtube.com
Oil Quality Maintenance
Maintaining the oil quality in your Pitco Fryer is essential. It ensures food tastes great and your equipment runs efficiently. Good oil quality also extends the life of your fryer. Let’s explore some key practices for oil quality maintenance.
Regular Filtering
Regular filtering of oil is crucial. It removes food particles and contaminants. This helps to keep the oil clean and safe for cooking. Filtering should be done daily.
- Use a filter machine or a built-in filtration system.
- Allow the oil to cool before filtering.
- Follow the fryer’s manual for specific filtering instructions.
Regular filtering keeps the oil clear and extends its usage life.
Oil Replacement Schedule
Replacing oil is necessary to maintain food quality. Even with regular filtering, oil degrades over time. Set an oil replacement schedule based on usage.
- Light usage: Replace oil every 2 weeks.
- Medium usage: Replace oil every 1 week.
- Heavy usage: Replace oil every 3-5 days.
Follow these guidelines to ensure consistently high-quality food.
Oil Storage Tips
Proper oil storage prolongs its usability. Store oil in a cool, dark place. Heat and light can degrade oil quality.
Tip | Description |
---|---|
Avoid sunlight | Store oil in opaque containers. |
Keep it cool | Ideal storage temperature is below 75°F (24°C). |
Sealed containers | Keep oil containers tightly sealed. |
These storage tips help maintain oil quality and extend its shelf life.
Pilot Light Troubleshooting
Pilot light issues can disrupt your Pitco fryer’s performance. Understanding how to troubleshoot the pilot light is essential. It ensures your fryer runs smoothly. This guide covers common pilot light problems and their solutions.
Pilot Won’t Stay Lit
A pilot light that won’t stay lit can halt your frying operations. First, check the thermocouple. It might be faulty. The thermocouple senses the pilot flame. If it is defective, the gas valve shuts off. Replace the thermocouple if needed. Ensure it is correctly positioned. The tip should be in the flame.
Pilot Burner Cleaning
A dirty pilot burner can cause issues. Debris can block the gas flow. Clean the pilot burner regularly. Use a brush or compressed air. Gently remove any dirt or buildup. Ensure the gas port is clear. A clean burner ensures a steady flame. Regular cleaning prevents many pilot light problems.
Gas Supply Check
Check the gas supply if the pilot light won’t stay lit. Ensure the gas valve is open. Verify the gas line is not kinked. Inspect for any leaks. A steady gas supply is vital. If the supply is interrupted, the pilot light will go out. Fix any gas supply issues promptly.
Burner Issues Resolution
Burner issues can disrupt your frying operations. Knowing how to resolve these issues is essential. This guide covers common burner problems and their solutions.
Burner Won’t Ignite
If the burner won’t ignite, check the power supply first. Ensure the fryer is plugged in and the power switch is on. Inspect the pilot light. If the pilot light is out, relight it. If it doesn’t stay lit, the thermocouple may be faulty. Replace the thermocouple if needed. Check the gas valve and ensure it is open. A closed gas valve will prevent ignition.
Burner Flame Adjustment
Proper flame adjustment is crucial for efficient frying. Observe the burner flame. It should be blue with a yellow tip. If the flame is too yellow, adjust the air shutter. Open the air shutter slightly to increase air intake. This should turn the flame blue. If the flame is too high or low, adjust the gas pressure. Consult the manual for the correct pressure settings.
Burner Cleaning
Regular cleaning ensures optimal burner performance. Turn off the fryer and let it cool. Remove the burner assembly carefully. Use a brush to clean the burner holes. Ensure no debris is blocking the holes. Wipe the burner with a damp cloth. Dry it thoroughly before reassembling. Check for any signs of corrosion or damage. Replace the burner if necessary.
Control Panel Problems
The control panel on your Pitco fryer is essential for its operation. When it malfunctions, it can disrupt your cooking process. This section will help you understand and fix common control panel issues. We will cover display malfunctions, button response issues, and control board resets.
Display Malfunctions
Is your display not showing correctly? First, check the power supply. Ensure the fryer is plugged in properly. Next, inspect for any loose connections. Loose wires can cause display issues. If the display is still malfunctioning, it might need a replacement. Consult your manual for specific instructions.
Button Response Issues
Are the buttons not responding? Start by cleaning the control panel. Grease and dirt can block the buttons. Use a soft cloth and mild cleaner. If cleaning doesn’t help, check for damage. Damaged buttons might need to be replaced. Refer to your manual for guidance.
Control Board Reset
Sometimes, a reset can fix many issues. To reset the control board, turn off the fryer. Wait for a few minutes. Turn it back on. This simple step can resolve many problems. If the issue persists, the control board might be faulty. Contact a professional for further assistance.
Preventive Maintenance Tips
Preventive maintenance is key for Pitco fryers. It extends their lifespan and ensures efficient operation. Following some basic tips can prevent breakdowns. This saves time and money. Below are some essential preventive maintenance tips.
Regular Cleaning
Clean your Pitco fryer daily. Wipe down the exterior. This prevents grease buildup. Clean the fryer pot with a soft brush. This removes food particles. Drain the oil and clean the tank weekly. Use warm water and mild detergent.
Routine Inspections
Inspect your Pitco fryer regularly. Check for leaks around the tank. Look at the gas connections. Ensure they are secure. Examine the thermostat. Make sure it reads accurately. Inspect the power cord. Look for any wear or damage.
Professional Servicing
Schedule professional servicing yearly. A technician can check all components. They will clean the internal parts. They will also replace any worn-out parts. Professional servicing keeps your fryer in top condition.
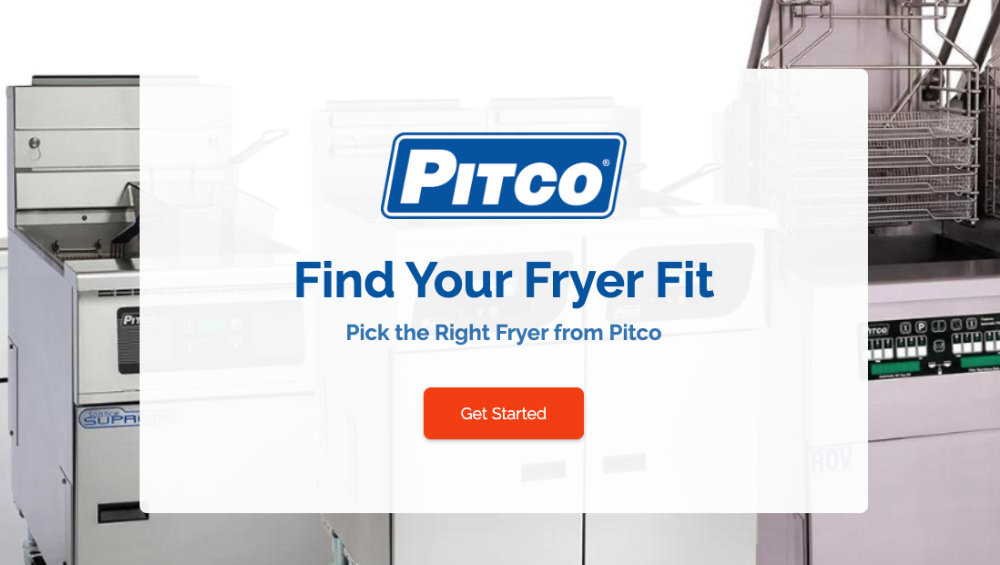
Credit: www.pitco.com
Frequently Asked Questions
How Do I Reset My Pitco Fryer?
To reset your Pitco fryer, press the reset button. It’s usually near the control panel.
Why Is My Pitco Fryer Not Heating Up?
Your fryer might not heat due to a faulty thermostat or heating element. Check and replace if needed.
What Should I Do If My Pitco Fryer Leaks Oil?
Check for loose connections or damaged seals. Tighten connections or replace seals to fix oil leaks.
How Often Should I Clean My Pitco Fryer?
Clean your fryer daily to prevent grease buildup. This ensures proper operation and longevity.
Why Does My Pitco Fryer Keep Turning Off?
Your fryer may turn off due to overheating or a faulty safety switch. Inspect and replace faulty parts.
Conclusion
Proper maintenance ensures your Pitco fryer works efficiently. Troubleshooting saves time and money. Always follow safety guidelines during repairs. Routine checks prevent major issues. Clean regularly to avoid buildup. Replace worn parts promptly. A well-maintained fryer cooks better. Happy frying!