Plasma Cutter Troubleshooting Guide: Essential Tips & Solutions
Plasma cutters are essential tools for metal workers. They provide precise, clean cuts.
But, like any tool, they can have issues. Troubleshooting these problems can be tricky without guidance. Understanding your plasma cutter’s common problems saves time and frustration. This guide helps identify and fix issues quickly. From poor cuts to machine malfunctions, we cover it all.
Whether you’re a beginner or an experienced user, knowing these tips ensures your plasma cutter works smoothly. Dive in to learn how to keep your tool in top shape. Let’s get started with the most common plasma cutter problems and their solutions.
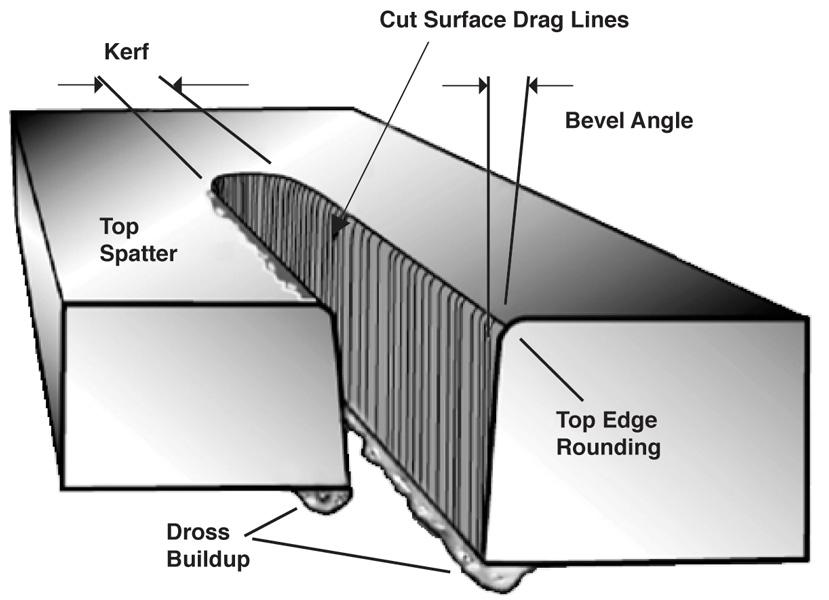
Credit: www.thefabricator.com
Introduction To Plasma Cutters
Plasma cutters are essential tools in many industries. They provide precise and efficient metal cutting. Understanding how they work can help you troubleshoot common issues. This guide offers a detailed look at plasma cutters and their components.
What Is A Plasma Cutter?
A plasma cutter is a device that cuts through electrically conductive materials. It uses a high-velocity jet of ionized gas, or plasma. The plasma conducts electricity from the cutter to the workpiece. This process melts the material, which is then blown away by the gas jet.
Plasma cutters are used in various fields. These include automotive repair, industrial construction, and metal fabrication. They can cut a range of metals, including steel, stainless steel, aluminum, brass, and copper.
Basic Components
Understanding the basic components of a plasma cutter is crucial. It helps in troubleshooting and maintaining the device.
Component | Description |
---|---|
Power Supply | Provides the electrical energy needed to create the plasma. |
Arc Starting Console | Creates a spark to ionize the gas, forming plasma. |
Plasma Torch | Holds the electrode and nozzle, directing the plasma. |
Electrode | Conducts the electrical current to the plasma arc. |
Nozzle | Constricts the plasma arc, increasing its intensity. |
Each component plays a vital role. The power supply ensures the device has enough energy. The arc starting console initiates the plasma arc. The torch directs the arc to the workpiece. The electrode and nozzle help maintain a stable, intense arc.
Regular maintenance of these components is essential. It ensures the plasma cutter functions correctly and efficiently. Cleaning and replacing worn parts can prevent many common issues.
Common Plasma Cutter Issues
Plasma cutters are essential tools in many workshops. But, they can encounter issues that disrupt work. Understanding these common problems helps in troubleshooting and ensures smooth operation. Below, we explore some frequent plasma cutter issues and how to fix them.
No Arc Starting
A common issue with plasma cutters is the failure to start an arc. This can stem from several causes. Here are some steps to identify and resolve this problem:
- Check the power supply. Ensure the plasma cutter is plugged in and turned on.
- Inspect the ground clamp. It should be securely attached to the workpiece.
- Examine the consumables. Worn out or damaged consumables can prevent arc starting.
- Verify air pressure. Incorrect air pressure settings can hinder arc formation.
If these steps do not resolve the issue, consult your plasma cutter’s manual for further troubleshooting.
Inconsistent Cuts
Inconsistent cuts can lead to poor quality work. This issue often arises due to several factors. Here are some key aspects to check:
- Check consumables. Ensure they are in good condition and properly installed.
- Inspect the torch. Make sure there are no obstructions or damage.
- Verify settings. Confirm that the amperage and air pressure are set correctly for the material being cut.
- Clean the workpiece. Dirt, rust, or paint can affect cut quality. Clean the surface before cutting.
Maintaining your plasma cutter and following these steps can help achieve clean and consistent cuts.
Electrical Problems
Electrical problems are common with plasma cutters. These issues can disrupt the cutting process and lead to unexpected downtime. Understanding and fixing these problems quickly can save you both time and money. Below, we discuss two major electrical issues: power supply problems and faulty connections.
Power Supply Issues
A consistent power supply is crucial for a plasma cutter. If the cutter does not turn on, check the power source first. Ensure the outlet is working by plugging in another device. If the outlet works, inspect the power cable for any visible damage. A frayed or broken cable can prevent the cutter from receiving power.
Sometimes, the issue lies within the internal components. Open the cutter and inspect the internal wiring. Look for any loose or disconnected wires. Tighten any loose connections and replace damaged wires. If these steps do not resolve the issue, the problem might be with the power supply unit itself. In this case, consulting a professional is recommended.
Faulty Connections
Loose or faulty connections can also cause electrical problems. First, check the connections at the power source. Ensure all plugs are securely inserted. Next, inspect the connections within the plasma cutter. Look for any signs of wear or corrosion. Clean corroded connections with a wire brush.
Sometimes, connectors can become loose over time. Tighten any loose connectors with a wrench or pliers. Be careful not to overtighten, as this can cause damage. Regular maintenance of connections can prevent many electrical issues. Always keep connectors clean and secure for the best performance.
Airflow Troubles
Many plasma cutter issues stem from poor airflow. This can lead to weak cuts or machine failure. Understanding common airflow troubles helps in quick problem resolution. Below are two main airflow issues and their solutions.
Insufficient Air Pressure
Insufficient air pressure is a common problem. Plasma cutters need a steady air supply. Low pressure can cause weak arcs and poor cuts. Ensure your compressor meets the machine’s air requirements. Check the pressure gauge regularly. Here are some steps to help:
- Inspect the air compressor for leaks.
- Ensure the air filter is clean.
- Verify the pressure settings match the plasma cutter’s needs.
Maintaining proper air pressure ensures efficient cutting and prolongs the machine’s life.
Contaminated Air Supply
A contaminated air supply can lead to many problems. Dust, oil, and moisture can damage the plasma cutter. Use an air dryer or filter to clean the air. Here are some tips for maintaining clean air:
- Install an air filter before the plasma cutter.
- Regularly drain the moisture trap.
- Replace the air filter as needed.
Keeping the air supply clean helps in achieving smooth and precise cuts. It also protects the internal components of the machine.
Torch Problems
Having issues with your plasma cutter torch can be frustrating. Torch problems are common, and they can affect the quality of your cuts. In this guide, we will discuss two main torch issues: worn-out consumables and damaged torch heads. Understanding these problems can help you maintain your plasma cutter and ensure it works efficiently.
Worn Out Consumables
Consumables, such as nozzles and electrodes, wear out over time. They play a crucial role in the cutting process. When they become worn, the torch’s performance decreases. You may notice a drop in cut quality or an increase in dross. Regularly inspect your consumables for signs of wear. Replace them promptly to maintain optimal performance. Using worn consumables can lead to more significant issues.
Damaged Torch Head
The torch head is another essential component. It can get damaged from rough handling or accidental drops. A damaged torch head affects the plasma arc’s stability. This can result in uneven cuts and poor cut quality. Inspect the torch head for cracks or other damage. If you find any, consider replacing the torch head. Proper handling and storage can prevent damage. Always keep the torch head clean and protected.
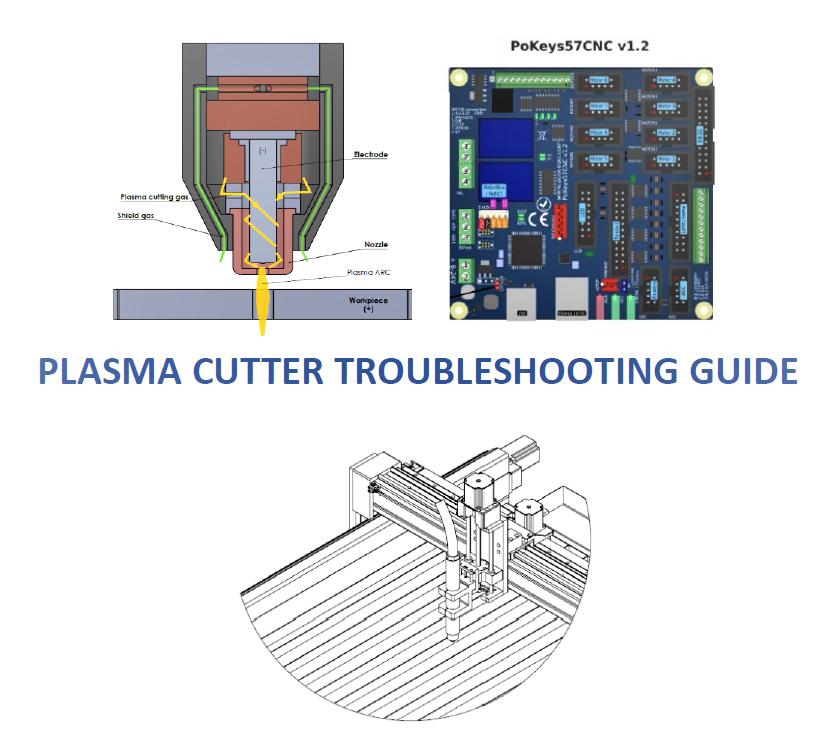
Credit: blog.poscope.com
Cut Quality Issues
Plasma cutting is a precise process. Sometimes, cut quality issues arise. These problems can affect the final product. Understanding and troubleshooting these issues is crucial.
Dross Formation
Dross refers to unwanted material on the cut edge. This can occur due to improper settings. Adjust the cutting speed and amperage to fix this. A fast cut speed can leave dross. Slow down for a cleaner edge. Also, check the torch height. It should be consistent and appropriate for the material thickness.
Uneven Cuts
Uneven cuts can ruin a project. This issue often stems from torch angle. Ensure the torch is perpendicular to the material. Also, inspect the consumables. Worn parts can lead to uneven cuts. Replace them regularly. Lastly, maintain a steady hand or use a guide. This helps achieve consistent cuts.
Maintenance Tips
Maintaining your plasma cutter is crucial for its longevity and performance. Regular maintenance ensures smooth operation and helps avoid unexpected breakdowns. In this section, we’ll cover essential maintenance tips for your plasma cutter.
Regular Inspection
Inspect your plasma cutter regularly to catch potential issues early. Check the torch head for wear and tear. Ensure the nozzle and electrode are in good condition. Look for any signs of damage or excessive wear. Replace worn parts promptly to maintain cutting quality.
Component | Inspection Frequency |
---|---|
Torch Head | Weekly |
Nozzle | Weekly |
Electrode | Weekly |
Cleaning Procedures
Keep your plasma cutter clean to ensure its optimal performance. Dust and debris can affect its efficiency. Follow these cleaning steps:
- Turn off and unplug the plasma cutter.
- Remove the torch and clean the torch head with a soft cloth.
- Use compressed air to blow out dust from the cutter’s interior.
- Wipe down the exterior with a damp cloth.
- Ensure all connections are clean and secure before reassembling.
Regular cleaning prevents dust buildup. It also extends the life of your plasma cutter. Adhering to these maintenance tips will keep your plasma cutter running smoothly and efficiently.
Advanced Troubleshooting
Advanced troubleshooting in plasma cutting involves using specific tools and seeking expert help. This guide will help you with these steps to fix complex problems. Let’s dive into the details.
Diagnostic Tools
Using diagnostic tools can help identify issues in your plasma cutter. These tools are essential for precise troubleshooting:
- Multimeter: Measures electrical voltage, current, and resistance.
- Oscilloscope: Displays signal voltages, useful for checking waveforms.
- Gas Flow Meter: Ensures correct gas flow for optimal cutting.
- Air Pressure Gauge: Monitors air pressure to maintain consistency.
These tools help in diagnosing electrical and mechanical problems efficiently. Regular checks with these tools can prevent major failures. They also help in maintaining the cutter’s performance.
Professional Assistance
Sometimes, problems require expert help. Seeking professional assistance can save time and prevent further damage. Here’s when you should call an expert:
- If the plasma cutter does not turn on, even after basic checks.
- If there are unusual noises or vibrations during operation.
- If the cutter produces inconsistent or poor-quality cuts.
- When the diagnostic tools indicate a problem you cannot fix.
Professionals have the experience and tools to handle complex issues. They can perform advanced diagnostics and repairs. Hiring a professional ensures your plasma cutter operates safely and efficiently.

Credit: www.basicwelding.co.uk
Frequently Asked Questions
Why Won’t My Plasma Cutter Start?
Check power supply, air pressure, and connections. Ensure consumables are installed correctly. These are common issues.
Why Is My Plasma Cutter Cutting Unevenly?
Check torch height and speed settings. Replace worn consumables. Ensure clean and dry air supply.
Why Does My Plasma Cutter Keep Tripping The Breaker?
Ensure proper grounding and correct amperage settings. Check for short circuits or faulty wiring in the machine.
Why Is There Excessive Slag On My Cuts?
Adjust cutting speed and amperage. Ensure proper torch angle. Clean and dry air supply helps.
What Causes My Plasma Cutter To Lose Arc?
Check for worn consumables and proper air pressure. Ensure good electrical connections and clean work surface.
Conclusion
Regular maintenance ensures your plasma cutter works smoothly. Address common issues promptly. Simple fixes often solve performance problems. Remember safety first while troubleshooting. Keep your manual handy for quick reference. Stay patient and persistent. Your plasma cutter is a valuable tool.
With care, it will serve you well. Happy cutting!