Simplify3D Troubleshooting: Ultimate Guide to Fixing Common Issues
3D printing can be complex. Problems often arise, causing frustration.
Simplify3D is a powerful tool for 3D printing. But, like any software, it can face issues. Many users struggle with common problems, such as print quality, software errors, and hardware compatibility. Understanding how to troubleshoot these problems can save time and enhance printing experience.
Whether you’re a beginner or an expert, having a guide to address these issues is invaluable. This blog will walk you through typical Simplify3D problems. You’ll learn practical solutions and tips to keep your 3D printer running smoothly. Let’s dive in and tackle those troubleshooting challenges together.
Software Installation Issues
Installing Simplify3D can sometimes be challenging. Users often face issues during the installation process. These issues can be due to various factors. Let’s explore the common software installation issues and their solutions.
System Requirements
Before installing Simplify3D, ensure your system meets the requirements. This software demands specific hardware and software configurations. Your operating system should be up-to-date. A recent version of Windows, MacOS, or Linux is necessary. Check if your system has enough RAM and disk space. Insufficient resources can lead to installation failures.
Installation Steps
Follow these steps to install Simplify3D smoothly:
- Download the installer from the official website.
- Run the downloaded file.
- Follow the on-screen instructions.
- Choose the installation directory.
- Complete the installation process.
Restart your computer after installation. This ensures all changes take effect.
Common Installation Problems
Users often encounter errors during installation. One common issue is compatibility. Ensure your operating system supports Simplify3D. Another problem is corrupted installer files. Re-download the installer if you face this issue. Insufficient disk space can also cause problems. Free up some space before trying again. Sometimes, antivirus software can block the installation. Temporarily disable it during the process.
By following these guidelines, you can resolve most installation issues. Simplify3D should now run smoothly on your system.
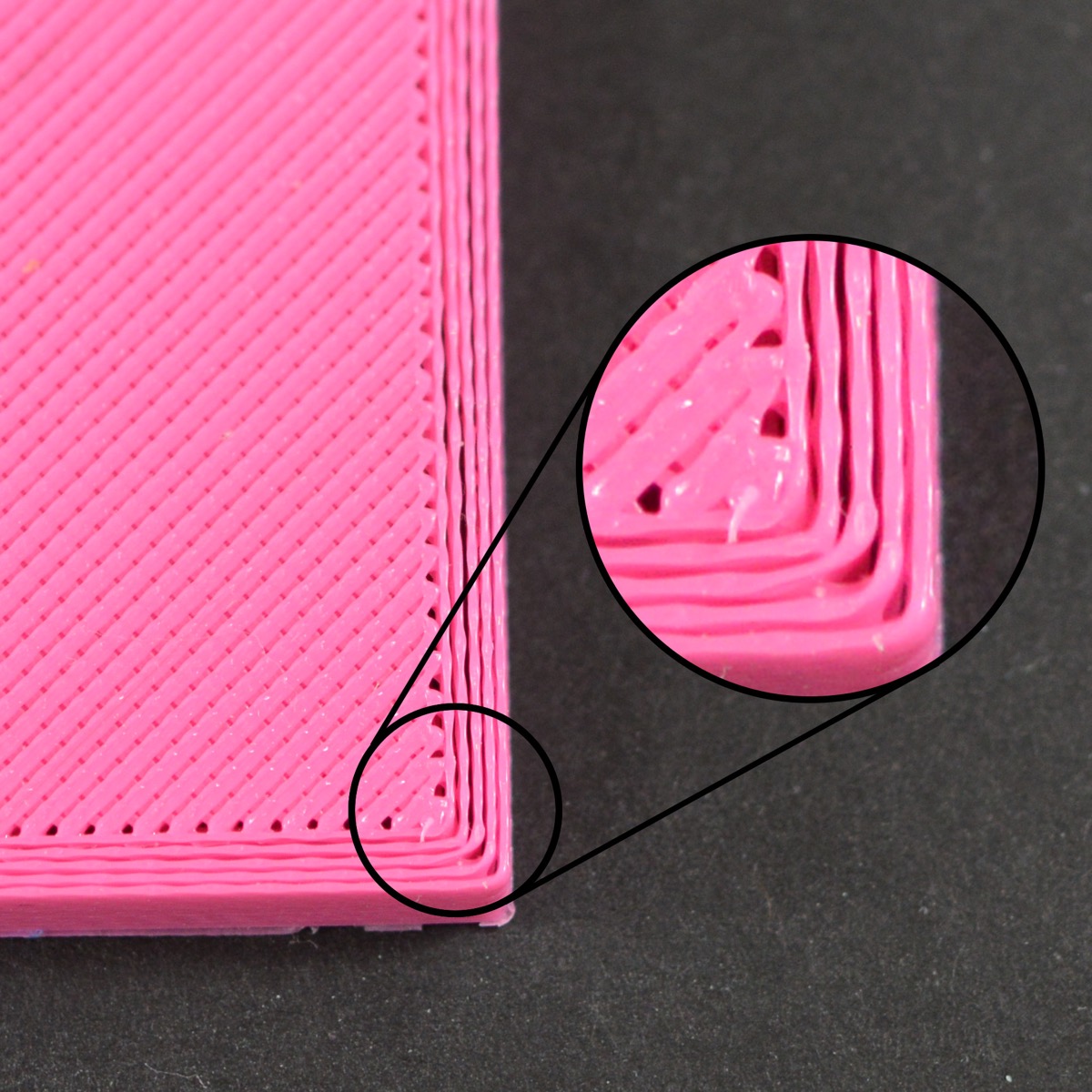
Credit: www.simplify3d.com
Printer Connection Problems
Printer connection problems can be frustrating. They often interrupt your 3D printing process. Simplify3D users may face issues connecting their printer to the software. This section will help you troubleshoot common connection problems. Follow these steps to ensure a smooth setup.
Checking Cables And Ports
First, inspect your cables and ports. Ensure they are secure and undamaged. Use a high-quality USB cable. Avoid using long cables that may cause signal loss. Check the USB port on your computer. Try different ports to rule out any issues. Sometimes, simply switching ports can solve the problem.
Printer Driver Issues
Printer drivers are essential for communication. Ensure you have the correct driver installed. Visit the printer manufacturer’s website for the latest driver. Download and install it on your computer. Restart your computer to apply the changes. Incorrect or outdated drivers can cause connection problems.
Firmware Updates
Firmware is the software running on your printer. Keeping it updated is crucial. Check the printer manufacturer’s website for firmware updates. Follow the instructions to update your printer’s firmware. Updated firmware can fix bugs and improve compatibility. Make sure your printer and computer are connected during the update.
Slicing And G-code Errors
Slicing and G-Code errors can be a major hurdle in 3D printing. These issues can affect print quality or even stop the process. Understanding and fixing these errors is vital for smooth printing. Let’s dive into some common problems and how to solve them.
Incorrect Settings
Incorrect settings can cause various issues in your prints. Ensure the layer height matches your printer’s capabilities. Check the print speed to avoid layer shifting. Set the right temperature for your filament type. Incorrect temperatures can cause under-extrusion or clogging.
File Corruptions
File corruption is another common problem. This can happen when downloading or transferring files. Always verify the integrity of your files before slicing. Use reliable sources for your models to avoid corrupt files. If a file seems off, try re-downloading it.
Software Bugs
Software bugs can also impact your prints. Ensure your Simplify3D software is up to date. Updates often fix known bugs and improve performance. Check the Simplify3D forums for any known issues. Sometimes, a bug might be specific to a certain version.
Troubleshooting these issues can save you time and material. Understanding the root of the problem is the first step to solving it. Happy printing!
Print Quality Issues
Print quality issues are common in 3D printing. Simplify3D users often face challenges that can affect the final product. Understanding and fixing these issues is key to achieving perfect prints. Let’s explore some common print quality problems and their solutions.
Layer Shifting
Layer shifting occurs when the layers of your print are not aligned. This can result in a skewed or distorted model. Several factors can cause layer shifting:
- Loose belts or pulleys
- Overheating stepper motors
- Firmware or software issues
Check and tighten all belts and pulleys. Ensure stepper motors are not overheating. Update your firmware and Simplify3D software to the latest version.
Under-extrusion
Under-extrusion is when the printer does not extrude enough filament. This can lead to weak prints and gaps in layers. Common causes of under-extrusion include:
- Clogged nozzle
- Incorrect extrusion multiplier
- Filament diameter mismatch
Clean the nozzle regularly to prevent clogs. Adjust the extrusion multiplier in Simplify3D settings. Verify the filament diameter matches the printer settings.
Over-extrusion
Over-extrusion happens when too much filament is extruded. This can cause blobs, oozing, and poor surface finish. Factors leading to over-extrusion:
- High extrusion multiplier
- Incorrect filament diameter
- Incorrect nozzle temperature
Lower the extrusion multiplier in Simplify3D settings. Check and match the filament diameter in the settings. Adjust the nozzle temperature to the recommended range.
By addressing these common print quality issues, you can improve your 3D printing results. Regular maintenance and fine-tuning settings in Simplify3D will help achieve high-quality prints.
Filament Problems
Dealing with filament problems can be a common issue for 3D printing enthusiasts. These issues can affect your print quality. Understanding and troubleshooting these problems is crucial. Below, we discuss some of the most common filament problems you may encounter.
Clogged Nozzle
A clogged nozzle can halt your printing process. This usually happens when filament debris blocks the nozzle.
Here are some common signs of a clogged nozzle:
- No filament extruding
- Under-extrusion
- Clicking sounds from the extruder
To fix this, you can try:
- Heating the nozzle and using a needle to clear the blockage
- Using a cleaning filament
- Disassembling the nozzle for thorough cleaning
Filament Jams
Filament jams occur when the filament gets stuck in the extruder. This can be due to tangled filament or an inconsistent feed.
Signs of filament jams include:
- Extruder motor skipping
- Irregular extrusion
- Filament grinding
To resolve filament jams, you can:
- Check for tangled filament on the spool
- Ensure the filament path is clear
- Clean the extruder gears and rollers
Inconsistent Filament Diameter
An inconsistent filament diameter can cause uneven extrusion. This leads to poor print quality.
Indicators of this issue are:
- Visible layer lines
- Gaps in layers
- Over-extrusion or under-extrusion
To address this problem:
- Use high-quality filament
- Measure the filament diameter with a caliper
- Adjust extrusion settings in Simplify3D
By understanding these common filament problems, you can ensure smoother 3D printing experiences. Regular maintenance and using quality materials can also help in preventing these issues.
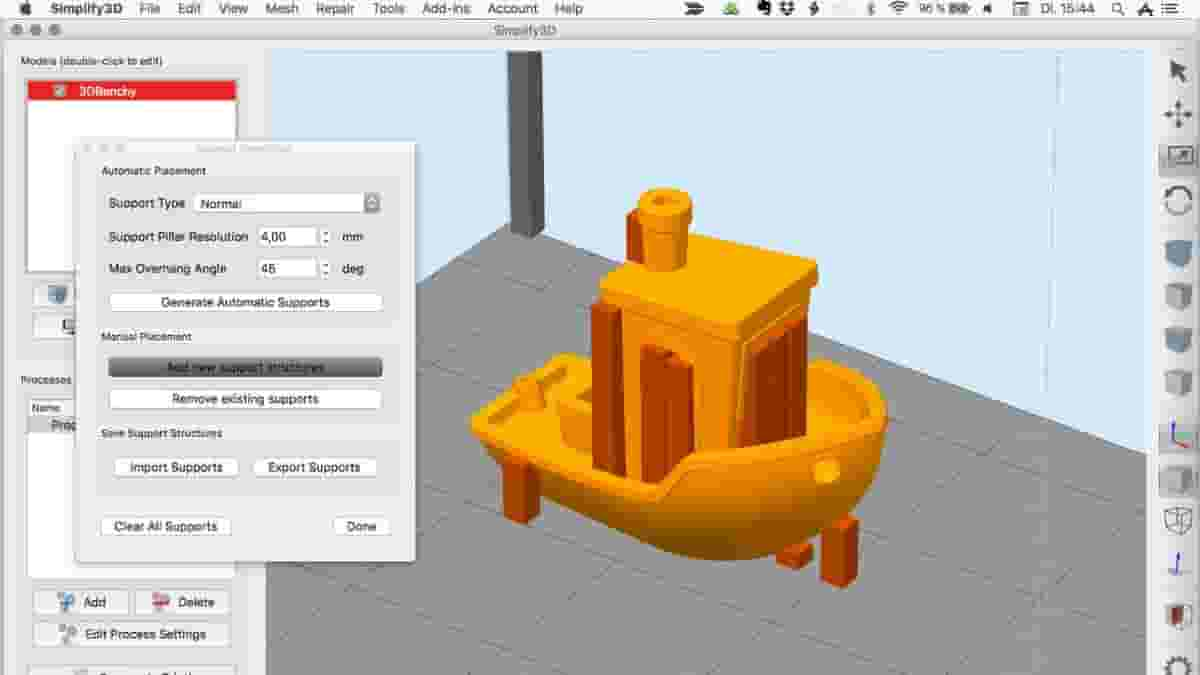
Credit: all3dp.com
Software Crashes And Freezes
Experiencing software crashes and freezes with Simplify3D can be frustrating. These issues often disrupt your workflow and hinder productivity. Understanding the root causes can help you fix these problems efficiently.
System Compatibility
Ensure your computer meets the minimum system requirements for Simplify3D. Below is a list of recommended specifications:
Component | Minimum Requirement |
---|---|
Operating System | Windows 7/8/10, macOS 10.9 or newer |
Processor | 1.7 GHz or faster |
RAM | 4 GB or more |
Graphics | OpenGL 2.0 compatible |
Verify that your operating system and hardware align with these requirements. Incompatible systems often lead to crashes and freezes.
Resource Management
Running multiple applications simultaneously can strain your system resources. Close unnecessary programs to free up CPU and RAM.
- Press
Ctrl + Shift + Esc
to open Task Manager. - Identify and close high-resource applications.
- Ensure Simplify3D has enough resources to operate smoothly.
Managing your system resources effectively can prevent software from freezing or crashing.
Updating Simplify3d
Outdated software can cause performance issues. Regularly check for updates to Simplify3D.
- Open Simplify3D.
- Go to the Help menu.
- Select Check for Updates.
- Follow the prompts to update to the latest version.
Updating ensures you have the latest bug fixes and performance improvements. This can significantly reduce the chances of crashes and freezes.
Advanced Troubleshooting
Advanced troubleshooting in Simplify3D requires a deeper understanding of the software and your 3D printer. It involves detailed analysis and sometimes seeking help from community resources or professionals. This section will guide you through these advanced steps to resolve complex issues.
Log File Analysis
Log files are essential for diagnosing issues. Simplify3D creates log files that record the software’s activity. These logs help identify errors or unusual behavior. To access the log files, go to the Help menu and select “Support” from the dropdown. Then, click on “Generate Support Bundle.” This will create a zip file containing your log files.
Open these files with a text editor. Look for error messages or warnings. These entries can provide clues about the problem. If you cannot understand the log entries, search the Simplify3D forums for similar issues. Many users share their log files and solutions.
Community And Support Resources
The Simplify3D community is a valuable resource. Join forums and social media groups. Ask questions and share your experiences. Many experienced users can offer advice and solutions. The official Simplify3D forums are a good place to start. You can find them on the Simplify3D website under the “Support” section.
Another resource is the Simplify3D Knowledge Base. It contains articles on common issues and their fixes. Search the Knowledge Base for your specific problem. Often, you will find detailed guides and tips.
Professional Help
Sometimes, issues are too complex to solve on your own. In such cases, consider seeking professional help. Simplify3D offers paid support options. You can contact their support team directly through their website. Provide them with your log files and a detailed description of the issue.
Another option is to consult with a local 3D printing expert. Many communities have makerspaces or 3D printing services. These professionals can offer hands-on help and advice. They can also provide maintenance services for your 3D printer.

Credit: www.3printr.com
Frequently Asked Questions
Why Is My Print Not Sticking To The Bed?
Your print might not be sticking due to bed leveling issues or incorrect temperature settings.
How Can I Fix Layer Shifting Issues?
Layer shifting can be fixed by tightening belts and ensuring the frame is stable.
What Causes Stringing Between Prints?
Stringing is often caused by incorrect retraction settings or high printing temperatures.
Why Is My Extruder Clicking?
A clicking extruder may be due to a clogged nozzle or filament feeding issues.
How Do I Resolve Warping In Prints?
Warping can be resolved by using a heated bed and proper bed adhesion techniques.
Conclusion
Simplify3D troubleshooting can seem daunting, but it doesn’t have to be. With patience, you can solve most issues. Always check your settings first. Make small adjustments one at a time. This prevents further complications. Keep your software updated for the best performance.
Community forums can also offer helpful advice. Remember, practice makes perfect. Soon, you’ll handle problems confidently. Simplify3D is a powerful tool with great potential. Happy printing!