Tig Welding Troubleshooting: Expert Tips for Perfect Welds
TIG welding is a precise and skilled technique. It creates clean, strong welds.
But, like any process, it can have issues. Common problems in TIG welding include contamination, poor arc starting, and inconsistent welds. Understanding these problems is crucial for effective welding. This blog will help you identify and fix common TIG welding issues.
With clear explanations, you’ll learn how to improve your welding skills. Whether you’re a beginner or experienced welder, this guide will offer valuable insights. Let’s dive into the world of TIG welding troubleshooting and make your welds better and stronger.
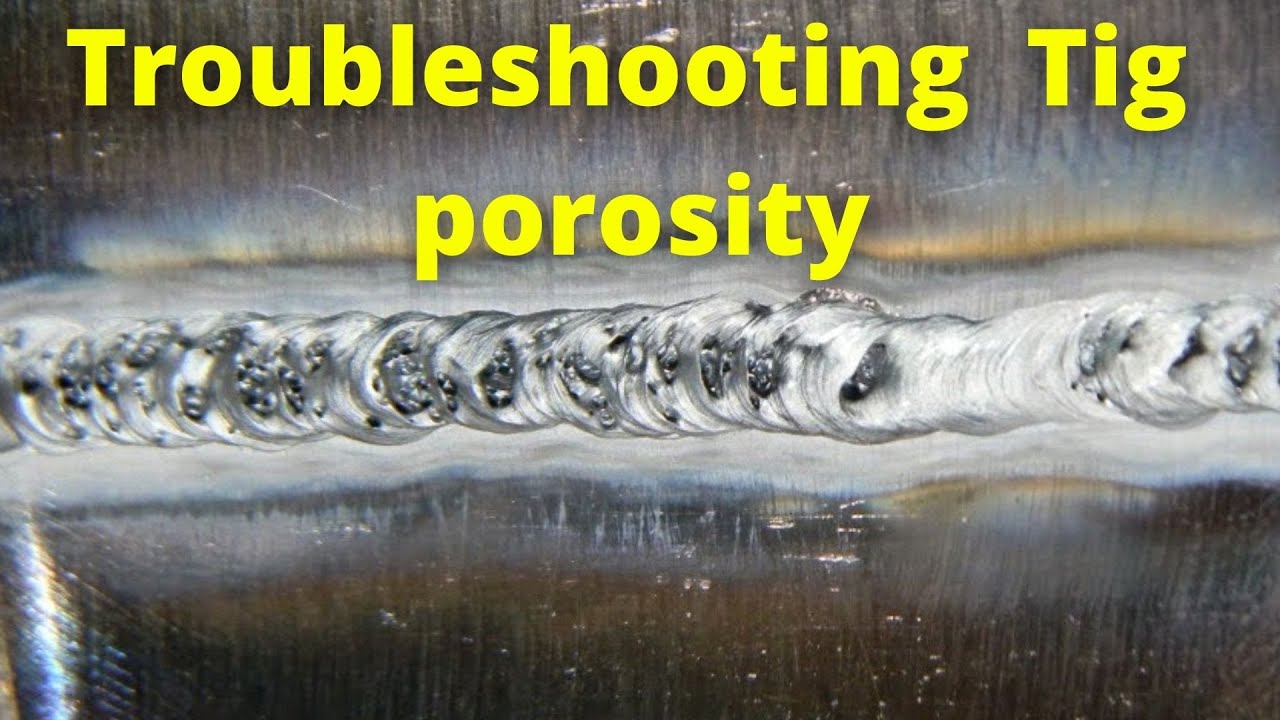
Credit: www.youtube.com
Common Tig Welding Issues
TIG welding, also known as Gas Tungsten Arc Welding (GTAW), is a popular method for producing high-quality welds. However, even experienced welders face common issues that can affect the quality and consistency of their work. Understanding these common TIG welding issues can help you troubleshoot and improve your welding skills.
Porosity Problems
Porosity in welds means small holes or voids within the weld bead. This issue often arises due to contamination. Dirty base metals, poor gas coverage, or improper filler materials can cause porosity. Always clean your workpiece and ensure proper gas flow to prevent porosity. Using the correct filler rod also helps in reducing this problem.
Inconsistent Arc
An inconsistent arc can lead to poor weld quality. Common causes include dirty tungsten, incorrect settings, or unstable hand movements. Ensure your tungsten is clean and properly ground. Adjust your machine settings to match your material and thickness. Practice steady hand movements for a consistent arc.
Preventing Contamination
Tig welding can be a precise and rewarding process. But contamination can spoil your work. Preventing contamination is vital for successful Tig welding. This section will cover essential tips to keep your welds clean and strong.
Cleanliness Tips
Ensure all materials are clean before welding. Use a dedicated wire brush for stainless steel. Use a different brush for aluminum. Never use a brush that has touched steel on aluminum. Wipe down materials with acetone. This removes oils and dirt.
Keep your gloves, torch, and workspace clean. Dirty gloves transfer contaminants to your work. A clean torch ensures smooth gas flow. A tidy workspace reduces the risk of dirt getting into your welds.
Proper Gas Flow
Argon gas shields the weld from contamination. Ensure your gas flow is set correctly. Use a flow rate of 15-20 cubic feet per hour (cfh). Check for leaks in your gas lines. Leaks can reduce gas flow and introduce contaminants.
Hold the torch at the right angle. Keep it around 15 degrees from vertical. This helps the gas shield the weld properly. Avoid drafts and wind. They can disrupt the gas flow. Use a welding screen to block wind if necessary.
Electrode Selection
Electrode selection plays a crucial role in successful TIG welding. The right choice impacts weld quality, stability, and ease of use. This section will guide you through choosing the right type of electrode and maintaining it for optimal performance.
Choosing The Right Type
Selecting the correct electrode depends on the material you are welding. Common options include tungsten electrodes. Pure tungsten works well for aluminum and magnesium. Thoriated tungsten suits stainless steel and carbon steel. Lanthanated and ceriated electrodes offer stable arcs and long lifespans. Consider the electrode diameter too. Thicker electrodes handle higher currents. Thinner ones work well for delicate tasks.
Electrode Maintenance
Regular maintenance ensures your electrode performs well. Always keep the tip clean. Contaminants can ruin the weld. Use a dedicated grinding wheel for tungsten. A bench grinder also works. Ensure it is clean and free from other materials. Grind the tip to a point for DC welding. For AC welding, create a rounded tip. Inspect the electrode for wear. Replace it if you notice cracks or other damage. Proper storage is important. Keep electrodes dry and away from contaminants.
Managing Heat Input
Managing heat input is crucial in TIG welding. Proper heat management ensures strong welds and prevents defects. It also helps maintain the integrity of the materials being welded. Let’s dive into some effective techniques for managing heat input in TIG welding.
Heat Control Techniques
Controlling heat is vital in TIG welding. One effective method is using a foot pedal. The foot pedal allows precise control over the heat. This helps in reducing overheating. Another technique is using a pulser. A pulser helps control the heat by alternating between high and low current. This method is excellent for thin materials. Also, adjusting the arc length can help. A shorter arc length reduces heat input, while a longer arc increases it.
Avoiding Warping
Warping is a common issue in TIG welding. Proper heat management can prevent warping. One way to avoid warping is by using heat sinks. Heat sinks absorb excess heat, reducing the risk of warping. Another method is to use tack welds. Tack welds hold parts in place and distribute heat more evenly. Additionally, controlling the welding speed is essential. Welding too fast or too slow can cause warping. Maintain a steady speed to ensure uniform heat distribution.
Shielding Gas Tips
Troubleshooting TIG welding issues can be challenging. The shielding gas plays a crucial role in achieving a clean, strong weld. Understanding the proper use and adjustments of shielding gas can help you avoid common problems.
Gas Types And Uses
Different gases serve different purposes in TIG welding. Argon is the most common choice. It is suitable for welding almost all metals. Helium is another option. It is often used for thicker materials. A mix of argon and helium can improve weld penetration.
Flow Rate Adjustments
The flow rate of the shielding gas is essential. Too low, and the weld will be contaminated. Too high, and you waste gas. A flow rate of 15-20 cubic feet per hour (CFH) is a good starting point. Adjust based on your welding environment and material.
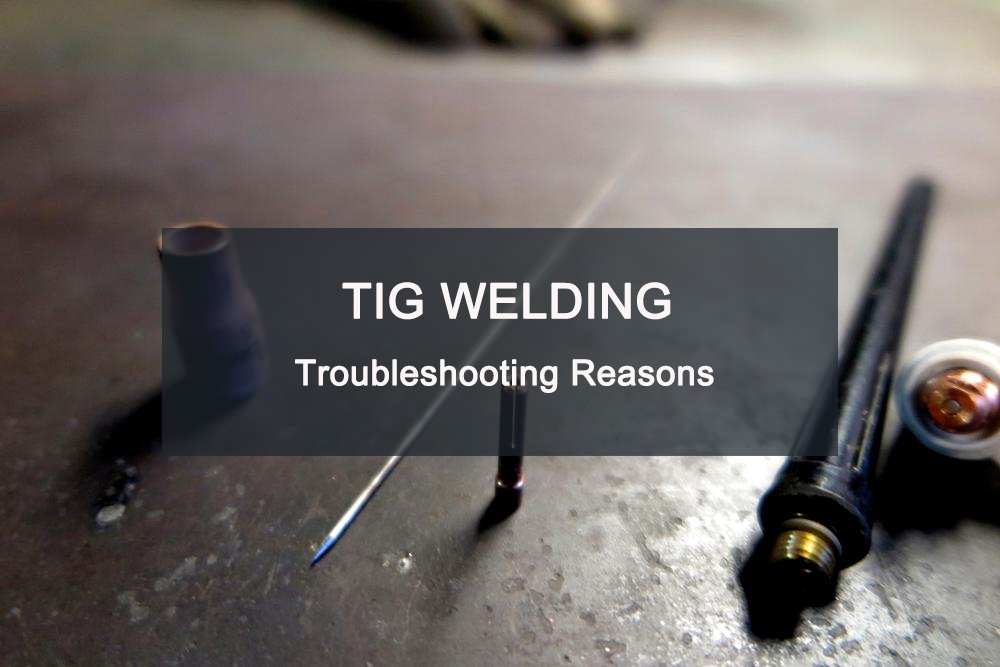
Credit: www.perfectwelders.com
Dealing With Cracks
TIG welding is a precise and clean welding method. Yet, dealing with cracks can be frustrating. Cracks weaken the weld and can cause failure. Addressing this issue is vital for a strong weld.
Identifying Causes
Cracks in TIG welding often stem from a few common issues. One primary cause is high stress during cooling. Uneven cooling can result in cracks. Another cause is contamination. Dirt or oil on the metal can lead to weak spots. Incorrect filler material can also cause problems. Using the wrong type or amount can weaken the weld.
Repair Methods
To fix cracks, start by cleaning the area. Remove any dirt, oil, or debris. Next, grind out the crack. This ensures you remove all weak material. Then, use a suitable filler rod. Match it to the base metal for best results. Apply heat evenly. This helps prevent new cracks.
Finally, inspect the weld. Look for any signs of new cracks or weak spots. If found, repeat the process. Proper TIG welding techniques can prevent cracks and ensure strong, durable welds.
Improving Weld Appearance
Improving the appearance of your TIG welds can be challenging. A well-executed weld not only looks good but also ensures the strength and durability of the joint. Here are some tips to help you achieve smooth beads and avoid undercuts in your welds.
Achieving Smooth Beads
Smooth beads are essential for a professional-looking weld. Here are some tips to help you achieve them:
- Clean the Metal: Ensure the metal is free of dirt, oil, and rust.
- Maintain a Steady Hand: Keep your hand steady to avoid waviness in the bead.
- Control the Heat: Use the appropriate heat setting for the thickness of the metal.
- Use the Right Filler Rod: Choose a filler rod that matches the base metal.
Practice these techniques to create smooth, consistent beads in your welds.
Avoiding Undercuts
Undercuts can weaken the weld and make it look unprofessional. To avoid undercuts:
- Proper Heat Control: Avoid excessive heat that can cause the metal to melt too much.
- Correct Torch Angle: Maintain a 15-20 degree angle between the torch and the workpiece.
- Consistent Speed: Move the torch at a consistent speed to ensure even distribution of heat.
- Fill Craters: Add filler material to any craters that form to prevent undercuts.
Following these tips will help you avoid undercuts and improve the overall appearance of your welds.

Credit: www.reddit.com
Equipment Maintenance
Maintaining your TIG welding equipment is essential for achieving quality welds. Regular maintenance helps prevent unexpected breakdowns and ensures consistent performance. This section covers important aspects of equipment maintenance, including regular checks and replacing worn parts.
Regular Checks
Performing regular checks on your TIG welding equipment can significantly extend its lifespan. Here are some key areas to focus on:
- Cables and Hoses: Inspect for cracks, wear, or damage. Replace if needed.
- Connectors: Ensure tight and clean connections. Loose connections can cause poor performance.
- Gas Supply: Check gas flow and pressure. Ensure there are no leaks in the system.
Keeping these components in good condition prevents common welding issues and ensures safety during operation.
Replacing Worn Parts
Over time, some parts of your TIG welding equipment will wear out and need replacement. Key components to monitor include:
Part | Signs of Wear |
---|---|
Tungsten Electrode | Burnt tips, reduced arc stability |
Nozzle | Cracks, irregular gas flow |
Collet Body | Deformation, poor electrode grip |
Regularly replacing these worn parts ensures your equipment functions properly and produces high-quality welds. Always use parts recommended by the manufacturer to avoid compatibility issues.
Expert Techniques
TIG welding is a precise art. Expert techniques can make a big difference. Understanding advanced methods helps welders achieve clean, strong welds. This section will explore advanced welding methods and tips for precision. Both are crucial for troubleshooting TIG welding issues.
Advanced Welding Methods
Mastering advanced methods requires practice. One key method is pulse welding. Pulse welding controls heat, reducing warping and burn-through. It’s perfect for thin metals. Another method is back-purging. Back-purging protects the weld’s backside from oxidation. This is important for stainless steel and titanium.
Using the right filler rod is crucial. Match the rod material to the base metal. Clean the rod before use. A clean rod ensures a strong bond. Also, consider using a gas lens. A gas lens provides better gas coverage. This results in a smoother weld bead.
Tips For Precision
Precision in TIG welding starts with preparation. Clean the base metal thoroughly. Remove any dirt, oil, or rust. This ensures a strong weld. Next, set up your equipment correctly. Check the gas flow rate. Too much or too little gas affects the weld quality.
Maintain a steady hand. Use both hands if needed. Rest your hand on a support to reduce shaking. This helps in making smooth, consistent welds. Also, control the heat input. High heat can cause warping. Use the foot pedal to adjust heat as you weld.
Lastly, practice makes perfect. Weld scrap pieces to improve your skills. Experiment with different settings. Find what works best for you. Keep a log of your settings and results. This helps in troubleshooting future issues.
Frequently Asked Questions
Why Is My Tig Welder Not Starting?
Your TIG welder may not start due to a poor ground connection, improper torch setup, or a faulty pedal.
Why Is My Tungsten Electrode Burning Up?
The tungsten electrode burns up because of excessive amperage, incorrect gas flow, or contamination.
Why Is My Weld Puddle Not Forming?
A weld puddle may not form if there’s insufficient amperage, improper torch angle, or a dirty workpiece.
Why Am I Getting Porosity In My Welds?
Porosity in welds can be caused by contaminated gas, poor shielding, or dirty base materials.
Why Is My Tig Weld Bead Too Narrow?
A narrow weld bead might result from low amperage, fast travel speed, or incorrect filler rod size.
Conclusion
Troubleshooting TIG welding issues can be challenging but rewarding. Identifying problems early saves time. Practice makes perfect. Regular maintenance of equipment is crucial. Always check for proper settings and clean surfaces. Patience and attention to detail are key. With these tips, you can improve your welding skills.
Stay safe and keep learning. Happy welding!