Vevor Slush Machine Troubleshooting: Expert Tips and Solutions
Slush machines are fun and useful, especially for hot days. But, like any machine, Vevor Slush Machines can have issues.
Understanding common problems can save you time and frustration. Whether you own a Vevor Slush Machine for business or home, knowing how to troubleshoot it is essential. This guide will help you identify and fix common problems. From minor glitches to more serious malfunctions, you’ll find practical solutions here.
Keep reading to ensure your slush machine runs smoothly and efficiently.
Common Issues
Understanding common issues with your Vevor Slush Machine can save time and frustration. Below, we address frequent problems and provide simple solutions.
Machine Not Turning On
If your Vevor Slush Machine is not turning on, follow these steps:
- Check the Power Cord: Ensure the power cord is securely plugged in.
- Inspect the Power Outlet: Make sure the outlet is working by testing another device.
- Examine the Fuse: Look for a blown fuse and replace it if necessary.
- Check the Switch: Confirm the power switch is in the “on” position.
If the machine still doesn’t turn on, contact customer support for further assistance.
Slush Not Freezing
Is your slush not freezing? Try these tips:
- Correct Mixture: Ensure you have the right water to syrup ratio. Too much water can prevent freezing.
- Temperature Setting: Verify the machine is set to the correct freezing temperature.
- Clean the Condenser: Dust and dirt on the condenser can hinder cooling. Clean it regularly.
- Adequate Ventilation: Make sure there’s enough space around the machine for proper air circulation.
- Check for Blockages: Ensure there are no blockages in the freezing cylinder.
If the problem persists, you might need professional maintenance.
Table Of Quick Fixes
Issue | Possible Solution |
---|---|
Machine Not Turning On | Check power cord, outlet, fuse, and switch |
Slush Not Freezing | Check mixture, temperature, condenser, ventilation, and blockages |
These simple checks and solutions can resolve most common issues with your Vevor Slush Machine.
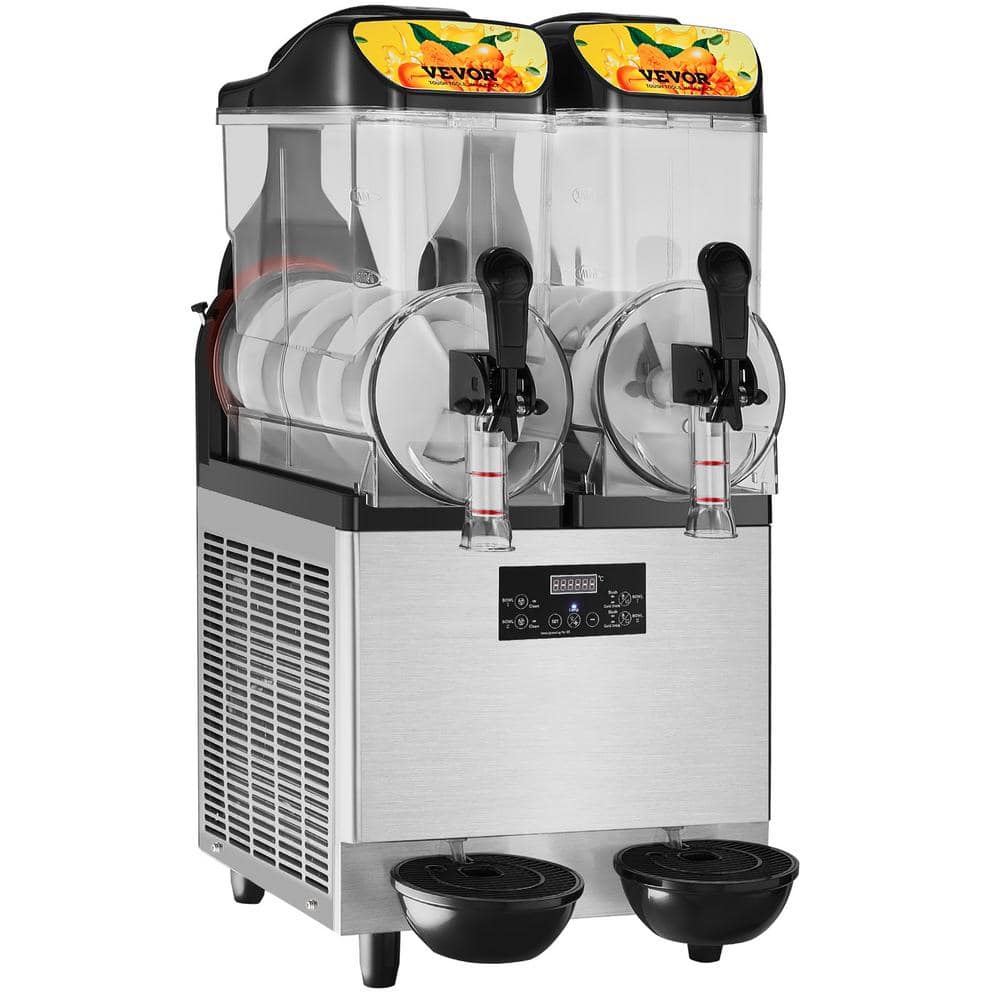
Credit: www.homedepot.com
Electrical Problems
Encountering electrical problems with your Vevor Slush Machine can be frustrating. These issues often stem from simple fixes. Below, we will guide you through checking the power supply and inspecting the fuse.
Power Supply Check
First, ensure that the power supply to your slush machine is intact. Use these steps:
- Check if the power cord is plugged in securely.
- Examine the outlet for power. Plug another device to test.
- Verify that the machine’s power switch is turned on.
If the machine still does not power up, you may have a blown fuse or another internal issue.
Fuse Inspection
A blown fuse can stop your slush machine from operating. Follow these steps to inspect the fuse:
- Unplug the machine from the power source.
- Locate the fuse compartment (usually near the power cord).
- Open the compartment and remove the fuse.
- Check if the fuse wire is broken or burnt.
If the fuse is damaged, replace it with a new one of the same rating. Ensure it is properly seated in the compartment before closing it.
After replacing the fuse, plug the machine back in and turn it on. If the problem persists, further internal components may need inspection.
Cooling System Troubles
Experiencing issues with your Vevor slush machine? The cooling system might be the problem. It is crucial to understand common issues related to the cooling system. This helps in ensuring your machine works optimally. Let’s dive into some common areas of concern.
Refrigerant Levels
Low refrigerant levels can hinder your machine’s cooling efficiency. This can result in slush that is not properly frozen. Check the refrigerant levels regularly. If you find them low, it might be time for a refill.
Signs of low refrigerant levels:
- Longer freezing times
- Inconsistent slush texture
- Warm air from the vents
Compressor Function
The compressor plays a vital role in the cooling process. A malfunctioning compressor can cause significant cooling issues. If the compressor is not functioning properly, your machine will not freeze the slush mix.
Symptoms of compressor problems:
- Strange noises from the machine
- Frequent cycling on and off
- No cooling at all
If you notice any of these issues, it might be time to inspect the compressor. In some cases, a simple repair might suffice. In others, you might need a replacement.
Maintenance Tips
Keeping your Vevor Slush Machine in top condition is essential. Regular maintenance not only ensures smooth operation but also extends the machine’s lifespan. Here are some important maintenance tips to keep your machine running efficiently.
Regular Cleaning
Regular cleaning is crucial for your Vevor Slush Machine. After each use, wash all removable parts with warm, soapy water. Avoid using abrasive cleaners as they can damage the surfaces. Ensure all parts are thoroughly dried before reassembling to prevent mold or mildew.
Lubrication Points
Lubrication keeps the machine’s moving parts functioning smoothly. Identify the key lubrication points in your Vevor Slush Machine. Apply food-safe lubricant to the specified areas. This reduces friction and prevents wear and tear. Regular lubrication ensures the machine operates quietly and efficiently.
User Errors
Operating a Vevor slush machine can sometimes be challenging. User errors often lead to issues. Understanding these common mistakes can help you avoid them. Let’s dive into two main user errors: improper mixture ratios and incorrect settings.
Improper Mixture Ratios
Using the wrong mixture ratio can cause problems. The slush mixture must be precise. Too much water can make the slush too thin. It won’t freeze properly. Too much syrup can make the slush too thick. This can strain the machine.
Always follow the manufacturer’s guidelines. Measure ingredients carefully. Consistency is key. The right balance ensures smooth operation. It also keeps the slush at the perfect texture.
Incorrect Settings
Setting the machine incorrectly can lead to issues. Each machine has specific settings for different slush types. Using the wrong setting can affect freezing. The slush may become too icy or too liquid.
Check the manual for the correct settings. Adjust according to the type of slush you want. Regularly review settings to ensure accuracy. This simple step can prevent many problems.
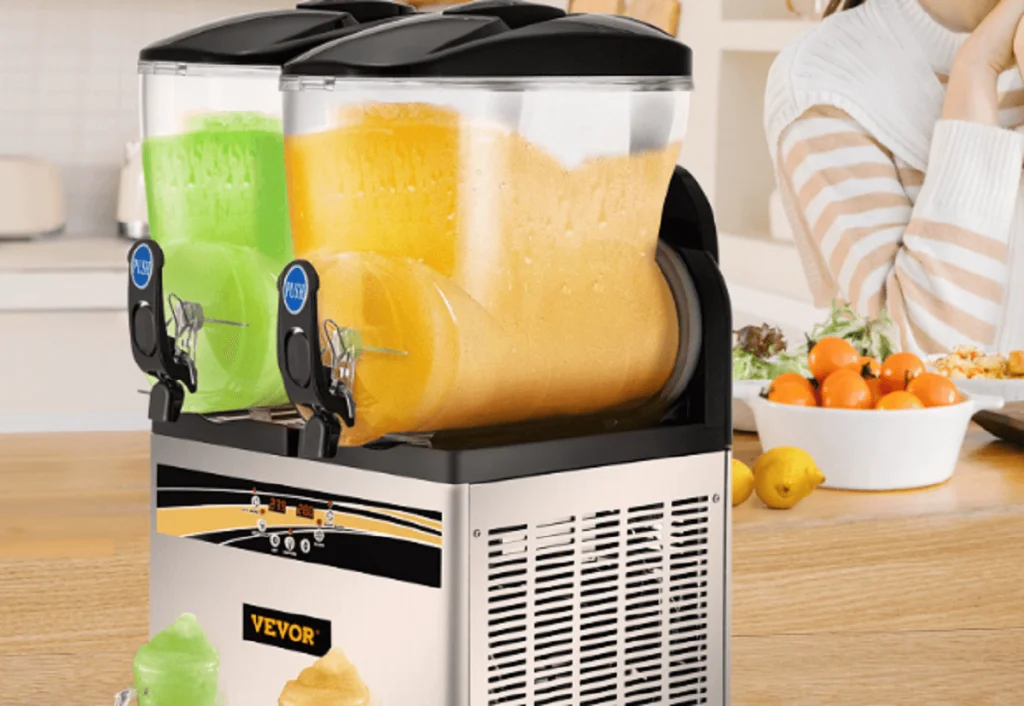
Credit: www.vevor.com
Advanced Repairs
Advanced repairs on a Vevor Slush Machine can be challenging. Sometimes, basic troubleshooting doesn’t solve the issue. In these cases, replacing parts or seeking professional assistance is essential. Below, we will delve into these steps.
Replacing Parts
Replacing parts is a common solution for many issues with a Vevor Slush Machine. Here is a simple guide to help you:
- Identify the faulty part: Check the user manual to identify the broken part.
- Source the replacement: Purchase the correct replacement part from a reliable supplier.
- Follow the manual: Use the user manual for step-by-step replacement instructions.
Always ensure the machine is unplugged before starting any repairs. This prevents electric shocks and other hazards.
Professional Assistance
If replacing parts does not fix the issue, seeking professional assistance is advisable. Professionals have the tools and expertise to diagnose and repair complex issues.
Here’s how to find a reliable technician:
- Check reviews: Look for technicians with good customer reviews.
- Ask for certifications: Ensure the technician is certified to work on Vevor Slush Machines.
- Get a quote: Ask for a detailed quote before agreeing to any repairs.
Professional assistance ensures your slush machine is repaired correctly and safely. This can save you time and prevent further damage.
Preventative Measures
To keep your Vevor Slush Machine running smoothly, follow these preventative measures. Simple steps can save you time and money. Proper care is essential for longevity and performance. Let’s explore some key practices.
Routine Inspections
Routine inspections are crucial for your slush machine’s health. Check all parts regularly. Look for signs of wear and tear. Inspect the cooling system and ensure it’s free from blockages. Verify the mixing motor runs smoothly without strange noises.
Create a checklist for a thorough inspection:
- Check the cooling fans.
- Inspect the mixing blades.
- Ensure the drip tray is clean.
- Examine all seals for leaks.
Proper Storage
Proper storage of your Vevor Slush Machine is vital during off-seasons. Always clean the machine thoroughly before storage. Remove all slush mixture and sanitize the tanks.
Here are some tips for storing your machine:
- Dry all parts completely to avoid mold.
- Store in a cool, dry place.
- Cover the machine to protect it from dust.
- Avoid stacking heavy items on top of the machine.
By following these preventative measures, you can ensure your Vevor Slush Machine stays in top condition. Regular care extends the life of your equipment and ensures it works efficiently when you need it.
Useful Resources
Having a Vevor Slush Machine is great for making delicious slushies. Sometimes, you may face issues with the machine. Don’t worry. There are useful resources to help you troubleshoot. Below, you will find some important resources to get your machine running smoothly again.
Manuals And Guides
The first place to look is the Vevor Slush Machine manual. It has detailed instructions on setup and troubleshooting. Keep the manual handy. It can guide you through common problems. If you lost your manual, you can download it from the Vevor website. Search for your model to find the correct manual. Reading through the guide can save you time and effort.
Customer Support
If the manual does not solve your issue, contact customer support. Vevor has a dedicated team to help with your slush machine problems. You can reach them by phone or email. They are quick to respond and very helpful. Have your machine’s model number ready. This will help them assist you better. Customer support can provide solutions or direct you to a service center if needed.
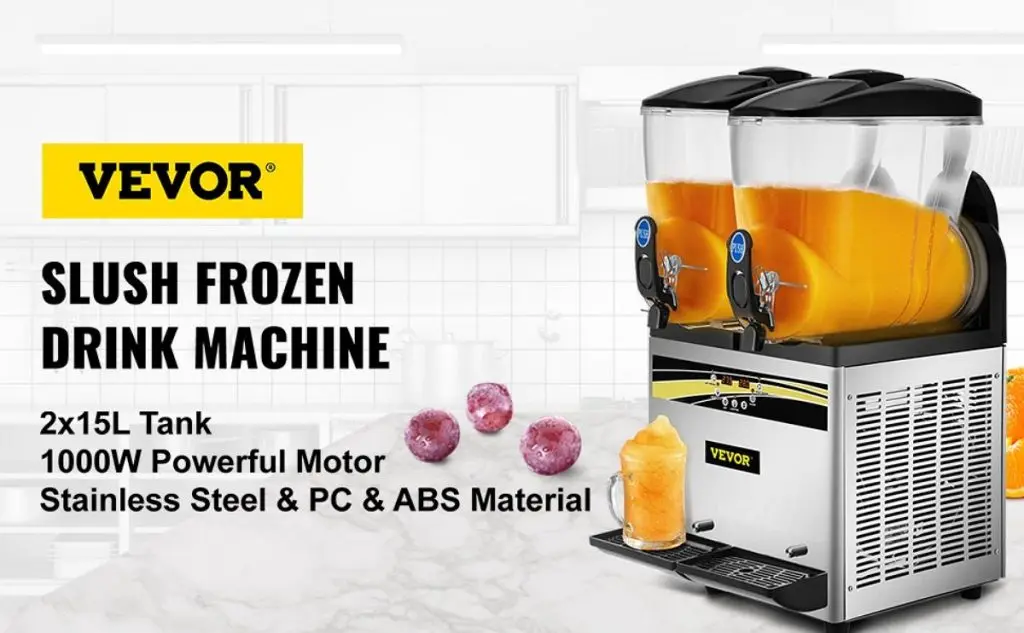
Credit: www.vevor.com
Frequently Asked Questions
Why Is My Vevor Slush Machine Not Freezing?
Check the thermostat setting. Ensure the machine has enough ventilation and is not overloaded.
How Do I Clean My Vevor Slush Machine?
Turn off and unplug the machine. Disassemble parts. Wash with warm, soapy water. Rinse and dry.
What Should I Do If My Slush Machine Is Leaking?
Inspect seals and gaskets. Tighten any loose parts. Replace damaged seals if necessary.
Why Is My Vevor Slush Machine Making Noise?
The machine might be uneven. Place it on a flat surface. Check for loose parts and tighten them.
How Often Should I Service My Slush Machine?
Service your slush machine every 3-6 months. Regular maintenance ensures it runs smoothly.
Conclusion
Troubleshooting your Vevor slush machine can be simple with these steps. Regular maintenance ensures your machine runs smoothly. Clean parts often to avoid issues. Check connections and seals regularly. Always use the recommended ingredients. Follow the user manual closely. With these tips, your slush machine will last longer.
Enjoy delicious slushies without hassle. Stay cool and refreshed!