Walk in Cooler Troubleshooting Chart: Solve Issues Fast
A walk-in cooler is the backbone of many businesses, from restaurants to grocery stores. When it stops working right, you can feel the stress building.
After all, your inventory, your schedule, and even your bottom line depend on it running smoothly. That’s where a troubleshooting chart becomes your best ally. Imagine having a clear, step-by-step guide to pinpoint the issue quickly and get things back on track.
No more guessing, no more wasted time. This blog will walk you through exactly how to use a troubleshooting chart to diagnose common walk-in cooler problems and even prevent them in the future. Stay with me—you’re about to save yourself a lot of headaches and money.
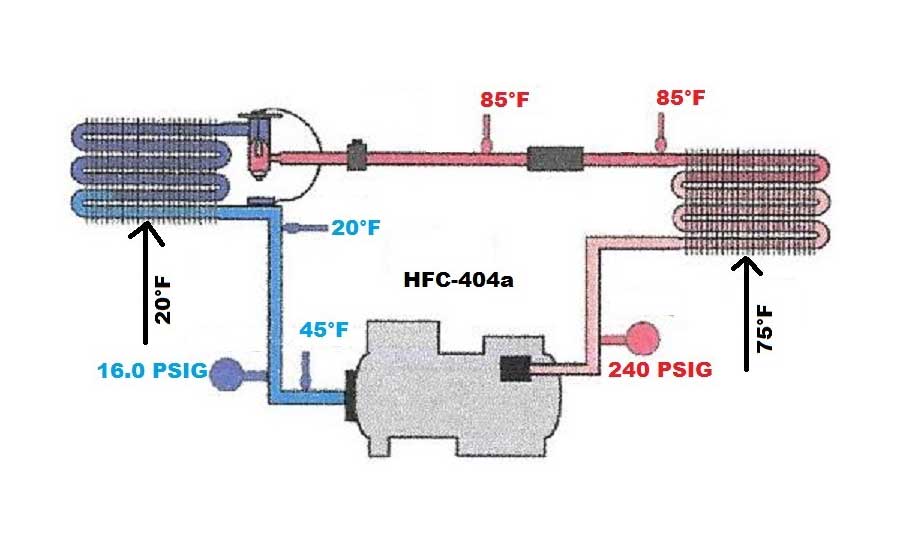
Credit: www.achrnews.com
Common Cooler Problems
Walk-in coolers are essential for keeping perishables fresh and ensuring smooth business operations. But what happens when your cooler isn’t working as it should? Knowing the most common cooler problems can save you time, money, and stress. Let’s break down these frequent issues and how you can address them.
1. Temperature Fluctuations
If your walk-in cooler isn’t maintaining the correct temperature, it could be due to a few reasons. Check the thermostat setting first—sometimes it’s as simple as someone accidentally adjusting it. If the thermostat is fine, inspect the door seals for gaps or tears where cold air might be escaping.
Another culprit might be blocked airflow. Shelves packed too tightly can restrict air circulation, causing uneven cooling. Always leave space between items to allow air to flow freely.
2. Ice Build-up
Ice forming on walls, floors, or the evaporator coil is a clear sign something’s wrong. It’s often caused by warm air sneaking into the cooler, usually from a damaged door gasket or a door left open too long. Make it a habit to check the door seals regularly and remind your staff to close the door quickly after use.
If the problem persists, inspect the defrost system. A faulty defrost timer or heater can lead to excessive ice buildup. Addressing this promptly can prevent further damage to your cooler.
3. Strange Noises
Unusual sounds like banging, squealing, or rattling should never be ignored. They often point to mechanical issues, such as a failing fan motor or compressor. A noisy fan might simply need cleaning to remove debris clogging the blades.
If the compressor is making odd noises, it could be struggling to maintain pressure. Schedule maintenance as soon as possible to avoid a complete breakdown.
4. High Energy Bills
Has your electricity bill spiked recently? Your walk-in cooler might be the reason. A cooler that’s overworking due to poor insulation, malfunctioning components, or frequent door openings consumes more energy than necessary.
Inspect the cooler’s insulation and seals, and monitor how often the door is opened and closed throughout the day. You can also clean the condenser coils, as dirt and grime force the system to work harder.
5. Water Leaks
Water pooling inside or outside the cooler is another common issue. This could be due to a clogged drain line, which prevents condensation from draining properly. Clear out the line with a pipe cleaner or call a technician if you’re unsure how to do it safely.
Leaking water can also result from excessive condensation caused by warm air entering the cooler. Again, check the door gaskets and ensure the door isn’t left open longer than necessary.
Have you faced any of these problems before? How did you resolve them? Understanding these common cooler issues can empower you to act quickly and keep your business running smoothly.
Temperature Issues
Temperature problems in walk-in coolers can affect food safety and energy use. Identifying and fixing these issues quickly ensures your cooler runs efficiently. Below are common temperature-related problems and troubleshooting tips.
Cooler Not Cooling Properly
If your cooler isn’t cooling, check the thermostat settings first. Verify the set temperature matches the recommended range for your items. Dirty condenser coils can also cause cooling failure. Clean them to improve airflow and efficiency. Inspect the door seals for gaps or damage. Warm air can enter if seals aren’t tight. Ensure the evaporator fan is working. A broken fan disrupts air circulation inside the cooler.
Overcooling Or Freezing
If your cooler overcools, the thermostat may be faulty. Replace it if settings don’t respond. Check the temperature probe placement. A misplaced probe may read incorrect temperatures. Inspect the refrigerant levels. Low refrigerant can cause freezing due to uneven cooling. Ensure the defrost timer is functional. Freezing may occur if defrost cycles aren’t happening.
Uneven Temperature Distribution
Electrical Failures
Electrical failures are one of the most common issues with walk-in coolers. They can disrupt your system’s functionality, spoil your inventory, and lead to unexpected repair bills. Knowing how to identify and address these issues is key to keeping your cooler running smoothly.
Power Supply Problems
Start with the basics: check the power supply. Is the cooler plugged in securely? A loose plug or damaged outlet can cut off power and stop your cooler in its tracks.
Examine the power cord for wear and tear. A frayed cord can cause intermittent power issues or even pose a safety hazard. Replacing a damaged cord is simple and can save you from larger electrical problems.
Is the main power switch turned on? It sounds obvious, but you’d be surprised how often this gets overlooked. Always double-check before diving into more complex troubleshooting.
Blown Fuses Or Tripped Breakers
If your cooler suddenly stops working, a blown fuse or tripped breaker could be the culprit. Open your electrical panel and see if the breaker for the cooler has flipped to the “off” position. Resetting it might solve the issue.
A fuse that keeps blowing could signal a bigger problem, like an overloaded circuit. Avoid repeatedly resetting the breaker without identifying the root cause—it could damage your system. Call a licensed electrician if you’re unsure how to proceed.
Using the wrong fuse type is another common mistake. Double-check that your fuses match the manufacturer’s specifications to avoid unnecessary failures.
Faulty Thermostat
Sometimes the thermostat is to blame for electrical issues. If the walk-in cooler isn’t cooling properly, test the thermostat by adjusting the temperature settings. Does the system respond? If not, the thermostat might need replacement.
Loose wiring inside the thermostat can also disrupt its functionality. Carefully inspect the connections for any signs of looseness or corrosion. Tightening or cleaning the wires can often fix the problem.
A thermostat that isn’t calibrated correctly can throw off the entire cooling system. Use a separate thermometer to verify the temperature inside the cooler. If there’s a mismatch, recalibrating the thermostat might restore its accuracy.
Have you experienced any of these electrical issues before? If so, how did you solve them? Troubleshooting electrical failures may seem daunting, but breaking it into these simple steps can save you time and money.
Airflow Blockages
Airflow blockages can cause serious issues in walk-in coolers. Proper airflow ensures consistent cooling and efficient operation. Blockages can lead to uneven temperatures, frozen products, or equipment strain. Identifying and resolving these blockages promptly is crucial for maintaining performance and preventing costly repairs. Below are common causes of airflow issues and how to address them.
Obstructed Vents
Vents blocked by items or debris restrict airflow inside the cooler. Placing products too close to vents can hinder air circulation. Ensure at least a few inches of space around all vents. Inspect vents regularly for visible obstructions or dust buildup. Clear any blockages immediately to restore proper airflow.
Dirty Evaporator Coils
Dust and dirt on evaporator coils reduce cooling efficiency. Dirty coils limit heat exchange, leading to uneven temperatures. Clean the coils every few months using a soft brush or coil cleaner. Regular maintenance prevents dirt buildup and ensures the system runs smoothly.
Fan Malfunctions
Fans play a key role in distributing air inside the cooler. Malfunctioning or broken fans disrupt airflow and cooling efficiency. Listen for unusual noises or vibrations, which may indicate fan issues. Check fan blades for damage or obstructions. Replace faulty fans to restore proper airflow.
Refrigerant Concerns
Refrigerant concerns are among the most common issues you might face when troubleshooting your walk-in cooler. These problems can directly impact the cooler’s ability to maintain the correct temperature, potentially spoiling valuable inventory. Understanding and addressing refrigerant issues promptly can save you from costly repairs and downtime.
Low Refrigerant Levels
Low refrigerant levels can severely affect your walk-in cooler’s performance. If your cooler isn’t maintaining the set temperature, this might be the first thing to check. A pressure gauge can help you confirm if the refrigerant level is below the required amount.
Think about the last time your cooler wasn’t cooling properly—did you notice frost buildup on the coils or warmer air inside? These are clear signs of low refrigerant. Adding refrigerant can resolve the issue, but make sure to identify the root cause to prevent recurrence.
Leaks In Refrigerant Lines
Refrigerant leaks are another common culprit behind cooling issues. Small leaks can go unnoticed for weeks, gradually reducing efficiency. If you suspect a leak, inspect the refrigerant lines and fittings for any oily residue or damage.
Have you ever wondered why your refrigerant levels keep dropping despite refilling them? It’s likely a leak. Seal the damaged section or replace the faulty line to ensure the refrigerant stays where it belongs.
Incorrect Refrigerant Type
Using the wrong refrigerant type can cause operational inefficiencies or even damage your walk-in cooler. This often happens when repairs are done hastily, or the original specifications are overlooked.
Check your cooler’s manual or service documentation to confirm the correct refrigerant type. If you’ve accidentally used the wrong one, consult a licensed technician to safely remove and replace it. It’s worth asking: could this mistake be avoided with better record-keeping?
Addressing refrigerant concerns doesn’t just protect your cooler—it also prevents unnecessary expenses. What steps will you take today to ensure your cooler runs smoothly tomorrow?

Credit: hvacknowitall.com
Door Seal Problems
Door seal problems can lead to inefficiency in walk-in coolers. A properly sealed door prevents cold air from escaping and keeps moisture out. Issues like worn gaskets or improper closure can increase energy costs and reduce cooling performance. Identifying and addressing these problems early can save time and money. Below, we’ll explore common door seal issues and how to troubleshoot them effectively.
Worn Or Damaged Gaskets
Gaskets create an airtight seal around the cooler door. Over time, they can crack, tear, or wear out. Damaged gaskets allow cold air to escape, forcing the cooler to work harder. Inspect the gasket edges for visible tears, gaps, or brittleness. Run your hand along the gasket to feel for air leaks. Replace the gasket if it no longer seals properly. Regular cleaning can also extend its life and prevent cracks.
Improper Door Closure
A misaligned door can prevent a tight seal, even with good gaskets. Check the hinges and latches for wear or loose screws. Ensure the door closes evenly without resistance. If the door doesn’t align, adjust the hinges or replace worn components. A properly closing door maintains efficiency and reduces strain on the cooling system.
Excess Moisture Build-up
Moisture build-up near the door often points to a sealing issue. Condensation forms when warm air enters through gaps. Check for wet spots or frost around the door frame. Inspect both the gaskets and the door alignment for problems. Fixing these issues will stop the moisture and improve overall performance. Use a dehumidifier if excessive moisture persists after repairs.
Ice And Frost Build-up
Ice and frost build-up in your walk-in cooler is more than a minor inconvenience. It can reduce cooling efficiency, damage stored goods, and even lead to expensive repairs. By understanding the common causes, you can troubleshoot these issues and restore your cooler’s performance quickly.
Frost On Evaporator Coils
Frost on evaporator coils often signals airflow problems or incorrect temperature settings. Start by checking if the fan is running properly and not blocked by debris. If the frost persists, it’s worth inspecting whether the thermostat is set too low for the humidity level inside the cooler.
Dirty coils are another culprit. Dust and grime can restrict airflow, causing frost to form faster. Cleaning the coils regularly with a coil brush or mild detergent can help prevent frost build-up. Have you overlooked this simple maintenance step?
Ice Accumulation On Walls
Ice forming on the cooler walls can indicate poor insulation or frequent door opening. If your cooler is next to a heat source or has worn-out seals, warm air may be sneaking inside and freezing against the walls. Replacing damaged seals or repositioning the cooler can minimize this issue.
Another tip is to monitor door usage. Are employees leaving the door open longer than necessary? Installing self-closing hinges can reduce warm air infiltration and limit ice formation on walls.
Blocked Drain Lines
Blocked drain lines are a common reason for ice build-up at the base of your cooler. These clogs often happen due to dirt, grease, or food particles accumulating over time. Check the drain pan and line regularly for blockages and clean them with a mix of warm water and vinegar.
If ice has already formed due to a blockage, carefully melt it with a hairdryer or warm cloth. Have you tried this quick fix before calling a technician? Keeping drain lines clear can save you both time and money.
Ice and frost issues in your walk-in cooler are manageable with proactive steps. Next time you spot frost on coils, walls, or near the drain, use these actionable tips to troubleshoot effectively. Remember, small fixes today can prevent big headaches tomorrow!
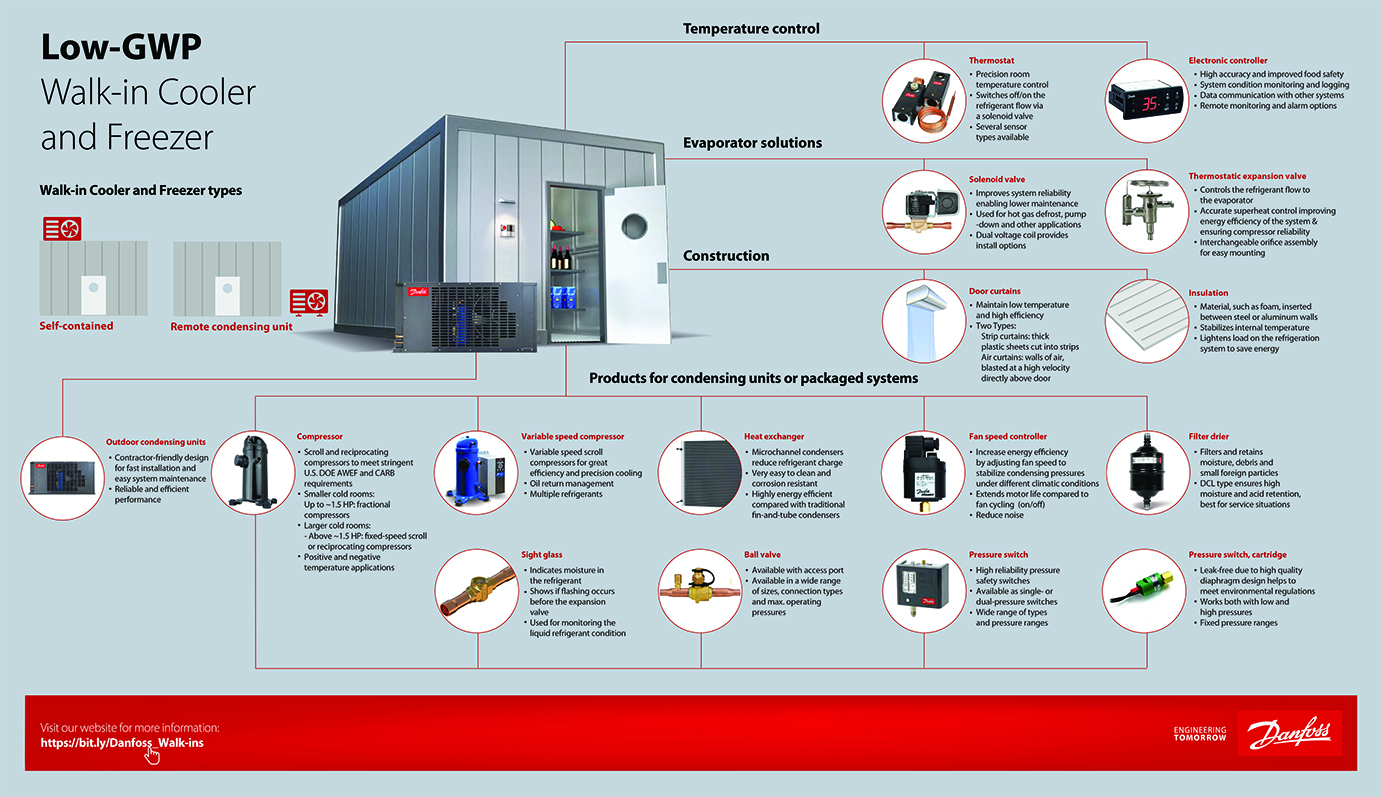
Credit: www.danfoss.com
Unusual Noises
Unusual noises in a walk-in cooler often signal underlying issues. These sounds can disrupt operations and may indicate mechanical problems. Identifying the noise type is crucial for effective troubleshooting. Below, we explore common noises and their potential causes.
Humming Or Buzzing Sounds
A humming or buzzing noise usually comes from the compressor or fan motor. It might indicate electrical issues or worn-out components. Check for loose wiring around the motor or compressor. Inspect the fan blades for dirt buildup or damage. Regular cleaning can prevent humming caused by debris.
Rattling Or Vibrating Noises
Rattling noises often stem from loose parts or mounting brackets. Vibrations might occur if the cooler is unevenly placed on the floor. Tighten screws and bolts to eliminate rattling. Place vibration-absorbing pads under the cooler for better stability. Inspect the condenser coil to ensure it’s securely attached.
High-pitched Whistling
Whistling sounds might indicate air leaks or pressure problems. Check the cooler door gaskets for cracks or gaps. Inspect the refrigerant system for pressure inconsistencies. Use a sealant to repair small leaks around the door frame. Ensure the cooler door closes tightly to avoid whistling noises.
Maintenance Tips
Proper maintenance is the backbone of keeping your walk-in cooler running efficiently. Neglecting routine care can lead to costly repairs, spoiled inventory, and unnecessary stress. By following a few simple yet effective maintenance tips, you can extend the life of your cooler and prevent sudden breakdowns.
Regular Cleaning Schedule
A clean walk-in cooler isn’t just about aesthetics—it’s essential for performance. Dirt, debris, and grease buildup can overwork your cooler’s components, leading to wear and tear. Set a weekly schedule to clean the interior and exterior surfaces with warm water and a mild detergent.
Pay special attention to the door gaskets, shelves, and corners where grime tends to accumulate. Dust the condenser coils every three months to improve airflow and efficiency. If you’re thinking, “Do I really need to clean that often?”—yes, you do. Cleanliness directly impacts your cooler’s energy use and cooling power.
Inspection Checklist
Would you drive a car without checking the tires or oil? Your walk-in cooler deserves the same vigilance. Create a simple inspection checklist to catch small issues before they turn into big problems.
- Check the door gaskets for cracks or wear—they are crucial for maintaining a proper seal.
- Ensure the thermostat is reading and maintaining the correct temperature.
- Look for unusual noises from the motor or compressor. Strange sounds could mean trouble.
- Inspect for water leaks or condensation buildup, which can lead to mold or damage.
Perform these checks monthly, and keep a log to track any recurring issues. This habit ensures you’re staying ahead of potential failures.
Professional Servicing
Some problems need an expert touch. Schedule a professional servicing for your walk-in cooler at least once a year. Technicians can identify hidden issues, optimize the system, and ensure components like refrigerant levels and fans are in top shape.
Think of it this way: just like you visit the doctor for an annual check-up, your cooler deserves the same care. A technician’s keen eye can save you from costly, unexpected repairs. Can you afford not to make this investment?
By combining regular cleaning, diligent inspections, and professional servicing, you can keep your walk-in cooler running smoothly for years to come. Isn’t it worth the effort to protect your business and inventory?
Conclusion
Troubleshooting a walk-in cooler doesn’t have to be overwhelming. With a clear guide, you can quickly pinpoint common issues. Regular maintenance can also prevent unexpected breakdowns. Always check basic components like the thermostat, fans, and seals first. Addressing minor problems early can save time and money.
If the issue persists, consult a professional for help. A well-functioning cooler keeps food safe and operations smooth. Use this troubleshooting chart as a reliable resource. It simplifies the process and keeps your cooler running efficiently. Stay proactive and ensure consistent performance for your cooling needs.