Warn Winch Troubleshooting: Expert Tips to Fix Common Issues
Having trouble with your Warn winch? Winches are essential for many tasks, but they can have issues.
Don’t worry; we’re here to help you fix common problems. Warn winches are known for their reliability and strength. Yet, like any other tool, they can sometimes fail. Understanding the basics of winch troubleshooting can save time and money. This guide will help you identify and solve common issues with your Warn winch.
From electrical faults to mechanical problems, we’ll cover the key areas to check. Let’s get your winch back in action!

Credit: www.pirate4x4.com
Introduction To Warn Winch Troubleshooting
Experiencing issues with your Warn winch can be frustrating. Learn how to identify common problems and find effective solutions. This guide helps you keep your winch running smoothly.
A Warn winch is a vital tool for off-road adventures. It helps you get out of tough spots. But like any tool, a winch can have issues. Knowing how to troubleshoot can save you time and hassle. This guide will help you understand common problems and how to fix them.Importance Of Proper Maintenance
Proper maintenance keeps your winch working well. Regular checks can prevent many issues. Clean and inspect the winch often. Look for worn or damaged parts. Lubricate moving parts to ensure smooth operation. This can extend the life of your winch.Common Problems Overview
Winches can face several common issues. The motor might not run. This could be due to electrical problems. A winch may also run slowly or stop working under load. This often points to issues with the battery or connections. Another problem is the winch line getting stuck or tangled. Regularly check the line for wear and tear. Ensure it is spooled correctly to avoid this issue. Understanding these problems helps you troubleshoot effectively. “`Electrical Issues
Experiencing electrical issues with your Warn winch can be frustrating. Common problems include dead batteries, faulty wiring, or malfunctioning solenoids. Regular maintenance helps prevent these issues.
Experiencing electrical issues with your Warn winch can be frustrating. These problems often stem from a few common sources. Addressing these can save you time and money. Let’s explore some frequent culprits.Battery Problems
A weak or dead battery can halt your winch. Ensure your battery has enough charge. Use a multimeter to check the voltage. A fully charged battery should read around 12.6 volts. Clean any corrosion on the battery terminals. Corrosion can impede the electrical flow. Tighten all connections securely. Loose connections can cause intermittent power loss.Solenoid Failures
A faulty solenoid can prevent your winch from operating. Listen for a clicking sound when you activate the winch. No sound? Your solenoid might be bad. Test the solenoid by bypassing it. Connect a jumper wire between the battery and the motor. If the winch runs, replace the solenoid. Ensure all solenoid connections are tight and clean. “`Mechanical Malfunctions
Dealing with mechanical malfunctions in your Warn winch can be frustrating. These issues can halt your work and cause delays. This section covers common mechanical problems. Let’s dive into common issues like gearbox problems and drum issues.
Gearbox Problems
The gearbox is essential for your winch’s performance. It transfers power to the drum. If the gearbox fails, the winch won’t work properly.
Common signs of gearbox problems include:
- Strange noises
- Difficulty in engaging gears
- Loss of power
To address gearbox issues:
- Check for any visible damage.
- Ensure the gears are properly lubricated.
- Inspect the gearbox for wear and tear.
Regular maintenance can prevent most gearbox problems. Keep the gears clean and lubricated.
Drum Issues
The drum is where the winch cable winds and unwinds. Any problem with the drum can affect the winch’s efficiency.
Common drum issues include:
- Cable getting stuck
- Uneven winding
- Drum not turning
To fix drum issues:
- Check for any obstructions around the drum.
- Ensure the cable is properly aligned.
- Inspect the drum for any signs of damage or wear.
Proper cable management can help prevent drum issues. Always keep the cable tight and even.
By addressing these mechanical malfunctions, you can ensure your Warn winch runs smoothly. Regular checks and maintenance are key.

Credit: www.reddit.com
Cable And Rope Issues
Winch cables and ropes face many challenges. Over time, these components can show signs of wear and damage. Understanding common issues can help you maintain and fix your Warn winch. Let’s delve into some typical cable and rope problems.
Frayed Cable
A frayed cable is a common issue. It can weaken the winch’s pulling power and lead to accidents. Regular inspection is key. Look out for broken strands. Also, check for kinks and rust.
Here are steps to address a frayed cable:
- Inspect the cable before each use.
- Replace the cable if you find significant damage.
- Lubricate the cable to prevent rust and wear.
Maintaining your cable can extend its lifespan and keep you safe.
Rope Jamming
Rope jamming happens when the rope gets tangled or stuck. It can render your winch unusable. Proper spooling can prevent this issue.
Follow these tips to avoid rope jamming:
- Re-spool the rope neatly after each use.
- Ensure even tension while spooling.
- Avoid crossing the rope over itself.
If a jam occurs, unwind the rope completely and re-spool it carefully. These simple steps can keep your winch running smoothly.
Remote Control Problems
Remote control problems can be a frustrating experience when using a Warn winch. If the winch fails to respond, the issue could lie within the remote control system. These problems may stem from various sources. This section will explore common remote control problems, focusing on wiring issues and signal interference.
Wiring Issues
Wiring issues often cause remote control problems. Check all connections between the remote and winch. Look for loose or damaged wires. Ensure connectors are secure. Corroded contacts can disrupt the signal. Clean any dirt or rust from the contacts. Replace any faulty wires. Secure all connections properly.
Signal Interference
Signal interference can also hinder remote control function. Nearby electronic devices can cause interference. Devices like radios or other wireless equipment. Move them away from the winch area. Metal objects can block signals too. Ensure the remote has a clear line of sight to the winch. Position the antenna correctly. This enhances signal strength and reduces interference.
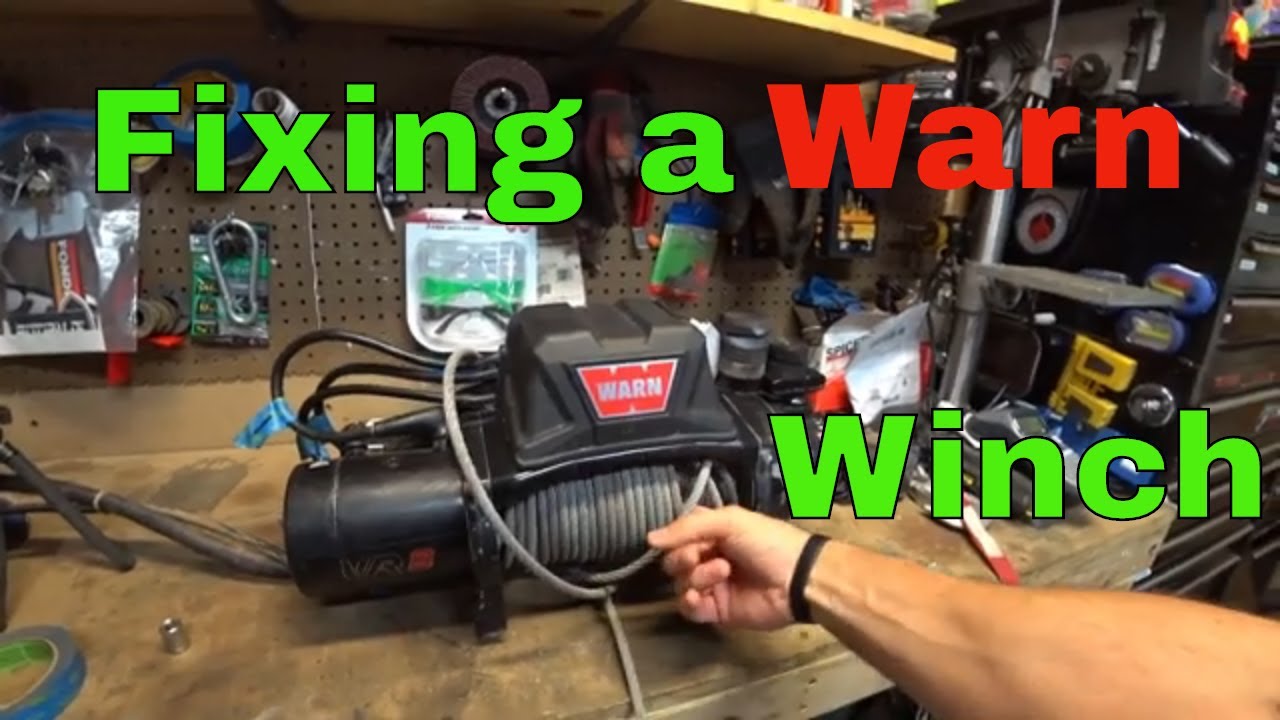
Credit: www.youtube.com
Motor Troubles
Experiencing motor troubles with your Warn winch can be frustrating. These issues can stop you from completing your tasks. Understanding common motor problems helps in quick fixes. Let’s look into two main issues: overheating and power loss.
Overheating
Overheating is a frequent problem with winch motors. It happens when the motor runs for too long without a break. High temperatures can damage the motor. To prevent overheating, check the motor’s temperature regularly. Allow the motor to cool down between uses. If overheating persists, inspect the motor for dirt and debris. Clean the motor to ensure proper ventilation. If the problem continues, consider getting professional help.
Power Loss
Power loss in your Warn winch can be due to several reasons. First, check the battery and cables. Loose or corroded connections can cause power issues. Tighten or replace any damaged cables. Next, examine the motor for wear and tear. Old motors may not perform well. Replacing worn-out parts can restore power. Finally, ensure the winch is not overloaded. Excessive weight can strain the motor, leading to power loss. Follow the manufacturer’s guidelines for the maximum load.
Preventive Measures
Regularly inspect winch components to prevent malfunctions. Clean and lubricate parts to ensure smooth operation. Always check for wear and tear.
Maintaining a Warn winch in top condition requires proactive measures. Preventive actions reduce the likelihood of issues and extend the winch’s life. Here are some key steps to ensure your winch remains reliable and efficient.Regular Inspection
Inspect the winch regularly for any signs of wear or damage. Check the cables for fraying or kinks. Examine the mounting bolts and ensure they are secure. Look at the drum for any dents or cracks. Make sure the electrical connections are clean and tight. A quick inspection can catch problems early.Proper Storage
Store the winch in a dry, clean place. Avoid exposure to moisture which can cause rust. Keep the winch covered when not in use. This protects it from dust and debris. Ensure the winch is not exposed to direct sunlight for long periods. Proper storage keeps the winch in good working condition. “`When To Seek Professional Help
Winch problems can sometimes be tricky to solve. While many issues can be fixed on your own, there are times when seeking professional help becomes necessary. Knowing when to call in an expert can save you time and prevent further damage to your winch. In this section, we’ll discuss how to identify severe issues and find a reliable technician.
Identifying Severe Issues
Certain winch problems signal the need for professional intervention. For example, if your winch motor makes unusual noises, it might have internal damage. Strange smells like burning could indicate electrical issues. These situations require expert attention.
If your winch cable shows significant wear or fraying, it poses a safety risk. Do not attempt to use it. Instead, contact a professional immediately. Severe corrosion on any part of the winch is another red flag. It can weaken the system and lead to failure.
Finding A Reliable Technician
Locating a trustworthy technician ensures your winch gets the best care. Start by asking friends or colleagues for recommendations. Personal referrals often lead to reliable services.
You can also check online reviews. Look for technicians with high ratings and positive feedback. Ensure they have experience with winches and relevant certifications. Verify their credentials and ask about their experience.
Lastly, get a detailed estimate before any work begins. This helps you understand the costs and avoid surprises. A good technician will explain the issues and the necessary repairs clearly.
Frequently Asked Questions
Why Is My Warn Winch Not Working?
Check the power connections and battery. Loose connections or a dead battery can cause issues.
How Do I Reset My Warn Winch?
Disconnect the power for a few minutes. Reconnect and test the winch. This can reset the system.
What Causes My Warn Winch To Stop Pulling?
Overheating, overloading, or a damaged motor can stop the winch. Allow it to cool, reduce the load, or inspect the motor.
How Do I Maintain My Warn Winch?
Regularly clean and lubricate the winch. Check cables and connections for wear and tear.
Why Is My Warn Winch Making Noise?
Noises often mean mechanical issues. Inspect for loose parts or worn gears. Lubricate if necessary.
Conclusion
Troubleshooting your Warn winch doesn’t have to be daunting. Follow these simple steps and keep your winch in top shape. Regular checks and proper maintenance can prevent many issues. Always ensure the winch is clean and well-lubricated. If problems persist, consult the manual or seek professional help.
Keeping these tips in mind will help you maintain a reliable winch, ready for any challenge. Stay safe and happy winching!