Ge Ptac Troubleshooting Guide: Expert Tips to Fix Common Issues
GE PTAC units are widely used for heating and cooling. They are reliable but can sometimes encounter issues.
In this guide, we’ll explore common problems with GE PTAC units and their solutions. Understanding these issues can save time and money. Whether it’s a heating malfunction or a cooling problem, this troubleshooting guide will help you diagnose and fix it.
By the end, you’ll feel more confident in maintaining your PTAC unit. Stay tuned as we dive into the specifics, ensuring your unit runs efficiently all year round.
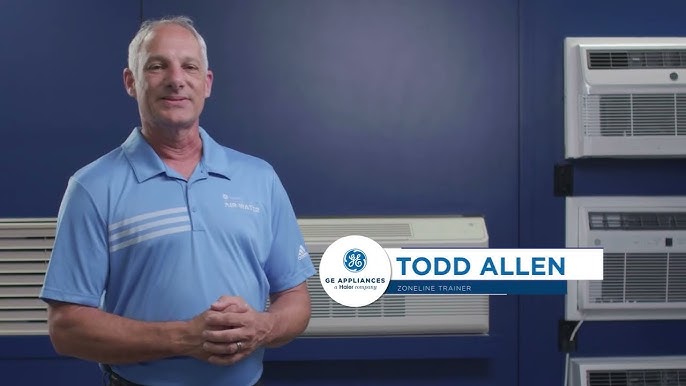
Credit: www.youtube.com
Introduction To Ge Ptac Units
GE PTAC units, short for Packaged Terminal Air Conditioners, are popular in hotels, apartments, and offices. These units combine heating and cooling capabilities, providing comfort all year round. Understanding how these units work and their maintenance needs is crucial for optimal performance.
What Is A Ptac Unit?
A PTAC unit is a self-contained heating and cooling system. It is installed through a wall and is designed to serve a single room. These units are known for their efficiency and ease of installation. PTAC units have both heating and cooling modes, making them versatile.
Key features of PTAC units include:
- Compact Design: Fits through a wall, saving space.
- Energy Efficiency: Consumes less power compared to central systems.
- Ease of Use: Simple controls for temperature adjustment.
Importance Of Regular Maintenance
Regular maintenance of GE PTAC units is essential. It ensures the unit operates efficiently and prolongs its lifespan. Neglecting maintenance can lead to higher energy bills and frequent repairs.
Here are some critical maintenance tasks:
- Filter Cleaning: Clean or replace filters monthly to maintain air quality.
- Coil Inspection: Check coils for dust and debris, clean if necessary.
- Thermostat Calibration: Ensure the thermostat is accurate for consistent temperature control.
Regular check-ups can identify issues before they become major problems. This proactive approach can save time and money.
In summary, understanding GE PTAC units and maintaining them regularly can enhance their performance. This knowledge helps in troubleshooting and ensures a comfortable environment.

Credit: www.youtube.com
Common Issues In Ge Ptac Units
GE PTAC units are popular for their reliability and efficiency. Yet, like any appliance, they can face issues. Knowing common problems helps maintain your unit and ensures it runs smoothly.
Unit Not Cooling Properly
If your GE PTAC unit is not cooling, several factors could be the cause. First, check the thermostat settings. Ensure it is set to a cooler temperature. A dirty air filter can also restrict airflow. Clean or replace the filter regularly. Another possible issue is low refrigerant levels. This requires a professional to inspect and refill. Lastly, examine the condenser coils. Dust and dirt can accumulate, affecting performance. Clean the coils carefully to restore cooling efficiency.
Strange Noises
Strange noises from your GE PTAC unit can be alarming. These sounds often indicate mechanical issues. A buzzing noise might mean loose parts. Check the unit for any loose screws or components. Clicking sounds could be a sign of electrical problems. Inspect the wiring and connections for any damage. A rattling noise usually points to debris inside the unit. Clean the interior to remove any obstructions. If the noise persists, consult a technician for a thorough inspection.
Basic Troubleshooting Steps
When your GE PTAC unit is not working properly, following basic troubleshooting steps can help. These steps can solve many common problems quickly. Below are some simple checks to try before calling a professional.
Inspecting The Filter
The filter is a crucial part of your GE PTAC unit. A dirty filter can cause many issues. It can reduce airflow and efficiency. Regularly check the filter for dust and debris.
To inspect the filter, first, turn off the unit. Remove the front panel to access the filter. Pull out the filter gently. If the filter is dirty, wash it with mild soap and water. Let it dry completely before reinstalling it. A clean filter helps the unit run smoothly.
Checking Thermostat Settings
Incorrect thermostat settings can cause your GE PTAC unit to malfunction. Ensure the thermostat is set to the desired temperature. Sometimes, the settings might get changed accidentally.
If the unit is not cooling, check if the thermostat is set to “cool” mode. For heating issues, verify that it is set to “heat” mode. Also, make sure the temperature setting is appropriate. Adjust the settings as needed.
Sometimes, the problem can be with the thermostat itself. Replace the batteries if needed. If the thermostat is still not working correctly, it might need replacement.
Advanced Troubleshooting Techniques
Advanced troubleshooting techniques can help fix complex issues with your GE PTAC unit. These methods require a deeper understanding of the system. They involve checking electrical components and refrigerant levels. This guide will walk you through these advanced steps.
Testing Electrical Components
Testing electrical components ensures your GE PTAC operates safely. Start by turning off the power. Use a multimeter to check for continuity in wires. Look for any signs of wear or damage. Replace any faulty wires immediately.
Next, test the capacitors. Set your multimeter to the capacitance setting. Place the probes on the capacitor terminals. Compare the reading to the manufacturer’s specifications. Replace the capacitor if the reading is outside the range.
Check the fan motor. Set the multimeter to the ohms setting. Measure the resistance between the motor terminals. A reading of zero or infinite indicates a faulty motor. Replace the motor if needed.
Examining Refrigerant Levels
Refrigerant levels affect the cooling efficiency of your GE PTAC. Low levels can indicate a leak. Use a refrigerant gauge to check the levels. Connect the gauge to the service port. Compare the reading to the recommended pressure range.
If levels are low, recharge the system with the correct refrigerant. Follow the manufacturer’s guidelines. Ensure you do not overfill. Overcharging can damage the unit.
Check for leaks if refrigerant levels drop frequently. Use a leak detector to find the source. Repair any leaks before recharging the system. Regular maintenance can prevent refrigerant issues.
When To Call A Professional
There are times when you can fix issues with your GE PTAC unit yourself. But sometimes, you need to call a professional. Knowing when to call a professional can save you time and money. It can also prevent further damage to your unit. This guide will help you understand when it’s time to seek expert help.
Identifying Serious Issues
Some problems with your GE PTAC unit can be serious. You should call a professional if you notice any of the following issues:
- Strange noises: Unusual sounds can mean mechanical problems.
- Unpleasant odors: Bad smells can signal mold or electrical issues.
- Leakage: Water leaks can damage your home and the unit.
- Frequent cycling: The unit turns on and off often.
- No cooling or heating: The unit fails to cool or heat properly.
If you experience any of these issues, it’s best to call a professional. Attempting to fix serious problems on your own can make things worse.
Finding A Qualified Technician
Finding the right technician is important. Here are some tips to help you find a qualified professional:
- Check for certifications. Make sure the technician is certified to work on GE PTAC units.
- Read reviews. Look for feedback from other customers.
- Ask for references. A good technician will have satisfied customers who can vouch for their work.
- Get a quote. Ask for a detailed estimate before any work begins.
- Verify insurance. Ensure the technician has insurance to cover any damages.
Taking these steps can help you find a reliable and skilled technician. This ensures your GE PTAC unit gets the best care possible.
Preventive Maintenance Tips
Regularly clean filters and check for obstructions in your GE PTAC unit. Ensure proper airflow by clearing any dust buildup. Perform these checks to maintain efficiency and prevent issues.
Preventive maintenance is essential for your GE PTAC unit. It helps to ensure your unit operates efficiently and lasts longer. Following a few simple steps can save you time and money.Regular Cleaning Schedule
Clean your PTAC unit regularly. Dust and dirt can clog the filters and vents. This reduces the unit’s efficiency. Use a vacuum cleaner with a brush attachment. Gently clean the filters and vents. Do this at least once a month. It helps to keep the air flowing smoothly.Seasonal Check-ups
Inspect your PTAC unit before each season. Check for any signs of wear or damage. Look at the coils and fins. Ensure they are clean and not bent. A simple visual check can prevent bigger problems. If you notice anything unusual, consider calling a professional. Regular check-ups keep your unit running efficiently. “`Optimizing Ptac Performance
Optimizing your PTAC unit’s performance is essential for maintaining a comfortable indoor environment and reducing energy costs. By focusing on energy efficiency and enhancing airflow, you can ensure your PTAC unit operates at its best. This guide will provide practical tips to help you achieve optimal performance.
Energy Efficiency Tips
Keeping your PTAC unit energy-efficient saves money. Regular maintenance is key. Clean the filters monthly to ensure proper airflow. Dirty filters force the unit to work harder, using more energy. Check for and seal any gaps around the unit. This prevents air leaks that reduce efficiency. Setting the thermostat to an appropriate temperature also helps. Aim for 78°F in summer and 68°F in winter. These settings balance comfort and energy use.
Enhancing Airflow
Proper airflow is crucial for PTAC performance. Start by clearing obstructions around the unit. Furniture, curtains, or other items can block air circulation. Make sure vents and grilles are free of dust and debris. Regularly vacuum or wipe them clean. Consider using fans to aid air movement. Ceiling or floor fans help distribute air evenly. This reduces the strain on your PTAC unit. Finally, ensure the unit is level. A tilted unit may not drain properly, affecting airflow and performance.
Resources For Ptac Owners
Owning a Packaged Terminal Air Conditioner (PTAC) can sometimes be challenging. Troubleshooting issues can be more manageable with the right resources. This guide will help you find the best resources for PTAC owners.
User Manuals And Guides
User manuals and guides are essential for PTAC troubleshooting. They offer detailed instructions and solutions for common problems. These resources often contain diagrams and step-by-step guides. Most PTAC units come with a manual. You can also download manuals from the manufacturer’s website.
Online Support Communities
Online support communities provide valuable help for PTAC owners. Forums and groups allow users to share experiences and solutions. You can find advice from other PTAC owners and experts. These communities are great for getting quick answers. Some popular places include Reddit, HVAC forums, and social media groups.
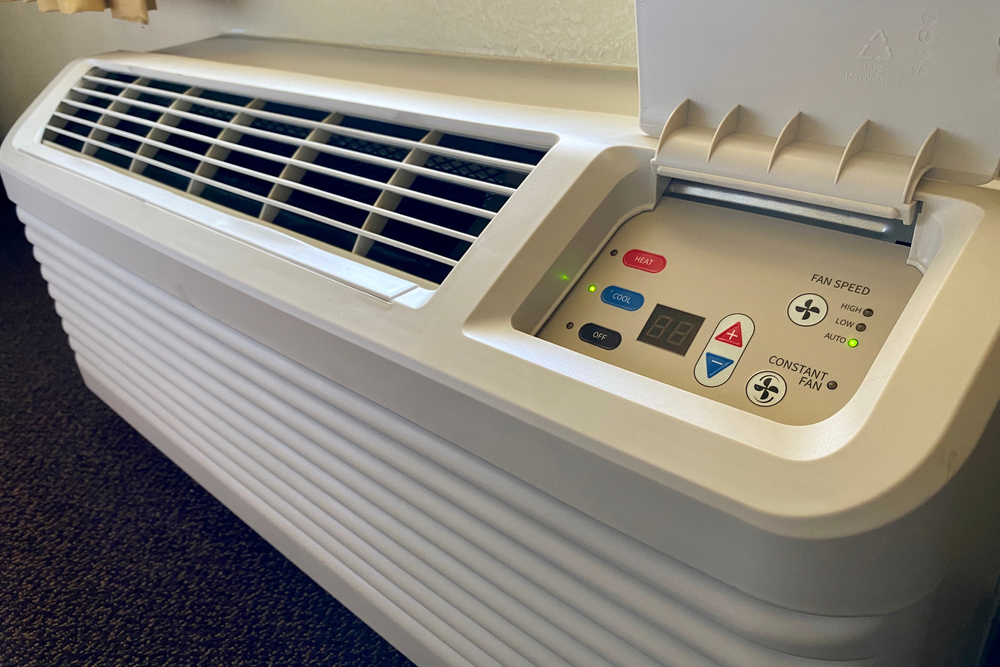
Credit: www.ptacunits.com
Frequently Asked Questions
How Do I Reset My Ge Ptac Unit?
To reset your GE PTAC unit, turn off the unit, unplug it, wait 5 minutes, then plug it back in.
Why Is My Ge Ptac Not Cooling?
A dirty air filter or blocked condenser can cause poor cooling. Clean or replace the filter and check for blockages.
What Does The Error Code On My Ge Ptac Mean?
Refer to your unit’s manual. Error codes indicate specific issues like sensor problems, power failures, or refrigerant issues.
How Often Should I Clean My Ge Ptac Filter?
Clean the air filter every 30 days. This ensures efficient operation and prolongs the unit’s life.
Why Is My Ge Ptac Making Noise?
Noises can be due to loose parts, debris, or a failing motor. Inspect the unit and tighten or clean as needed.
Conclusion
Fixing your GE PTAC unit can be simple with our guide. Follow the steps listed, and you should resolve most issues. Regular maintenance keeps your unit running smoothly. Don’t forget to check filters and clean coils. Understanding these basics helps you save time and money.
We hope this guide helps you troubleshoot any problems. Thanks for reading, and good luck with your repairs!