Intertek Ice Maker Troubleshooting: Quick Fixes & Tips
Is your Intertek ice maker giving you trouble? Don’t worry—you’re not alone, and you’ve come to the right place.
When your ice maker stops working or doesn’t perform as it should, it can be frustrating, especially when you rely on it for cold drinks or entertaining guests. But here’s the good news: most ice maker issues are easier to fix than you might think.
In this guide, we’ll walk you through practical troubleshooting tips to get your Intertek ice maker back on track. Whether it’s not making ice, producing too little, or acting up in other ways, we’ll help you identify the problem and find a solution. Stick with us, and by the end of this article, you’ll feel confident tackling the issue—no need to call a repair technician just yet! Ready to get your ice maker working like new again? Let’s dive in.
Credit: www.tiktok.com
Common Issues With Intertek Ice Makers
Intertek ice makers are reliable, but like any appliance, issues can arise. Understanding these problems helps you fix them quickly. Below, we discuss common issues and practical solutions.
Ice Maker Not Turning On
An ice maker that won’t power on can be frustrating. Start by checking the power cord. Ensure it’s securely plugged into the outlet. Inspect the outlet itself. Use another device to confirm it’s working. Check the circuit breaker to rule out a tripped switch. If all seems fine, look at the control panel. The power button might not be activated. Lastly, inspect the internal wiring for any visible damage.
No Ice Production
If your ice maker isn’t producing ice, the water supply might be the issue. Confirm the water line is connected and not kinked. Check for water flow by testing the valve. Clean the water filter if it’s clogged. A full ice storage bin can also halt production. Empty the bin to allow new ice to form. Additionally, inspect the freezer temperature. It should be set between 0°F and 5°F.
Slow Ice Production
Slow ice production can signal a few problems. First, check the temperature settings. Warmer settings can delay ice formation. Clean the condenser coils to improve cooling efficiency. Dust and debris can hinder performance. Inspect the water filter and replace it if clogged. Low water pressure can also slow production. Ensure the water supply line provides adequate pressure.
Power And Connectivity Checks
Ensuring your Intertek ice maker receives proper power and connectivity is crucial. Ice makers rely on stable electricity and secure connections to function effectively. A quick check of these can resolve many issues without professional help.
Below are three essential steps for troubleshooting power and connectivity problems. Follow these to pinpoint the issue and restore your ice maker’s performance.
Inspecting The Power Supply
Check if the ice maker is plugged into a working outlet. Sometimes, power cords can get loose or disconnected. Test the outlet by plugging in another device to confirm if it is functional. If the outlet works, ensure the ice maker’s cord is securely connected.
Look for visible damage on the cord like fraying or cuts. Damaged cords can interrupt power flow and should be replaced immediately. Always use the recommended power source for your model to avoid electrical issues.
Checking The Circuit Breaker
Locate your home’s circuit breaker panel and inspect the ice maker’s circuit. A tripped breaker can prevent the ice maker from working. Flip the breaker off and then on to reset it.
If the breaker trips repeatedly, there might be an electrical overload or fault. Consult an electrician if resetting doesn’t solve the problem. Avoid using other high-power devices on the same circuit to reduce the load.
Verifying Cable Connections
Ensure all cables connecting the ice maker to power and water are secure. Loose or disconnected cables can disrupt the machine’s performance. Check for tight connections and reconnect any loose cables firmly.
Inspect cables for signs of wear or damage. Faulty cables can cause malfunctions and need replacement. Properly aligned and undamaged cables improve efficiency and prevent outages.
Water Supply Troubleshooting
A steady water supply is key to a properly functioning ice maker. Issues with water flow can disrupt ice production. Troubleshooting water supply problems ensures your Intertek ice maker works efficiently. Follow these steps to address common water-related issues.
Ensuring Proper Water Flow
Check the water line for kinks or bends. Straighten any twisted sections to restore proper flow. Make sure the water supply valve is fully open. A partially closed valve can reduce water pressure. Inspect the connection between the water line and the ice maker. Tighten any loose fittings to prevent leaks or disruptions.
Cleaning The Water Filter
A clogged water filter can block water flow. Locate the filter and remove it for inspection. Rinse it under running water to remove debris. If the filter is heavily clogged, replace it with a new one. Regular cleaning or replacement keeps water flowing smoothly.
Inspecting Water Inlet Valve
The water inlet valve controls water entry into the ice maker. Disconnect the ice maker from power before inspecting it. Check the valve for visible cracks or damage. Ensure the valve’s screen is free of debris. Replace the valve if it’s faulty or damaged to restore proper water flow.
Credit: www.tiktok.com
Temperature And Environment Factors
Temperature and environmental factors play a huge role in how well your Intertek ice maker performs. If your ice maker isn’t producing enough ice or is acting up, the surrounding conditions might be the culprit. Let’s dig into how adjusting temperature settings, preventing overheating, and proper placement can make a big difference.
Adjusting Freezer Temperature
Your ice maker is highly sensitive to the freezer’s temperature. If it’s too warm, the ice won’t form properly. Set your freezer temperature between 0°F and 5°F for optimal performance.
Check your freezer’s thermostat with a thermometer to ensure accuracy. A faulty thermostat can give you incorrect readings, leading to improper adjustments. If your ice cubes are smaller than usual, the temperature might not be low enough.
Have you noticed your ice maker working slower on particularly warm days? That’s likely due to a higher freezer temperature. Don’t hesitate to adjust it slightly to compensate for changes in room temperature.
Avoiding Overheating Issues
Is your ice maker located near an oven, dishwasher, or another heat-emitting appliance? This can increase the temperature around the unit and affect its efficiency.
Keep the ice maker away from heat sources. Even direct sunlight streaming through a window can cause overheating. A shaded, cool location is always better.
You can also improve airflow around the unit to prevent overheating. Make sure there’s at least 2-3 inches of space around the sides and back of the ice maker. This allows heat to dissipate effectively.
Placing The Ice Maker Correctly
Where you place your ice maker matters more than you think. Poor placement can disrupt its cooling cycle, leading to slow or inefficient ice production.
Always position it on a flat, stable surface to keep it level. Uneven placement can cause the internal components to work harder, leading to wear and tear. Use a spirit level to check if needed.
Also, avoid placing the ice maker in an uninsulated garage or near drafty areas. Extreme cold or heat can hinder its ability to maintain the required internal temperature. Aim for a room temperature between 50°F and 90°F for best results.
Have you tried adjusting these factors yet? Sometimes, small tweaks can resolve what seems like a major issue. Start with these tips and see how your ice maker responds. You might save yourself a service call!
Cleaning And Maintenance Tips
Regular cleaning and maintenance of your Intertek ice maker ensures peak performance. Proper care prevents buildup, blockages, and extends the machine’s lifespan. Follow these practical tips to keep your ice maker running smoothly.
Descaling The Ice Maker
Mineral deposits can accumulate inside the ice maker over time. Descaling removes these deposits, improving efficiency and ice quality. Use a safe descaling solution recommended by the manufacturer. Mix the solution with water according to the instructions.
Turn off and unplug the ice maker before descaling. Pour the solution into the water reservoir. Let it sit for the specified duration to dissolve mineral buildup. Rinse the reservoir with clean water several times to remove any residue.
Removing Ice Blockages
Ice blockages can disrupt the machine’s operation. Clear these blockages to restore functionality. Start by turning off the ice maker and unplugging it. Use a soft plastic tool to carefully break apart the ice without damaging components.
If the blockage persists, check the water inlet for clogs. Clean the inlet using a soft brush and warm water. Once cleared, restart the machine and monitor its performance.
Cleaning Interior Components
Cleaning the interior components prevents mold and bacteria growth. Remove all ice from the tray before starting. Use a mild detergent mixed with warm water to clean the ice tray and water reservoir.
Wipe the interior surfaces with a soft cloth or sponge. Avoid abrasive cleaners or rough scrubbing tools to protect delicate parts. Rinse thoroughly with clean water and dry with a clean towel before reassembling.
When To Replace Parts
Ice makers are essential for keeping your beverages cold and refreshing. Over time, specific parts may wear out or stop functioning. Recognizing the signs early can help you avoid costly repairs. Here’s how to identify when parts of your Intertek ice maker need replacement.
Signs Of A Faulty Motor
The motor drives the entire ice-making process. A faulty motor often causes loud grinding noises during operation. If your ice maker struggles to produce ice or stops completely, the motor could be failing. A burning smell is another clear indicator of motor issues. Regular inspection can help catch these problems early.
Damaged Ice Trays
Ice trays can crack or warp over time, especially with frequent use. Damaged trays may cause uneven ice shapes or leaking water. Check for visible cracks or deformities. If the trays stick or fail to release ice properly, replacement is necessary. Using damaged trays can lead to further mechanical issues.
Worn-out Water Valves
Water valves control the flow of water into the ice maker. A worn-out valve can result in slow water filling or no water flow. If your ice maker produces small or hollow ice cubes, the valve may be failing. Water leaks around the valve area also signal wear and tear. Replacing the valve ensures consistent ice production.
Contacting Professional Support
Sometimes, troubleshooting your Intertek ice maker might require professional assistance. Whether the issue is beyond your expertise or you simply don’t have time to fix it yourself, contacting professional support can save you from unnecessary stress. But before you pick up the phone, there are a few things you should know to make the process smooth and efficient.
Warranty And Service Options
Before reaching out for help, check your warranty details. Many ice makers come with a manufacturer’s warranty that covers specific repairs or replacements. If your ice maker is still under warranty, contacting the manufacturer directly could be your best option to avoid out-of-pocket costs.
Some brands also offer extended service plans. These plans often cover maintenance and repairs, even after the initial warranty expires. If you’ve signed up for one of these, make sure you have the paperwork handy when contacting support.
Finding Certified Technicians
Not all repair professionals are created equal, and your ice maker deserves the best care. Look for certified technicians with experience handling Intertek appliances. Certification ensures they have the right skills and tools for the job.
You can start your search online. Websites like Yelp or Google Reviews can help you identify reputable technicians in your area. Don’t forget to read customer reviews to learn about their reliability and quality of service.
Another option is to ask friends or family for recommendations. Sometimes, a personal referral is more trustworthy than an online review.
Preparing For Service Calls
Before calling a technician, gather all the important details about your ice maker. Note the model number, purchase date, and a brief description of the problem. This information helps the technician diagnose the issue quickly.
Take a moment to check your schedule and choose a time slot for the service call. It’s better to pick a time when you’re available to answer questions or assist if needed. Also, make sure the area around the ice maker is clean and accessible.
Think about this: Have you tried basic troubleshooting steps yourself? Mention this to the technician. It saves time and shows you’ve done your homework.
By taking these steps, you’ll not only get your ice maker fixed faster but also ensure a hassle-free experience. So, what’s stopping you from making that call?
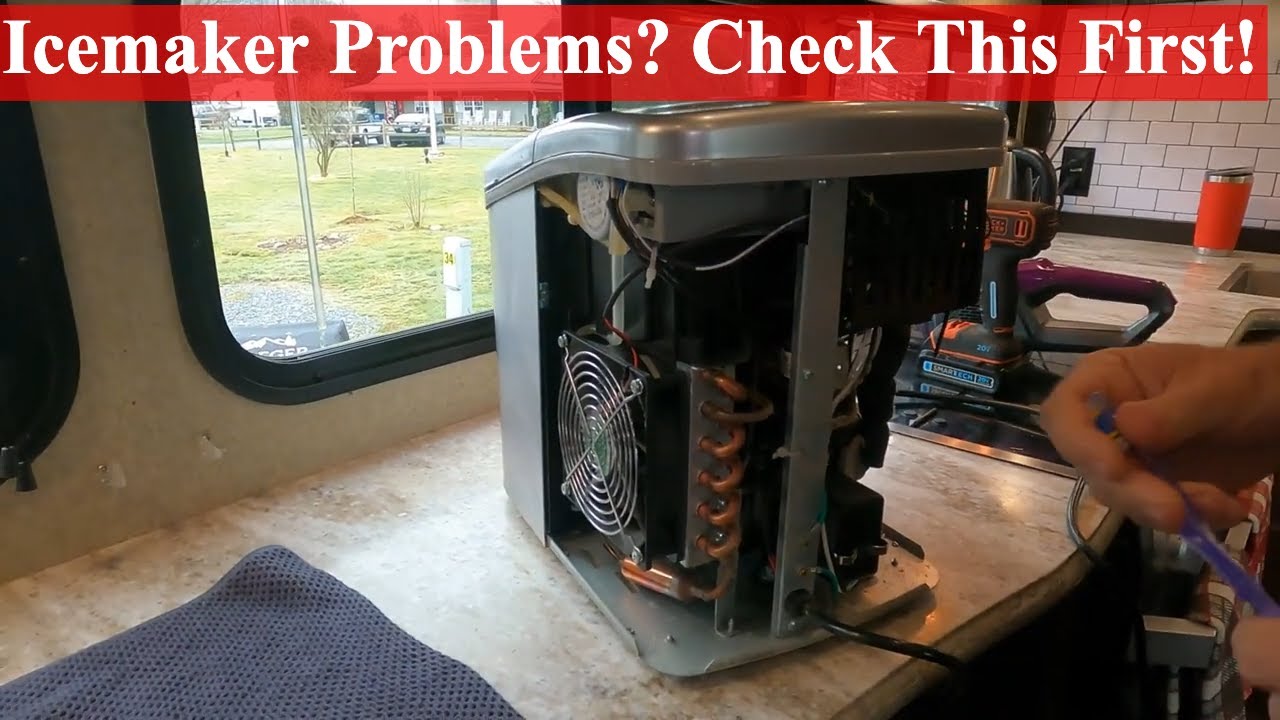
Credit: www.youtube.com
Conclusion
Fixing your Intertek ice maker can feel overwhelming, but it’s manageable. Start with basic checks like power and water supply. Clean the machine regularly to prevent clogs and ensure smooth operation. Refer to your manual for model-specific issues and solutions.
If problems persist, professional help might be necessary. Consistent maintenance reduces breakdowns and extends the life of your appliance. Troubleshooting doesn’t have to be complicated with a step-by-step approach. Keep your ice maker in top shape for reliable performance every time.