Mcquay Air Cooled Chillers Troubleshooting: Expert Solutions
Are you dealing with issues in your McQuay air-cooled chiller and feeling unsure about where to start? You’re not alone.
When your chiller isn’t performing as it should, it can disrupt operations, increase energy costs, and create unnecessary stress. But here’s the good news: troubleshooting your McQuay air-cooled chiller doesn’t have to feel overwhelming. In this guide, we’ll walk you through common problems, their possible causes, and practical steps you can take to get your system back on track.
Whether it’s unusual noises, temperature inconsistencies, or system shutdowns, we’ll help you pinpoint the issue and take action. Keep reading, because understanding these solutions could save you time, money, and a lot of headaches.
Common Issues In Air Cooled Chillers
Air cooled chillers are essential in various industries, but they’re not immune to problems. Identifying and resolving common issues can save you time, money, and energy. Let’s look at some of the most frequent challenges and practical solutions.
Refrigerant Leaks
Refrigerant leaks are one of the most common issues in air cooled chillers. When refrigerant levels drop, your chiller’s cooling efficiency takes a hit. You may notice higher energy bills or uneven cooling.
Regular inspections can help you catch leaks early. Use a leak detector or check for oil stains around fittings and connections. If you spot a leak, call a certified technician to fix it and recharge the system.
Compressor Failures
The compressor is the heart of your chiller, and when it fails, the system stops working. Overheating, electrical issues, or lack of proper lubrication often cause these failures.
Monitor for unusual noises or frequent cycling as warning signs. Ensure your system has clean filters and proper ventilation to prevent overheating. If the compressor fails, replacing it might be your only option, so early prevention is key.
Faulty Sensors
Sensors control various operations in your chiller, from temperature to pressure. Faulty sensors can lead to incorrect readings, resulting in poor performance or complete shutdowns.
Test sensors regularly to ensure they’re accurate. Replace any damaged or malfunctioning sensors promptly. A well-calibrated sensor keeps your chiller running smoothly and avoids unnecessary disruptions.
Electrical Malfunctions
Electrical issues can cripple your chiller, causing erratic behavior or total failure. Loose connections, blown fuses, or worn-out wiring are common culprits.
Inspect electrical components routinely to spot potential problems early. Tighten loose connections and replace damaged wires immediately. Don’t ignore frequent power trips—they might signal a deeper electrical issue that needs attention.
Which of these issues have you faced with your air cooled chiller? Addressing these problems early can make all the difference in extending the life of your system.
Signs Of Chiller Malfunction
McQuay air-cooled chillers are reliable, but like any equipment, they can show signs of trouble. Recognizing these early can save you from costly repairs and downtime. Let’s dive into the most common signs of malfunction and what they mean for your system.
Inconsistent Cooling
Does your chiller struggle to maintain a steady temperature? This could be a sign of clogged filters or low refrigerant levels. When cooling fluctuates, your building’s comfort and productivity can suffer.
Check if certain areas are warmer than others, even when the system is running. A simple maintenance check might uncover blocked coils or airflow issues. Addressing these promptly can restore efficiency.
Unusual Noises
Strange noises like rattling, buzzing, or squealing can indicate mechanical problems. Loose components, worn-out fans, or failing compressors might be the culprit. Ignoring these sounds can lead to bigger issues down the line.
Next time you hear something unusual, don’t brush it off. Open the chiller panel and inspect for visible issues. If you’re unsure, calling in a technician can prevent further damage.
High Energy Consumption
Have your electricity bills spiked recently? A malfunctioning chiller often consumes more energy than normal. Dirty condenser coils or inefficient compressors could be draining your system’s power.
Track your energy usage over time. If there’s a noticeable jump, inspect the chiller for buildup or aging components. Regular cleaning and calibration can keep your system running smoothly.
Frequent System Shutdowns
If your chiller keeps shutting down unexpectedly, it’s a red flag. Overheating, electrical faults, or insufficient refrigerant may be causing the issue. These interruptions can halt operations and affect your bottom line.
Ask yourself—how often is this happening? Frequent shutdowns could mean the system is due for a thorough diagnostic. Don’t delay; acting quickly can prevent permanent damage.
Spotting these signs early can save you time, money, and headaches. So, keep your eyes and ears open. What’s the most persistent issue you’ve faced with your chiller, and how did you handle it?
Diagnosing Performance Problems
Diagnosing performance problems in a McQuay air-cooled chiller can feel overwhelming, but it doesn’t have to be. Breaking the process into smaller checks can help you pinpoint the issue faster. By focusing on key areas like refrigerant levels, compressor health, and control settings, you can get your chiller back to optimal performance without unnecessary guesswork.
Inspecting The Refrigerant System
Low refrigerant levels are a common cause of performance issues. Check for visible signs of leaks, like oil stains around fittings or connections. If you suspect a leak, use a leak detector to confirm before adding more refrigerant.
Also, ensure the refrigerant type matches the manufacturer’s specifications. Using the wrong refrigerant can compromise efficiency and even damage the system. A quick review of the unit’s manual will save you potential trouble later.
Monitoring Pressure Readings
Pressure readings can tell you a lot about your chiller’s health. Use a gauge to check both the high and low-pressure sides of the system. If the readings are outside the recommended range, it could indicate blockages, overcharging, or undercharging.
For instance, abnormally high pressures might suggest a dirty condenser or improper airflow. On the other hand, low pressures could mean a refrigerant shortage or a restriction in the system. Always compare your readings to the manufacturer’s guidelines for accuracy.
Evaluating Compressor Health
The compressor is the heart of your chiller. If it’s not performing well, the entire system will suffer. Listen for unusual noises, like knocking or rattling, which might indicate internal wear or damage.
You can also measure the voltage and amperage to ensure they’re within the recommended range. If the compressor is overheating or tripping the circuit, it could be a sign of electrical issues or overload. Address these problems quickly to avoid costly repairs.
Checking Control Settings
Control settings often get overlooked, but they can be the root cause of many issues. Verify that the temperature and pressure setpoints align with your application’s requirements. Incorrect settings can lead to inefficient operation or system shutdowns.
Also, check for error codes on the control panel. These codes can guide you directly to the problem area. Resetting the system after adjustments can help you confirm whether the issue is resolved.
What’s the one area you tend to skip during troubleshooting? Addressing even small oversights can make a big difference in your chiller’s performance.
Preventive Maintenance Tips
Preventive maintenance is key to keeping McQuay air-cooled chillers efficient. Regular upkeep reduces downtime and extends the equipment’s life. It also ensures consistent cooling performance. Neglecting maintenance often leads to costly repairs and energy inefficiency. Below are practical tips to maintain your chiller effectively.
Regular Cleaning Of Condenser Coils
Dirty condenser coils reduce heat transfer and strain the chiller. Clean the coils at least twice a year to ensure efficient operation. Use a soft brush or low-pressure water to remove debris. Avoid using high-pressure water, as it can damage the fins. For areas with heavy dust or pollen, clean more frequently.
Lubricating Moving Parts
Proper lubrication minimizes wear and tear on moving components. Lubricate fan motors, bearings, and other moving parts regularly. Use the recommended type and amount of lubricant for your chiller model. Over-lubrication can also cause problems, so always follow the manual.
Ensuring Proper Airflow
Blocked airflow can overheat the chiller and reduce efficiency. Inspect and clear obstructions around the unit, such as leaves or debris. Ensure a minimum clearance around the chiller as specified by the manufacturer. Check the air filters and clean or replace them when necessary.
Scheduling Routine Inspections
Routine inspections help identify potential issues before they become major problems. Schedule professional inspections at least once a year. Technicians can check refrigerant levels, electrical connections, and overall system performance. Document all inspections for future reference and maintenance planning.
Advanced Troubleshooting Techniques
When it comes to troubleshooting McQuay air-cooled chillers, basic methods can only take you so far. Advanced troubleshooting techniques give you deeper insights into performance issues and help you resolve them faster. These methods leverage technology and systematic approaches to pinpoint problems effectively and prevent downtime.
Using Diagnostic Software
Diagnostic software can be a game-changer for troubleshooting McQuay chillers. Most modern chillers come equipped with built-in software that provides real-time data. You can use this software to monitor temperature fluctuations, pressure readings, and compressor performance without manually inspecting every component.
Look for error codes displayed on the chiller’s interface. These codes can guide you to the exact issue. For instance, if the software shows a high-pressure alarm, you can focus on the condenser or refrigerant levels. Always update the software regularly to ensure accurate diagnostics.
Testing Electrical Components
Electrical issues are common in air-cooled chillers, but testing components can help you pinpoint them. Use a multimeter to check voltage levels and continuity across wires and terminals. This ensures all electrical connections are functioning as expected.
Pay close attention to the contactors and relays. If they’re worn out or have burnt contacts, they can disrupt power flow. Replace faulty components immediately to avoid further damage to the system.
Analyzing System Logs
System logs often contain valuable information that’s easy to overlook. These logs track operational data over time, showing patterns that may indicate problems. For example, recurring temperature spikes might point to a failing compressor or clogged filters.
Review the logs regularly and compare them with past performance. This allows you to identify trends and fix minor issues before they become major problems. Don’t forget to save these logs for future reference.
Identifying Recurring Issues
Recurring issues can drain your time and resources if not addressed properly. Start by listing the problems that happen repeatedly, such as frequent shutdowns or unusual noises. These patterns often suggest deeper system faults.
Ask yourself: are these issues tied to specific components or operating conditions? For example, if shutdowns occur during peak hours, the system might be struggling with load capacity. Fixing the root cause is always more effective than temporary solutions.
Advanced troubleshooting isn’t just about finding problems; it’s about understanding your system better. What techniques do you already use, and how could they be improved? Let us know your thoughts in the comments below!
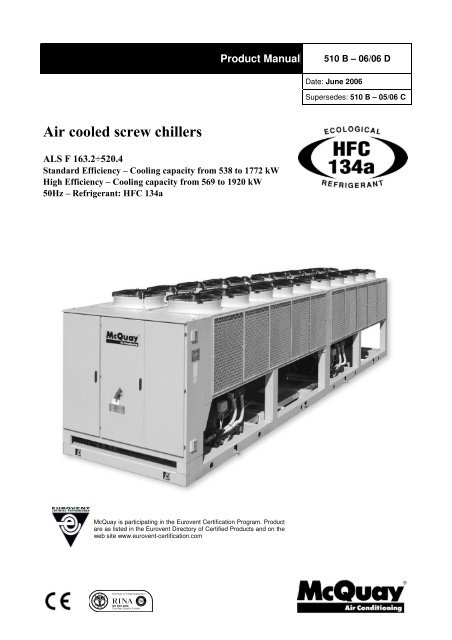
Credit: www.yumpu.com
When To Call A Professional
McQuay air-cooled chillers are designed to offer reliable cooling, but even the best systems can face issues. Some problems are simple to fix, like cleaning dirty filters or resetting a tripped breaker. But others require the expertise of a trained professional to ensure safety and prevent further damage. Knowing when to step back and call an expert can save you time, money, and unnecessary stress.
Persistent Refrigerant Problems
If your chiller consistently struggles with refrigerant issues, it’s time to get help. Low refrigerant levels might indicate a leak, which can harm the system and the environment. A professional can locate and repair leaks, recharge the system, and ensure proper refrigerant pressure for efficient performance.
Major Component Failures
Has your compressor stopped working? Is the condenser fan making unusual noises? These are major component failures that need immediate professional attention.
Replacing or repairing large components without the proper knowledge can lead to further damage. For example, mishandling a compressor replacement could void your warranty. Always call a certified technician for such critical repairs.
Complex Electrical Issues
Electrical problems can be tricky and dangerous. If your chiller isn’t powering on or frequently trips breakers, the issue likely lies in the electrical system. This could involve wiring, fuses, or even the control board.
Attempting to fix electrical problems without training can pose serious safety risks. Leave these tasks to a professional who can diagnose and repair the system without compromising safety.
System Not Responding To Repairs
Have you tried basic troubleshooting steps, but the system still doesn’t work? This could indicate deeper, underlying problems that require a professional’s expertise. Ignoring persistent issues can lead to bigger, more expensive repairs later.
Sometimes, what seems like a simple problem may mask a larger issue. A professional technician can perform a thorough inspection to identify and resolve the root cause, ensuring your chiller operates efficiently again.
Knowing when to call a professional isn’t just about fixing the problem—it’s about protecting your equipment and ensuring long-term reliability. Are you confident your system is in good hands?
Upgrading Or Replacing The Chiller
McQuay air-cooled chillers are critical for maintaining efficient cooling systems. Over time, wear and tear can reduce performance. Upgrading or replacing the chiller can ensure reliability and improve energy efficiency. Making the right decision depends on evaluating repair costs, assessing system lifespan, and selecting the right model.
Evaluating Repair Costs
Repair costs can sometimes exceed the value of the chiller itself. Frequent breakdowns mean higher expenses for parts and labor. Compare repair costs with the price of a new unit. Assess whether repairs will extend the chiller’s usefulness or just delay replacement.
Assessing System Lifespan
Older chillers often consume more energy and require frequent maintenance. Check the age of your system and its overall condition. If the chiller is over 15 years old, replacement may be more practical. Newer models often provide better performance and lower operating costs.
Choosing Energy-efficient Models
Energy-efficient chillers can reduce utility bills and environmental impact. Look for models with advanced features like variable speed drives. Check energy ratings to ensure compliance with modern standards. Investing in efficiency can provide long-term savings.
Planning For Installation
Proper installation ensures the chiller performs optimally from day one. Evaluate the space requirements and cooling capacity needs. Coordinate with professionals to avoid disruptions during the installation process. Ensure the system integrates seamlessly with existing equipment.
Credit: www.scribd.com

Credit: www.youtube.com
Frequently Asked Questions
How To Troubleshoot Mcquay Air Cooled Chillers Not Cooling?
Start by checking the thermostat and refrigerant levels. Inspect for clogged filters, blocked airflow, or compressor issues. Ensure the chiller is properly maintained and all electrical connections are secure. Address any error codes displayed on the control panel for specific problems.
Why Is My Mcquay Chiller Making Loud Noises?
Loud noises often indicate loose components, worn-out bearings, or refrigerant issues. Check the fans, compressors, and motors for damage. Perform routine maintenance and tighten loose parts. If the noise persists, consult a qualified technician for further inspection.
What Causes Frequent Shutdowns In Mcquay Air Cooled Chillers?
Frequent shutdowns may result from overheating, electrical faults, or low refrigerant levels. Ensure proper airflow around the chiller and clean filters regularly. Verify power supply stability and inspect error codes to identify specific problems.
How Can I Fix Mcquay Chiller Low Refrigerant Issues?
Low refrigerant issues are often caused by leaks. Inspect piping and connections for damage or cracks. Seal leaks promptly and recharge refrigerant to recommended levels. Regular maintenance can prevent recurring refrigerant loss.
Conclusion
Proper troubleshooting keeps McQuay air-cooled chillers running efficiently. Addressing issues early prevents costly repairs and downtime. Regular maintenance ensures longer equipment life and consistent performance. Always follow the manufacturer’s guidelines for best results. Pay attention to unusual noises, leaks, or temperature changes.
These signs often indicate underlying problems. Skilled technicians can help resolve complex issues quickly. A well-maintained system boosts energy efficiency and reduces operational costs. Stay proactive and monitor your chiller’s performance regularly. Reliable operation starts with careful attention and timely action.