Sloan Flush Valve Troubleshooting: Fix Common Issues Now!
Sloan flush valve troubleshooting is essential for maintaining proper functionality. Begin by inspecting the valve for any visible obstructions or damage. Check the water supply to ensure it’s turned on and delivering adequate pressure. If the flush is weak or inconsistent, clean or replace the diaphragm assembly.
Leaks may indicate loose connections or worn seals, which can often be resolved by tightening or replacing them. For persistent issues, consult the manufacturer’s troubleshooting guide or contact Sloan customer support for assistance. Regular maintenance, including cleaning and inspection, is key to preventing problems and extending the life of your flush valve system. By promptly addressing any issues and keeping up with routine care, you can ensure your Sloan flush valve operates efficiently and reliably for years to come.
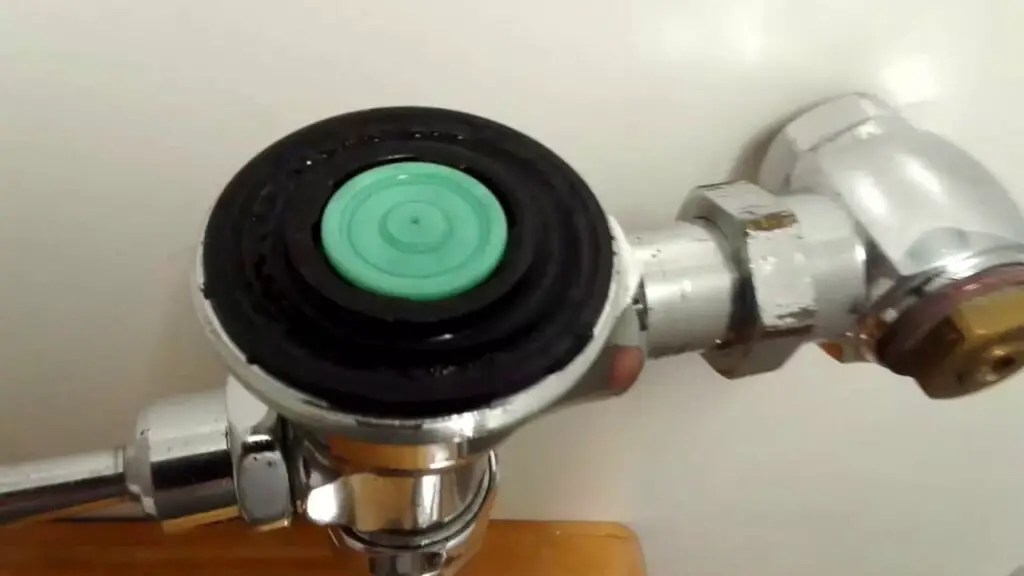
Understanding Sloan Flush Valves
Sloan flush valves are an essential component of commercial toilets and urinals, ensuring efficient and hygienic flushes in high-traffic areas. However, like any mechanical system, flush valves can encounter problems over time. Understanding how Sloan flush valves work and the importance of proper water flow is crucial for troubleshooting and maintaining their functionality.
How Do Sloan Flush Valves Work?
Sloan flush valves operate using a diaphragm and control stop mechanism to regulate water flow. When a user activates the flush lever or sensor, it lifts the control stop, allowing water to flow from the supply line into the valve. The water then fills the diaphragm chamber, causing the diaphragm to rise and push the valve open, allowing the water to enter the fixture and facilitate the flush. Once the flushing cycle is complete, the diaphragm lowers, closing the valve and stopping the water flow.
In addition to manual flush valves, Sloan also offers sensor-operated flush valves. These flush valves use infrared sensors to detect user presence and initiate the flushing process automatically. The sensor detects when the user leaves the vicinity, prompting the valve to close and prevent water waste.
The Importance Of Proper Water Flow In Sloan Flush Valves
Proper water flow is crucial for the optimal operation of Sloan flush valves. Inadequate flow or excessive flow can lead to various issues and affect the overall functionality of the valve. Here are a few reasons why proper water flow matters:
- Efficiency: Inadequate water flow can result in incomplete flushes, leaving behind residues and causing foul odors. Proper water flow ensures a thorough and effective flush every time.
- Water conservation: excessive water flow can lead to waste, increase water bills, and strain water resources. Maintaining the recommended water flow rates of Sloan flush valves helps conserve water while providing optimal performance.
- Durability: Improper water flow can put unnecessary strain on the diaphragm and control stop, leading to premature wear and tear. By ensuring the right water flow, you can extend the lifespan of your Sloan flush valve.
If you encounter issues with water flow in your Sloan flush valve, it is essential to troubleshoot and address the problem promptly. Depending on the specific issue, adjustments to the control stop, diaphragm replacement, or cleaning the valve may be required. Regular maintenance and monitoring of water flow can help prevent costly repairs and guarantee the smooth operation of your Sloan flush valve.
Common Issues With Sloan Flush Valves
Sloan flush valves are known for their durability and reliability, but like any plumbing fixture, they can experience problems over time. Understanding these common issues and knowing how to troubleshoot them can save you time and money. In this section, we will explore some of the most commonly encountered issues with Sloan flush valves and provide step-by-step solutions to resolve them.
Continuous Flushing: Causes And Solutions
Continuous flushing is a frustrating problem that can lead to water wastage and high water bills. There are a few possible causes for this issue. One common cause is a faulty flushometer diaphragm, which may need to be replaced. Another potential cause is a damaged control stop, which can prevent the valve from closing properly. To fix this issue, follow these steps:
- Turn off the water supply to the flush valve.
- Remove the flushometer cover.
- Inspect the diaphragm for any signs of damage or wear.
- If the diaphragm is damaged, replace it with a new one.
- Examine the control stop for any cracks or defects.
- If the control stop is damaged, replace it.
- Reassemble the flushometer and turn on the water supply.
Shortage Of Water: Troubleshooting And Fixing The Issue
If you are experiencing a shortage of water when flushing your Sloan flush valve, it could be due to a few different factors. One common cause is a clogged inlet screen, which can restrict the flow of water into the valve. To troubleshoot and fix this issue, follow these steps:
- Turn off the water supply to the flush valve.
- Remove the flushometer cover.
- Locate the inlet screen and inspect it for any debris or sediment.
- If the screen is clogged, remove it and clean it thoroughly.
- Reinstall the screen and reassemble the flushometer.
- Turn on the water supply and test the flush valve.
Excessive Water Flow: Identifying The Problem And Resolving It
Excessive water flow from a Sloan flush valve can result in water waste and potential damage to the plumbing system. One possible cause for this issue is a faulty flow control, which regulates the amount of water released during each flush. To identify and resolve this problem, follow these steps:
- Turn off the water supply to the flush valve.
- Remove the flushometer cover.
- Inspect the flow control for any signs of damage or wear.
- If the flow control is damaged, replace it with a new one.
- Reassemble the flushometer and turn on the water supply.
- Test the flush valve to ensure it is not releasing excessive water.
Flushometer Won’t Flush: Troubleshooting Steps To Fix The Problem
If your Sloan flushometer is not flushing at all, there are several possible causes. One common issue is a blocked flush valve orifice, which can prevent water from flowing properly. To troubleshoot and resolve this problem, follow these steps:
- Turn off the water supply to the flush valve.
- Remove the flushometer cover.
- Inspect the flush valve orifice for any debris or obstructions.
- If the orifice is blocked, use a small wire or brush to remove the debris.
- Reassemble the flushometer and turn on the water supply.
- Test the flush valve to ensure it is flushing correctly.
By following these troubleshooting steps, you can effectively address the common issues that may arise with your Sloan flush valve. Remember to always turn off the water supply before working on the flush valve, and if you are unsure about any steps, consult a professional plumber.
Troubleshooting Sloan Regal Flushometers
Step-by-step Guide To Troubleshooting Sloan Regal Flushometers
If you’re experiencing issues with your Sloan Regal flushometer, don’t worry – troubleshooting the problem can often be done on your own without the need for a professional plumber. In this step-by-step guide, we’ll walk you through the common issues that can arise with Sloan Regal flushometers and how to fix them.
1. Continuous Flushing
If your Sloan Regal flushometer is continuously flushing, it could be due to a problem with the control stop. To fix this issue, start by adjusting the control stop so that it can fully open as intended. If adjusting the control stop doesn’t solve the problem, you may need to replace the control and/or the diaphragm kit.
2. Shortage Of Water
If your Sloan Regal flushometer is not getting enough water for flushing, the control stop and diaphragm kit may need to be checked. Make sure the control stop is fully opened and not obstructed. Additionally, inspect the diaphragm kit for any signs of damage or wear and replace it if necessary.
3. Excessive Water Flow
Excessive water flow from the Sloan Regal flushometer can occur if the control stop is not properly adjusted. Start by adjusting the control stop to decrease the water flow. If adjusting the control stop doesn’t solve the problem, consider replacing the control and/or the diaphragm kit.
4. Flushometer Won’t Flush
If your Sloan Regal flushometer won’t flush at all, check the control stop first. Ensure it is fully opened and not blocked or obstructed. If the control stop is functioning properly, inspect the diaphragm kit for any damage or wear. If necessary, replace the diaphragm kit to solve the flushing issue.
Remember, proper maintenance and regular inspections can help prevent most problems with Sloan Regal flushometers. If you have followed these troubleshooting steps and are still experiencing issues, it may be time to consult a professional plumber for further assistance.
Troubleshooting Sloan Optima Flushometers
Step-by-step Guide To Troubleshooting Sloan Optima Flushometers
Is your Sloan Optima flushometer giving you trouble? This step-by-step guide will help you troubleshoot common issues and get your flushometer back to proper functioning in no time.
-
Adjusting the sensor range and troubleshooting dead batteries
If your Sloan Optima flushometer is not activating or is activating too frequently, a simple adjustment of the sensor range might be all you need. To adjust the sensor range, follow these steps:
- Locate the sensor range adjustment dial, typically found on the side of the flushometer.
- Turn the dial clockwise to decrease the sensor range or counterclockwise to increase it.
- Test the flushometer to see if the adjustment has resolved the issue.
If adjusting the sensor range doesn’t solve the problem, it may be caused by dead batteries. Follow these steps to troubleshoot dead batteries:
- Locate the battery compartment on the top or side of the flushometer.
- Remove the battery cover using a screwdriver or your fingers, depending on the model.
- Replace the old batteries with fresh ones, making sure to insert them correctly according to the polarity markings.
- Close the battery compartment and test the flushometer. If the issue persists, further troubleshooting is needed.
-
Solenoid failure: Replacing the solenoid for proper functioning
If your Sloan Optima flushometer is not flushing at all, the solenoid may be the culprit. Follow these steps to replace the solenoid:
- Locate the solenoid assembly, typically located on the top or side of the flushometer.
- Using a wrench or pliers, carefully disconnect the supply hose from the solenoid.
- Unscrew the solenoid from the flushometer body, taking care not to damage any surrounding components.
- Install the new solenoid by screwing it into place and reconnect the supply hose.
- Test the flushometer to ensure proper functioning. If the issue persists, further troubleshooting or professional assistance may be required.
By following these troubleshooting steps, you can effectively diagnose and resolve common issues with your Sloan Optima flushometer. Remember to always refer to the manufacturer’s instructions and, if needed, seek professional assistance for more complex problems. Don’t let a malfunctioning flushometer cause inconvenience—take action and maintain a properly functioning bathroom.
Tips For Maintaining Sloan Flush Valves
Proper maintenance and care are essential for maintaining the optimal performance of Sloan flush valves. By following some regular maintenance practices and taking preventive measures, you can avoid common issues that may arise with these valves. Additionally, knowing the proper cleaning techniques will ensure that your Sloan flush valves remain in good condition for longer. In this article, we will explore these tips and provide valuable insights into maintaining your Sloan flush valves.
Regular Maintenance Practices For Optimal Performance
Sloan flush valves, like any other plumbing fixture, require regular maintenance to ensure they function properly and efficiently. Here are some maintenance practices you should follow to keep your Sloan flush valves in the best condition:
- Inspect the flush valves for any signs of damage or wear regularly. Look for leaks, cracks, or any other visible issues that may affect their performance.
- Check the water supply connections and make sure they are tight and secure. Loose connections can result in water leaks or improper flushing.
- Test the flush valves periodically to ensure they are flushing properly. Observe if the flushing action is strong and complete, and address any issues promptly.
- Clean the exterior surface of the valves regularly to prevent the buildup of dirt, grime, and mineral deposits, which can affect their functionality.
- Inspect the flush handle and replace it if necessary. A faulty or damaged handle can lead to inconsistent flushing or difficulty in triggering the flush valve.
- Keep the surrounding area of the flush valves clean and free from any obstructions or debris that may interfere with their operation.
- Consider scheduling professional maintenance checks for your Sloan flush valves, especially if you have a large commercial or institutional facility with multiple valves.
Preventive Measures To Avoid Common Issues
In addition to regular maintenance, taking preventive measures can help you avoid common issues associated with Sloan flush valves. Here are some preventive measures you should implement:
- Keep an eye on the water pressure in your facility. Excessive water pressure can cause damage to the flush valves, leading to leaks and other issues. Ensure that the water pressure is within the recommended range specified by Sloan.
- Use a water filtration system to remove impurities in the water supply. Accumulation of sediments and minerals can clog the flush valves and affect their performance. Regularly replace or clean the filters as per the manufacturer’s instructions.
- Educate facility users about the proper use of the flush valves. Discourage the use of excessive force on the flush handles and instruct users on how to trigger a complete flush.
- Train your maintenance staff on the proper maintenance procedures for Sloan flush valves. This will ensure that they handle any issues promptly and efficiently.
- Consider installing water-saving devices or retrofit kits on your Sloan flush valves. These devices can help reduce water consumption and prolong the lifespan of your valves.
- Regularly monitor the performance of the flush valves and address any issues immediately to prevent further damage or costly repairs.
Proper Cleaning Techniques For Sloan Flush Valves
Cleaning your Sloan flush valves properly is vital for their efficient operation and longevity. Follow these techniques for effective cleaning:
Step | Procedure |
---|---|
1 | Turn off the water supply to the flush valve. |
2 | Remove the flush valve cover or access panel. |
3 | Inspect the interior for any visible debris or mineral deposits. |
4 | Use a non-abrasive cleaner and a soft brush to clean the valve components. Pay special attention to the diaphragm, seals, and other movable parts. |
5 | Rinse the valve components thoroughly with clean water. |
6 | Reassemble the flush valve and turn on the water supply. |
7 | Test the valve to ensure it is functioning properly. |
Regular maintenance, preventive measures, and proper cleaning techniques are crucial for maintaining Sloan flush valves. By following these tips, you can ensure the optimal performance and longevity of your flush valves, minimizing the chances of costly repairs or replacements. Implement these practices in your facility to keep your Sloan flush valves in excellent working condition.
Frequently Asked Questions
A Sloan toilet may not flush due to a shortage of water, excessive water flow, or a flushometer that won’t flush. Troubleshooting steps include adjusting the sensor range, changing batteries, checking the solenoid, and adjusting the control stop. If these steps don’t work, the control and/or diaphragm kit may need to be replaced.
How To Fix A Sloan Automatic Flush Valve?
To fix a Sloan automatic flush valve, first adjust the control stop to ensure it is fully open. If it still doesn’t work properly, consider replacing the control stop and/or diaphragm kit. Leaking from below the vacuum breaker may indicate a worn or degraded vacuum breaker sack.
Raise the supply or reduce sensor range if the sensor is detecting the front of the toilet. Check out Sloan’s troubleshooting guides for more assistance.
Why Does My Sloan Urinal Flush Valve Keep Running?
To stop your Sloan urinal flush valve from running continuously, adjust the control stop so it can fully open. If that doesn’t work, you may need to replace the control stop and/or the diaphragm kit.
How Much Water Pressure Does A Sloan Flush Valve Need?
A Sloan flush valve requires a water pressure of approximately 25 to 80 psi for optimal performance.
Why Is My Sloan Flush Valve Not Working Properly?
If your Sloan flush valve is not working properly, it could be due to a clog in the valve or a malfunctioning diaphragm. Check for any obstructions or consider replacing the diaphragm.
Conclusion
Troubleshooting Sloan flush valves doesn’t have to be a headache. By following the steps and tips outlined in this blog post, you can quickly diagnose and resolve any issues with your Sloan flush valve. Whether it’s continuous flushing, shortage of water, excessive water flow, or a flushometer that won’t flush, this guide has got you covered.
Don’t let a faulty flush valve disrupt your bathroom experience. With the right troubleshooting techniques, you can keep your Sloan flush valve running smoothly and efficiently.